Air and vapor barriers both stop moisture transport by vapor diffusion through a home’s building envelope. However, only an air barrier prevents airflow (and the moisture attached to it) into the envelope. Airflow contains 50 to 100 times more water than that carried by vapor diffusion, emphasizing a home’s building envelope’s need for a high-quality air barrier and systems, like that offered by Poly Wall®.
Above- and below-grade walls both require a high-quality air barrier (R402.4.1.1). In addition, the climate zone determines the need for a vapor barrier on the interior side of framed walls (R702.7)
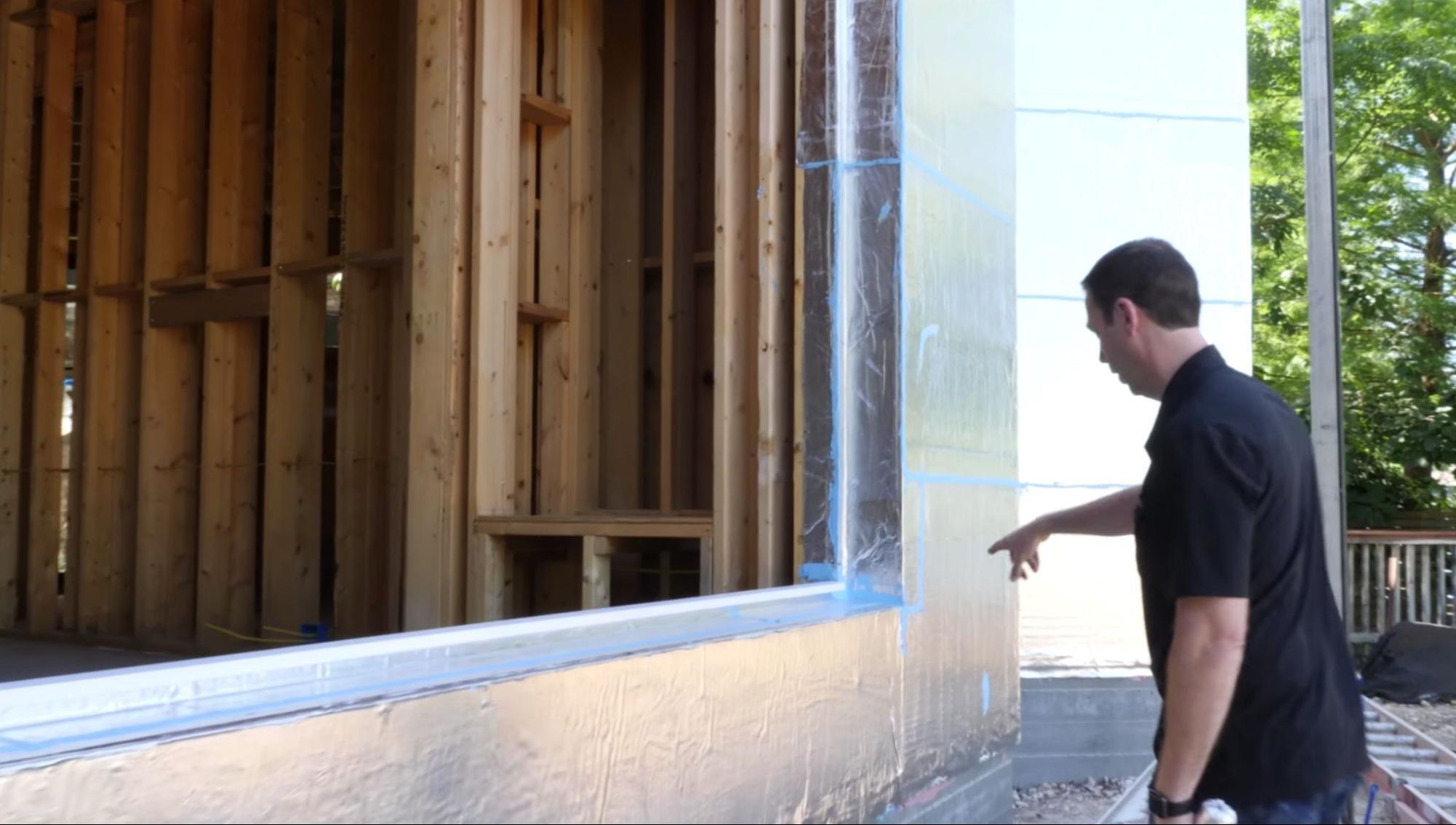
Defining Air Barriers
The 2021 International Residential Code (IRC) defines an air barrier as one or more materials joined together continuously to prevent airflow through the building's thermal envelope and its assemblies. In comparison, the IRC defines a continuous air barrier as one that includes a combination of materials and assemblies that restrict or stop the passage of air through the building envelope.
