Durable, long-lasting, and healthy buildings require quality below-grade waterproofing or damp proofing, either post-applied after the concrete pour or blindside waterproofing (pre-applied) before pouring concrete. A foundation without high-quality waterproofing can allow moisture and contaminants to infiltrate the building envelope, which can cause significant structural damage, diminish the indoor air quality, and even endanger the occupants and neighborhood.
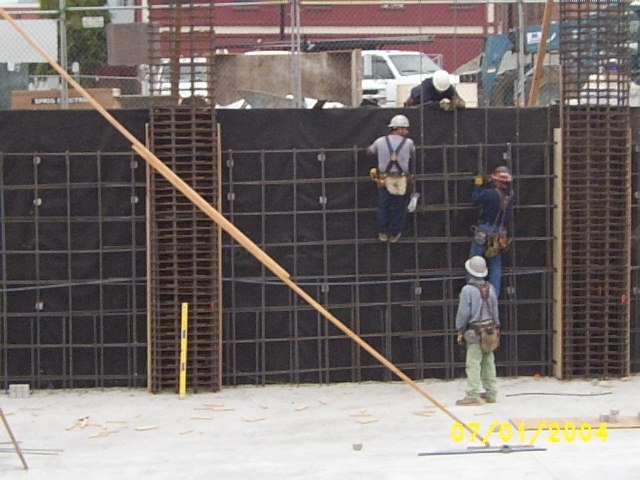
Waterproofing Vs. Damp Proofing
Waterproofing resists hydrostatic pressure, which can cause liquid water to infiltrate a wall system. It can also stop contaminants from migrating through the concrete. Damp proofing only prevents soil moisture from coming through the wall and does not protect against water under pressure.
- Buildings constructed wholly or partially below the water table, or on a hillside and in areas with significant rain and a high water table require waterproofing.
- Buildings in dry locations can utilize damp proofing on their foundations.
Fortunately, Poly Wall Building Solutions (a division of Polyguard) makes high-quality foundation post-applied and blindside waterproofing and damp proofing products. Our products protect against air and moisture infiltrations and significantly contribute to a building’s long-term integrity and indoor air quality.
How Water Infiltrates Foundation Walls
Water has many opportunities to infiltrate below-grade walls, making waterproofing below-grade walls vital to the long-term integrity of a building and the health of its occupants, including its foundation:
- Poor site drainages
- Wall penetrations
- Door/vent/window openings
- Concrete cracking/mortar joints and movement
- Flooding
- High water tables
- Hydrostatic pressures
All these situations contribute to foundation leaks which can cause costly and complicated repairs. Excess moisture will raise the relative humidity within the building and increase the potential for condensation and damaging and unhealthy mold.
Waterproofing new foundation walls can limit, if not stop, foundation water intrusion.
Builders typically apply below-grade waterproofing after pouring the foundation walls (post-applied waterproofing). However, some projects require blindside (pre-applied waterproofing) waterproofing due to access limitations or issues with excavation.
What Is Blindside Waterproofing?
Blindside waterproofing involves installing a drainage course and waterproofing membrane before constructing the vertical concrete walls. The blindside waterproofing goes on the outside of the foundation wall (positive-side). Consequently, the concrete foundation wall will add strength to the waterproof membrane when groundwater or contaminant vapors apply pressure.
The challenging process of applying blindside waterproofing involves installing over soil retention systems made of lagging beams, sheet pilings, or compacted soil.
Benefits of Blindside Waterproofing
Blindside waterproofing offers developers and builders several advantages. Densely populated areas where property lines or nearby structures limit access and excavation commonly use blindside waterproofing allows building developers to maximize land use while protecting the structure from extreme water damage or vapor intrusion. Tunnels and subways also commonly use blindside waterproofing.
Blindside waterproofing lessens excavation (removal of soil around the building perimeter), which can potentially benefit towards LEED credits by minimizing site disturbance.
Applying Blindside Waterproofing
Builders install blindside waterproofing, like Polyguard Blindside Membrane, before the foundation wall. First, they apply it to the soil support (i.e., rocks, shoring, sheet pile, slurry wall, neighboring building). Next, they apply concrete or shotcrete against the membrane, which permits the waterproofing membrane to adhere to the concrete foundation.
