Concrete foundation flashings direct water down and away from a building and contribute significantly to a below-grade wall waterproofing system, an essential component of a durable, strong, and safe building. The flashing performance depends on the proper selection of materials, detailing, and installation.
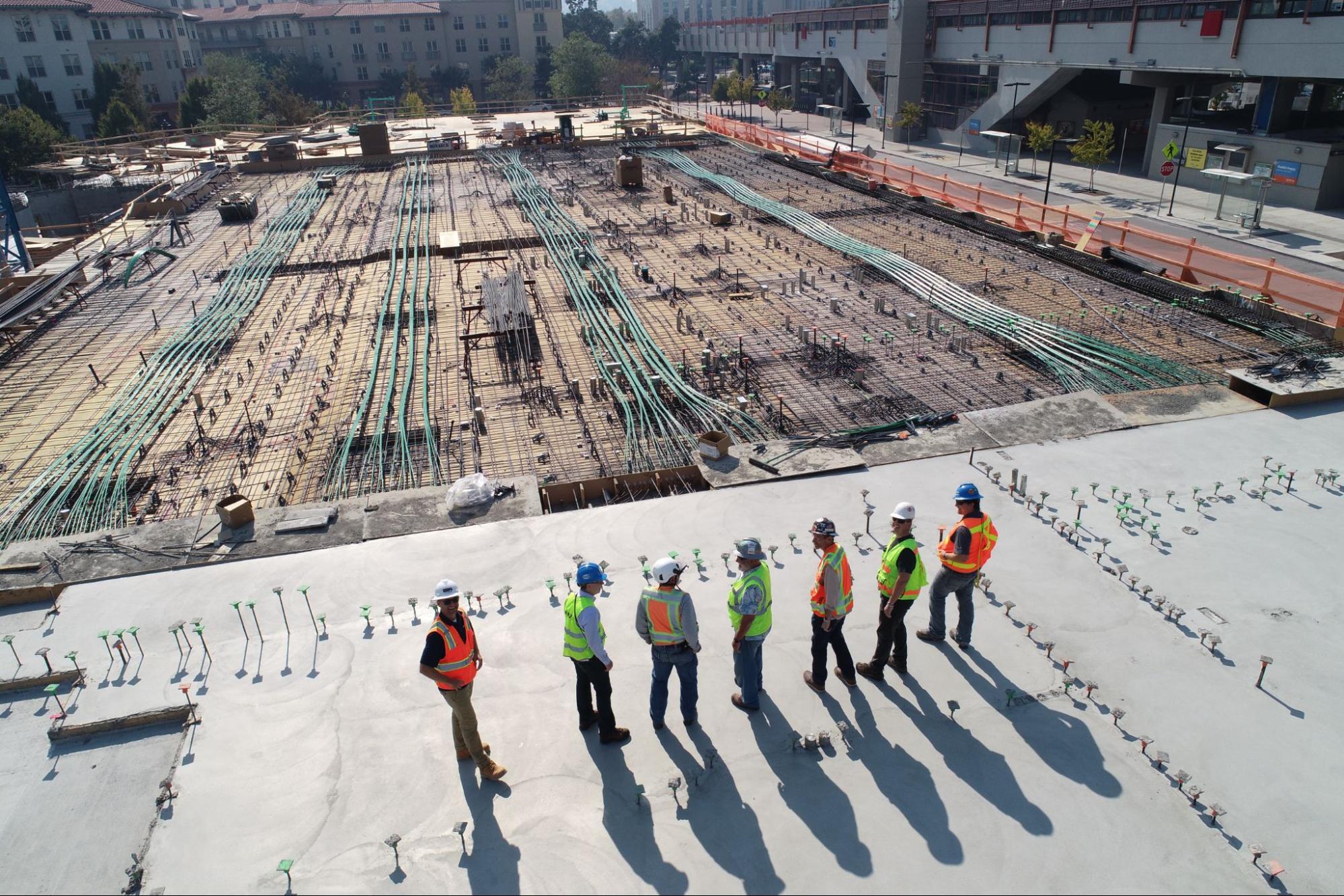
The below-grade wall performance depends on the appropriate design and installation of all individual elements of the waterproofing system, including the flashings, vapor retarders, air barriers, and insulation. Of concern, water intrusion accounts for 70 percent of construction litigation. Builders can limit these problems by sufficiently waterproofing new basement walls.
Fortunately, Polyguard offers superior concrete foundation flashings and other waterproofing products to protect against moisture and air infiltrations, to help ensure a building's long-term integrity, safety, and health.
Why Waterproof a Concrete Foundation?