An air barrier’s air permeance should not exceed 0.02 L/(s·m²) at a pressure difference of 75 Pa (or 0.004 cfm/ft2 at a pressure difference of 1.56 lb/ft2) when tested following ASTM E 2178. Air permeance represents the quantity of air that infiltrates through a material. In contrast, air leakage is the air that passes through gaps and holes.
Why a House Needs an Air Barrier
An effective air barrier regulates the indoor climate by preventing the transfer of air (and the moisture attached to it) between the exterior and interior of a home. An air barrier must also stand up to the air pressure differences acting on them. They stop air from transporting moisture to the interior of a wall assembly, preventing condensation and the damaging effects of moisture accumulation. They are essential to waterproofing new foundation walls.
The Design of a High-Quality and Effective Air Barrier
The design of an air barrier must control air, heat, moisture flow, and solar radiation to effectively manage the interactions between the building’s physical elements, its occupants, and the environment.
A quality air barrier minimizes heat losses and gains through convections, convection, and radiation:
Thermal convection occurs when heat energy from a warmer space flows to a cooler area by the movement of fluids (usually liquids and gases).
Thermal conduction happens when hot molecules move towards cooler molecules. The effective R-value of a building's wall assembly represents its resistance to conduction.
Thermal radiation transfers heat from warm spaces to cool spots by electromagnetic waves (primarily the sun’s radiation).
Four vital features of a high-quality air barrier include:
Structural integrity (durability) over the expected lifetime of the home
Continuous over the entire home’s building enclosure
Impermeable to airflow
The strength and stiffness to withstand forces acting on them during and after construction
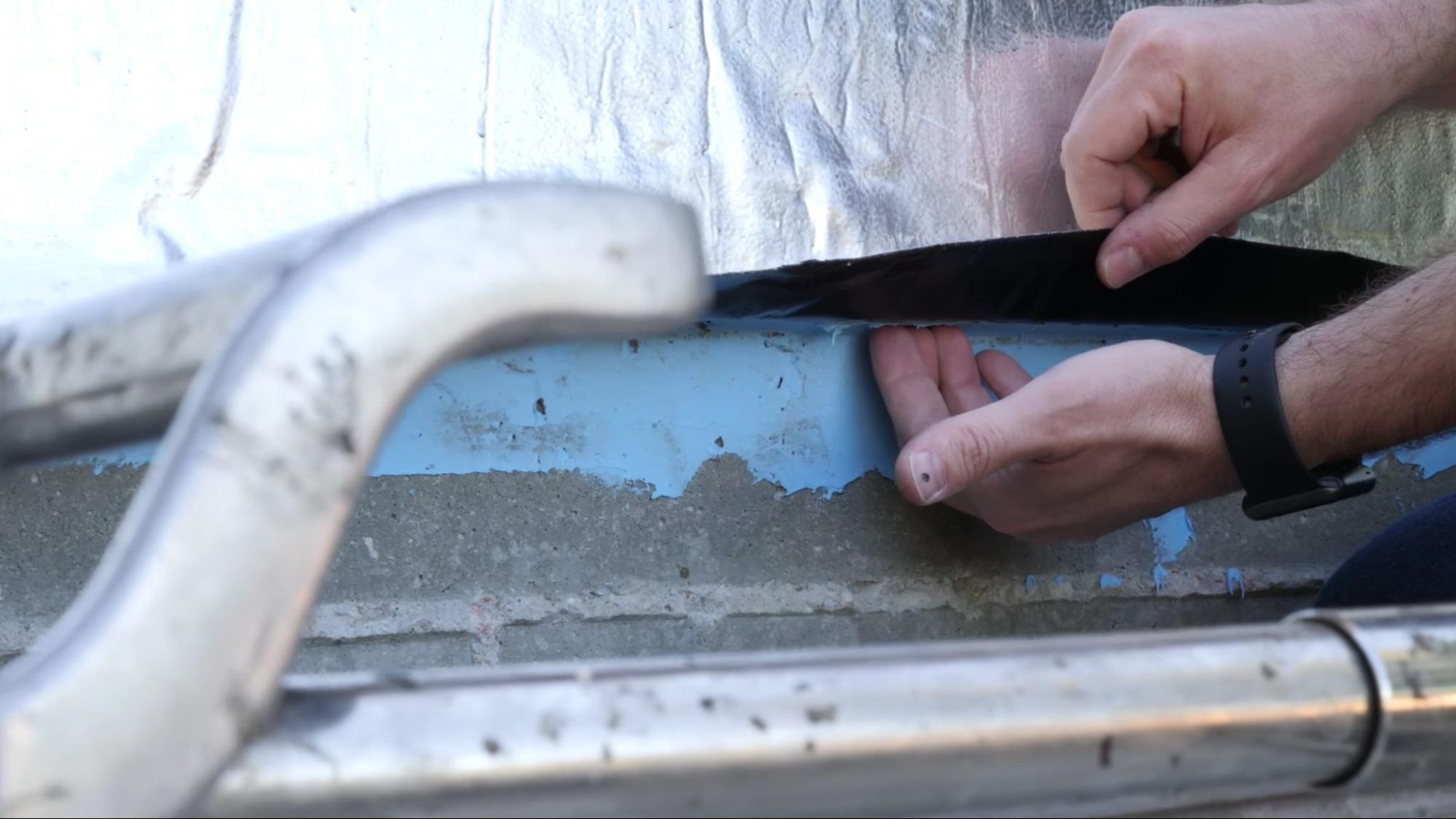