Polyguard Blindside Membrane
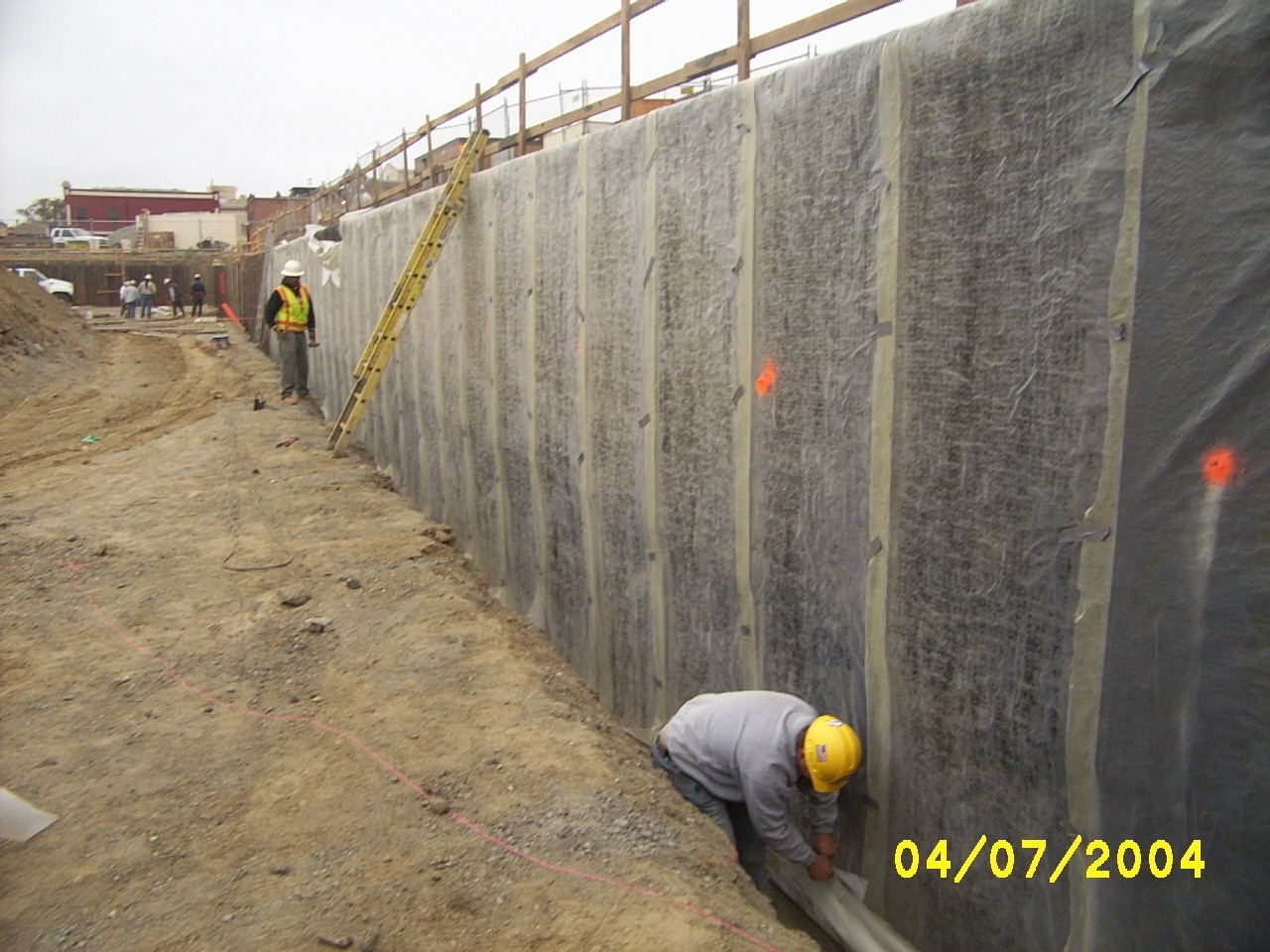
Puncture-resistant, flexible, 73 mil Blindside Membrane waterproofing membrane is vertically installed before workers pour the concrete foundation wall. The concrete cures after pouring to form a mechanical bond with the membrane. In addition, the cold flow tendencies of the membrane produce an outside adhesive layer, which creates a tight seal and high-quality protection against moisture infiltration.
You can install the Blindside Membrane horizontally over prepared sub-base like carton forms, mud slab, fine crushed beds/pea gravel, or Polyguard approved drainboard.
Advantages of Blindside Membrane
- Puncture-resistance of more than 217 lbs., 64 times greater than the requirements for a Class A Vapor Barrier. A strong puncture resistance protects the system from abuse during construction (foot traffic, trucks, regular vibrations, etc.).
- When pouring, the fibers of the nonwoven geotextile form a solid mechanical bond when the concrete.
- Once installed, freeze/thaw, rainfall, and wet/dry cycling do not affect the waterproofing system.
- It may qualify for L.E.E.D. Certification thru several credits:
- IAQ Credit 5 -Indoor Chemical and Pollutant Source Control (below-grade toxin barrier) o
- S.S. Credit 3 -Brownfield redevelopment
- ID Credit 1 -Innovation in design
- Flexible enough to adapt to jobsite irregularities.
- Provides fully adhering watertight laps for ease of installation.
Why Select Polyguard Blindside Membrane?
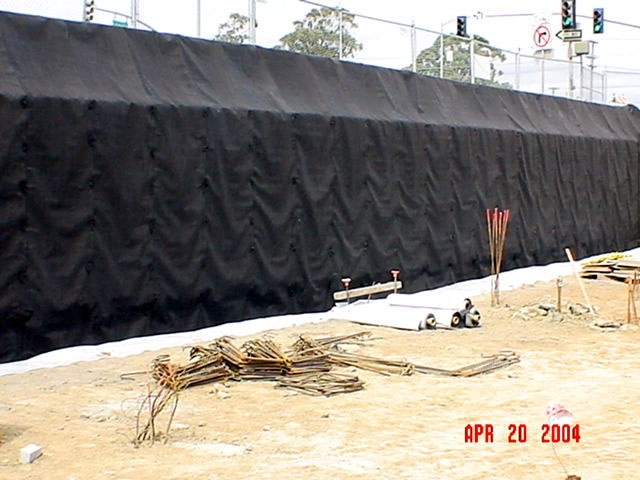
Durable, long-lasting, and healthy buildings require quality damp proofing or below-grade waterproofing, either post-applied after the concrete pour or blindside waterproofing (pre-applied). Blindside waterproofing installs on soil support before pouring the concrete. Crowded areas with limited access and the ability to excavate typically require blindside waterproofing.
Strong, durable, and sustainable Blindside Membrane offers a superior solution to blindside waterproofing. It virtually eliminates water and vapor transmission through concrete slabs on grade.
Don’t hesitate to contact the Polyguard professionals today to learn more about blindside waterproofing.