Properly waterproofing a foundation will protect a structure's integrity and indoor environmental quality by:
Stopping water infiltration into the below-grade wall and protecting it against structurally damaging and unhealthy mold, mildew, and rot
Preventing liquid water from infiltrating a building's interior, which can cause considerable damage to its contents
Minimizing water in the masonry, which may freeze, leading to cracking and spalling of the masonry units or mortar
Limiting water vapor from condensing inside the masonry's cores and surface
What Are Concrete Foundation Flashings?
Builders install foundation flashing at the base (bottom) and behind the concrete wall panel to direct water away from the building. Like all components of the waterproofing system, the flashing design must consider the impacts of wind pressure, hydrostatic pressure (gravity), and capillary action (moisture absorption).
Forceful wind pressure on the surface of an exposed wall can drive exterior moisture into the masonry.
Hydrostatic pressure occurs when gravity pushes stagnant-dense water against concrete foundation walls built entirely or partially below the water table or on a hillside. Hydrostatic pressure increases with depth and soil wetness and causes moisture to flow through joints and cracks, and infiltrate concrete foundations through capillary action (wicking), which can lead to larger pores, gaps, and voids in the concrete and corroded rebar, and will diminish the compressive strength of the concrete.
Capillary action occurs when water travels into narrow channels between porous concrete due to cohesive and adhesive forces interacting between the surface and liquid without gravity.
Foundation Flashing Types
Standard foundation flashings include flexible peel-and-stick tapes, liquid flashings, or rigid flashings. Environmental and design/building considerations determine the best type of flashing for a foundation.
Environmental considerations include moisture present (liquid, solid, or vapor), air movement, temperature extremes, and temperature differentials.
Design/build considerations include choosing the flashing material, location, and structural and installation details.
Foundation Flashing Material
Plastics and Rubber Compound Flashings
Plastic and rubber compound flashings come in EPDM (ethylene propylene diene terpolymer), PVC (polyvinyl chloride or vinyl), and rubberized asphalt.
Pros
Flexible - easy to form and join
Non-staining
Fully adhered
Does not require a separate lap adhesive
Self-healing
Low-cost
Cons
Requires full support
Degrades in UV light
Requires a drip edge
Easily damaged, poor durability
The right flashing material (sheet metals, composites, or plastic and rubber compounds) for a particular application depends on the service conditions, cost, durability, compatibility with other materials, ease of installation, aesthetic value, and performance.
The flashing should effectively perform for the building' lifespan to avoid the labor-intensive and costly repair or replacement of flashings.
Composite Flashings
Composite flashings come in lead-coated copper and copper laminates.
Pros
Flexible - easy to form and join
Durable
Non-staining
Cons
Difficult to solder
Requires a metal drip edge
Degrades in UV light
Tears easier than metal flashings
Excessive flexing will damage composite flashings
Sheet Metal Flashings
Sheet metal flashings come in stainless steel, cold-rolled copper, and galvanized steel.
Pros
Durable
Non-staining
Flexible - easy to form and join
Easy to paint
Cons
Difficult to solder and form
May stain surfaces
Corrodes in acidic and salty air
Damaged by excessive flexing
Plastics and Rubber Compound Flashings
Plastic and rubber compound flashings come in EPDM (ethylene propylene diene terpolymer), PVC (polyvinyl chloride or vinyl), and rubberized asphalt.
Pros
Flexible - easy to form and join
Non-staining
Fully adhered
It does not require a separate lap adhesive
Self-healing
Low-cost
Cons
Requires full support
Degrades in UV light
Requires a drip edge
Easily damaged, poor durability
Polyguard Concrete Foundation Flashings
Polyguard foundation waterproofing products (sheet and fluid applied and drainage systems) protect against liquid and vapor water infiltration into the concrete foundation by hydrostatic pressures and capillary action. In addition, Polyguard offers several high-quality flashing products to help ensure a water-tight foundation, including Polyguard 105 Flashing Membrane and TERM® Flashing Moisture|Termite Barrier.