A continuous air barrier system aims to control heat, moisture, and air transfer by providing a continuous airtight building envelope that separates the unheated and heated spaces between all the building enclosure components. The building enclosure includes the below- and the above-grade elements that physically separate the interior and exterior environments of the house.
The building enclosure includes three interactive components (the exterior and interior environment and the enclosure system) and five structural systems:
Above-grade wall
Roof
Windows, skylights, and doors
Below-grade wall
Base floor
Air Barrier Code Requirements
The International Residential Code (IRC) and the International Building Code (IBC) provide code requirements for residential and commercial buildings.
Residential Buildings
The 2021 IRC (Table R402.4.1.1) mandates installing a continuous air barrier in a building envelope, along with the sealing breaks for joints in the air barrier.
IRCs apply to detached one-and-two family dwellings and townhouses no more than three stories above grade plane in height. In addition, they should have a separate means of egress with accessory structures no more than three stories above grade plane in height.
Commercial Buildings
The 2021 IBC, Section C402.5.1, mandates a continuous air barrier throughout the building envelope for commercial buildings (except climate zone 2B). Moreover, builders can place air barriers inside or outside the building envelope, within the assemblies composing the envelope, or any combination thereof. The air barrier must comply with Sections C402.5.1.1 and C492.5.1.2.
The IBCs apply to all buildings or structures that do not conform to the prescriptive provisions of the IRC.
Defining Vapor Barriers
Vapor barriers stop vapor diffusion, which occurs when moisture flows from either a space of higher moisture concentration towards an area of lower concentration. It can also happen when moisture flows from a hotter to a cooler area within a building material like insulation. Vapor barriers that prevent diffusion should not be confused with vapor retarders, which only slow vapor diffusion.
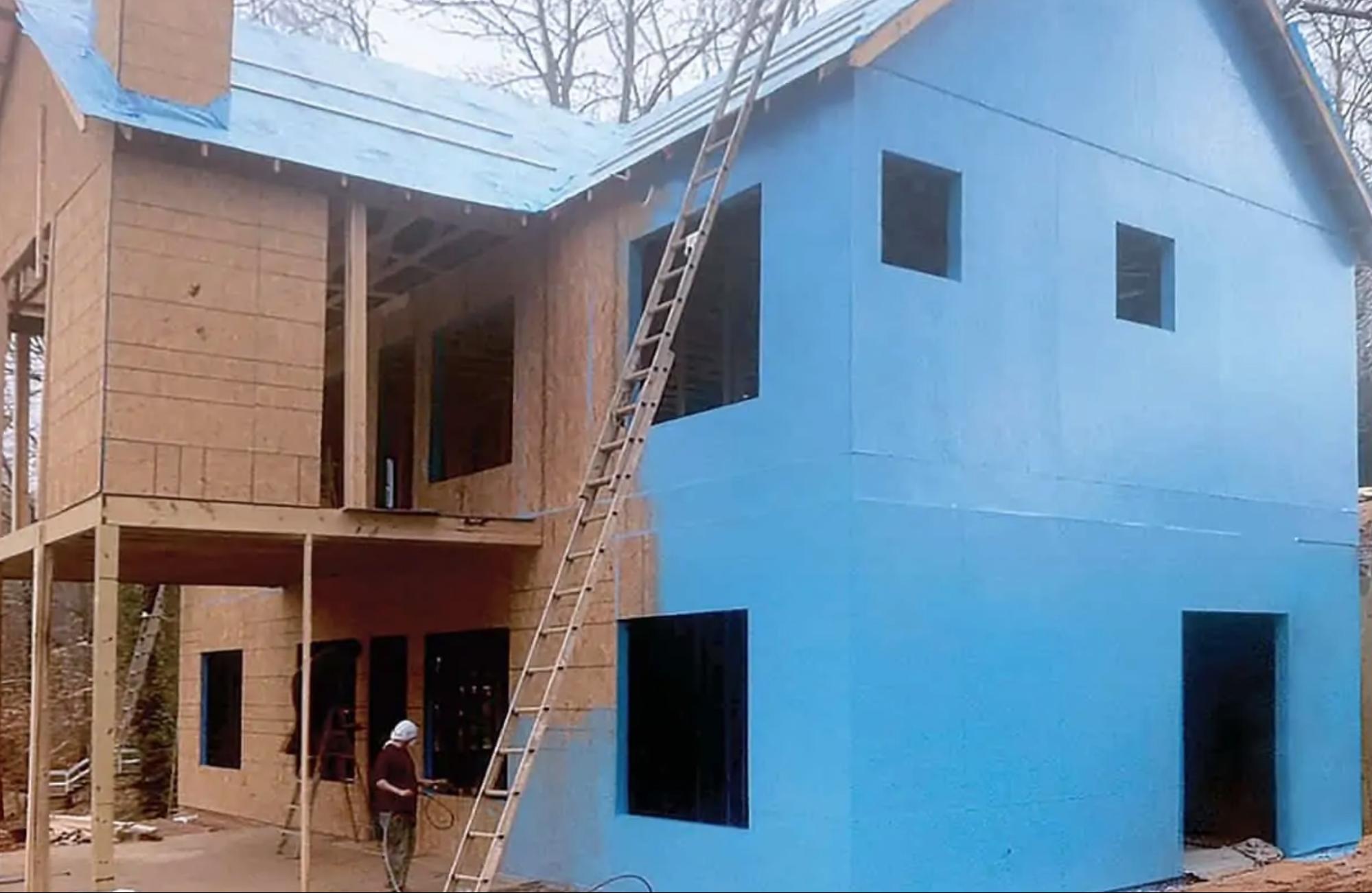
The ASTM E96 desiccant method determines a material's ability to restrict moisture from passing through it, assigning it a vapor retarder (barrier) class:
Class I vapor barrier: 0.1 perm or less
Class II vapor retarder: 0.1 < perm <1.0 perm
Class III vapor retarder: 1.0 < perm <10 perm
Typically, builders place vapor barriers (like polyethylene) on the interior wall and ceiling insulation to prevent vapor diffusion into the wall systems during the cold winter months when the inside of a house is warmer than the air within the wall assembly.
Do Walls Need Vapor Barriers?
A 2018 report from Denmark studied the influence of vapor diffusion and driving rain on the flow of moisture and heat through a permeable and hygroscopic building envelope. A permeable building envelope permits vapor diffusion, while a hygroscopic building envelope can absorb and store water from the surrounding air.
The study found that a vapor barrier did not significantly change the moisture content of the wall system. Moreover, of the four mechanisms for moisture transfer into the wall system (air movement, liquid flow, capillary suction, and vapor diffusion), vapor diffusion represented the smallest amount, so was less likely to cause severe damage to a house.
Code Requirements for Vapor Barriers
Deciding to use a vapor barrier on a building's interior or exterior depends on the climate zone. For example, the 2021 International Building Code (IBC) 1404.3 and the 2021 International Residential Code(IRC) R702.7 instruct Class I or II vapor barriers and retarders inside frame walls in climate zones 5,6,7,8 and Marine 4. However, southern climate zones 1, 2, and 3 do not mandate vapor barriers and retarders.
Effectively Stopping Air and Moisture Infiltration with Poly Wall® Waterproofing Systems
Poly Wall® Building Solutions (a division of Polyguard) provides homeowners quality protection against air and moisture infiltration for both above- and below-wall systems, ensuring a superior building envelope and the long-term integrity of the building or home. Poly Wall®’s air and moisture barrier systems include air barriers, below-grade waterproofing systems, liquid flashings, and window and door sheet flashings.
Poly Wall® Air Barriers
For over ten years, Poly Wall® has successfully waterproofed above-grade residential walls in hot and humid climate zones 1, 2, and 3A with their self-adhering, non-permeable Aluma Flash Plus weather-resistant barriers. Poly Wall® also offers permeable Blue Barrier™ Liquid Wrap 2300 for application over surfaces and substrates like OSB, plywood, and exterior gypsum.
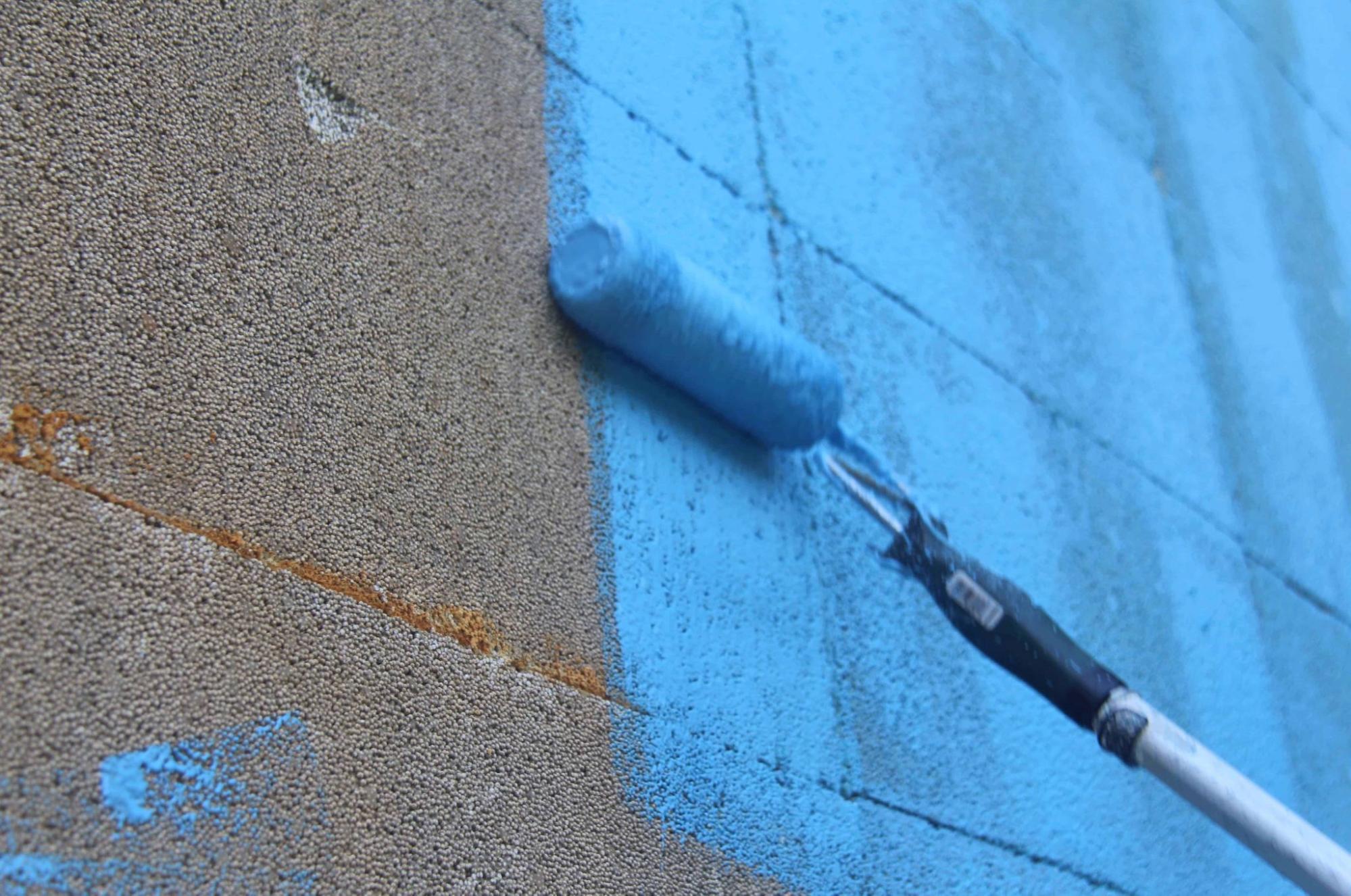
Aluma Flash™ Plus
Fast and straightforward to apply, sunlight- and chemical-resistant Aluma Flash™ Plus effectively adheres when used according to the manufacturer's installation and performance requirements. Aluma Flash™ Plus provides a 40-mil rubberized asphalt waterproofing membrane, laminated to two layers of high-strength polyethylene film, with a top protective layer of aluminum — making it a robust waterproofing product. In addition, the aluminum surface of durable Aluma Flash™ Plus works well with higher exposure houses because it reflects heat, cutting energy costs.
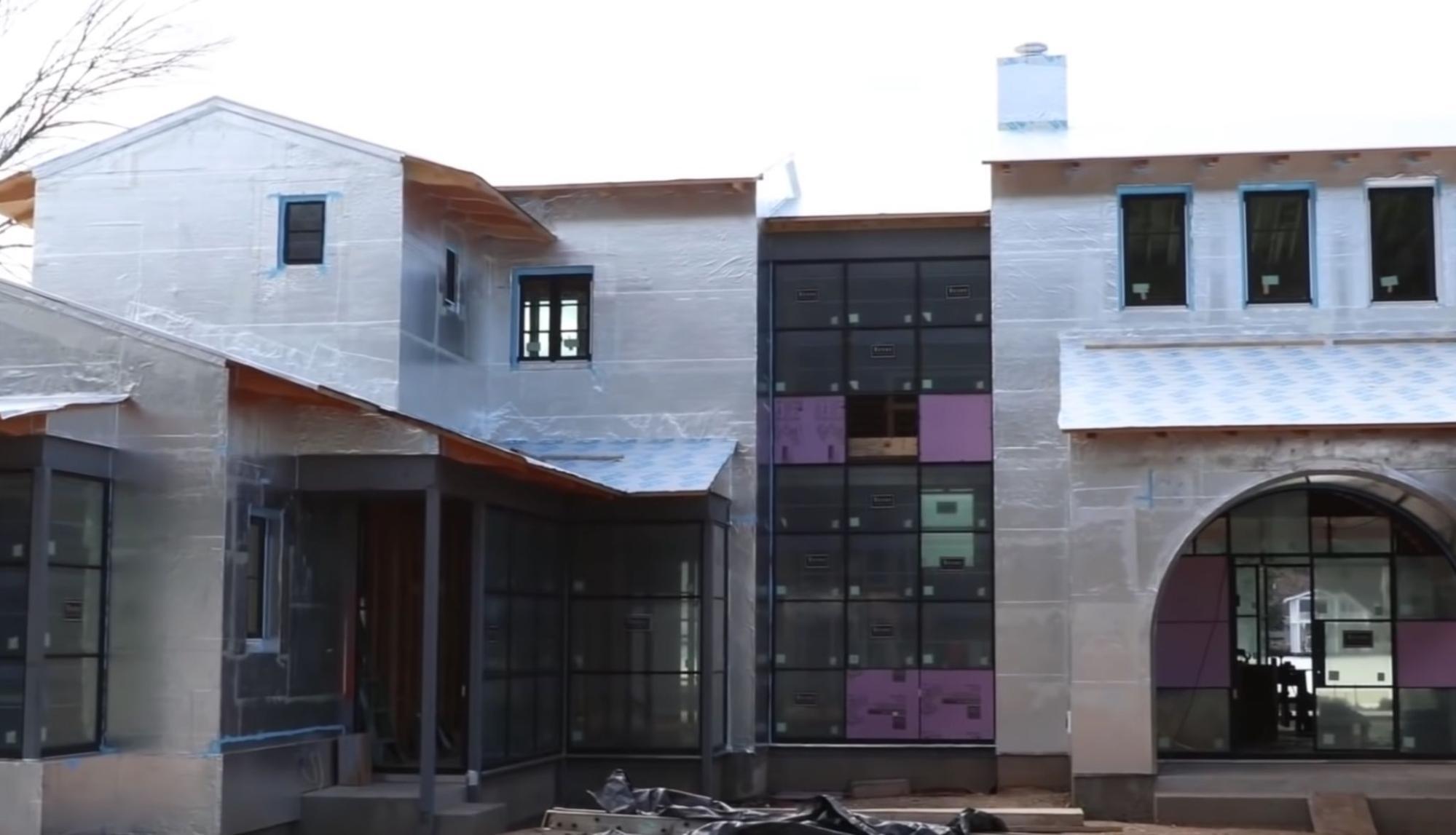
Poly Wall® Below-Grade Waterproofing Systems
Home Stretch™ ICF Waterproofing Membrane
Poly Wall® specifically designed and engineered Home Stretch™ ICF Waterproofing Membranes for ICF walls (insulated concrete form). However, it also provides an excellent waterproofing choice for poured walls and CMU (concrete masonry unit) foundation walls, along with other vital waterproofing applications or protection against hydrostatic pressure.
Easy to handle and install, Home Stretch™ contains a self-adhering, 40 mils thick sheet waterproofing membrane consisting of a strong, pliable high-density polyethylene (HDPE) facing bonded to a rubberized asphalt waterproofing compound.
To create a complete waterproofing system for your ICF, CMU, or poured concrete below-grade wall, Poly Wall® suggests using Home Stretch™ in combinations with their Detail Tape, Blue Barrier™ Gap Filler2200, Arroyo™ Drain Board, Arroyo™ Outlet Channel, Liquid Waterproofing, Water Based Liquid Adhesive, and Quick Grip.
Home Stretch™ Liquid Waterproofing
Poly Wall® designed Home Stretch™ Liquid Waterproofing for only below-grade poured concrete, precast concrete, CMU, and other vertical foundations surfaces exposed to hydrostatic pressure. For complete foundation wall waterproofing, Poly Wall® recommends using Home Stretch™ Liquid Waterproofing in combination with Blue Barrier™ Gap Filler2200, Arroyo™ Drain Board, Arroyo™ Outlet Channel, Arroyo™ Tee Outlet, and Arroyo™ End Outlet Channel System.
Poly Wall® Liquid Flashings Products
Poly Wall® offers several waterproof barrier systems for windows and doors, gaps, and penetrations:
All-purpose, trowel-grade, fluid-applied Poly Wall® Blue Barrier™ Liquid Flashing 2100 trowel-grade creates a weather-resistant, fully adhered waterproof barrier system around windows and doors.
Poly Wall® Blue Barrier™ Gap Filler2200 fills the gaps or treats pipes and penetrations before applying Blue Barrier™ Liquid Wrap 2300 or Liquid Flashing.
Easy to apply with a roller, Poly Wall® Blue Barrier™ Flash ‘N Wrap 2400 is a liquid window and door flashing that replaces traditional window tapes. It can also serve as a permeable air barrier for thin building envelope applications.
Poly Wall® Window and Door Sheet Flashing Products
Poly Wall® also has five unique window and door flashings: WindowSeal® Window Flashing, Butyl Flash , Aluma Flash™, Aluma Flash Plus™, and ArcFlash™.
Preserve Your Home’s Integrity with Poly Wall® Air and Moisture Barrier Systems
Code compliant air barriers prevent moisture infiltration into a wall system much more effectively than vapor barriers, which only stop moisture transported by vapor diffusion. However, some colder climate zones also require vapor barriers to prevent vapor diffusion into the wall systems during the winter months.
Protecting your home with a high-quality air barrier, from the top down to its foundation, will protect the home's integrity and air quality, along with lessening maintenance and repair bills. Applying Poly Wall® Air and Moisture Barrier Systems to your home’s above- and below-grade walls and around all windows, doors, and penetration will significantly lessen energy use and moisture-related problems.
Get in touch with Poly Wall® professionals today for more about the difference between air and vapor barriers and to find out how Poly Wall® products can help achieve your home’s design goals.