Polyguard 105 Flashing Membranes
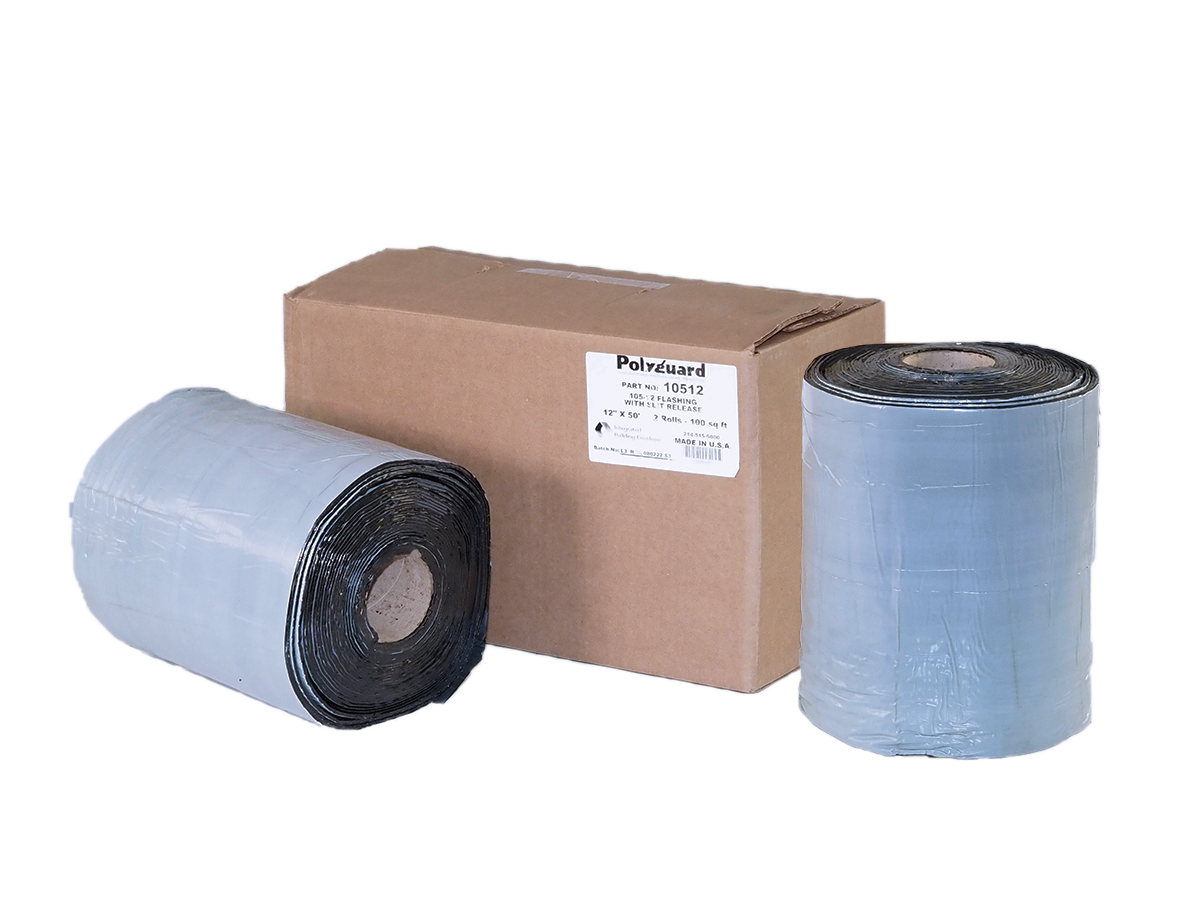
Builders can use Polyguard 105 exterior flashing membranes to divert water along sills, spandrel beams, copings, window and door headers, and flanges. Polyguard manufactures 105 Flashing Membranes in 12-inch and 18-inch, 50-foot rolls.
Polyguard 105 mil flashing provides:
Strong, flexible, self-adhesive sheet
A high-density polyethylene (HDPE) film bonded to a layer of rubberized asphalt waterproofing compound with a slit release sheet to conform to 90-degree angles
High puncture resistance that stands up to abuse by other trades during and after installation
Rubberized asphalt membrane securely clings to the surface, to eliminate blow-offs and tears before and after exterior wall installation
Rubberized asphalt helps to self-seal a punctured membrane
Accommodates most job site conditions without cracking, unlike some metal systems
Once installed and protected from ultraviolet light, the membrane will not rot or decay from mildew, mold, or plasticizer migration
Applying Polyguard 105 Flashing Membrane
Before applying Polyguard 105 Flashing Membranes, clean all dirt, dust, and foreign surfaces and eliminate sharp protrusions.
Prime the dry surfaces with 650 LT Liquid Adhesive at an average rate of 250-300 ft2./gallon by roller or brush.
After the adhesive becomes tacky to the touch (30 to 60 minutes), apply the 105 Flashing Membranes to areas requiring flashing to direct water away from walls.
Extend the vertical termination on the substrate 6 inches for extra protection and seal on the installation day with Detail Sealant PW™.
Last, overlap all the flashings at least 2 inches, and run them parallel to the direction of water flow. For temperatures below 40º F (4º C), prime the overlaps.
TERM® Flashing Moisture|Termite Barrier
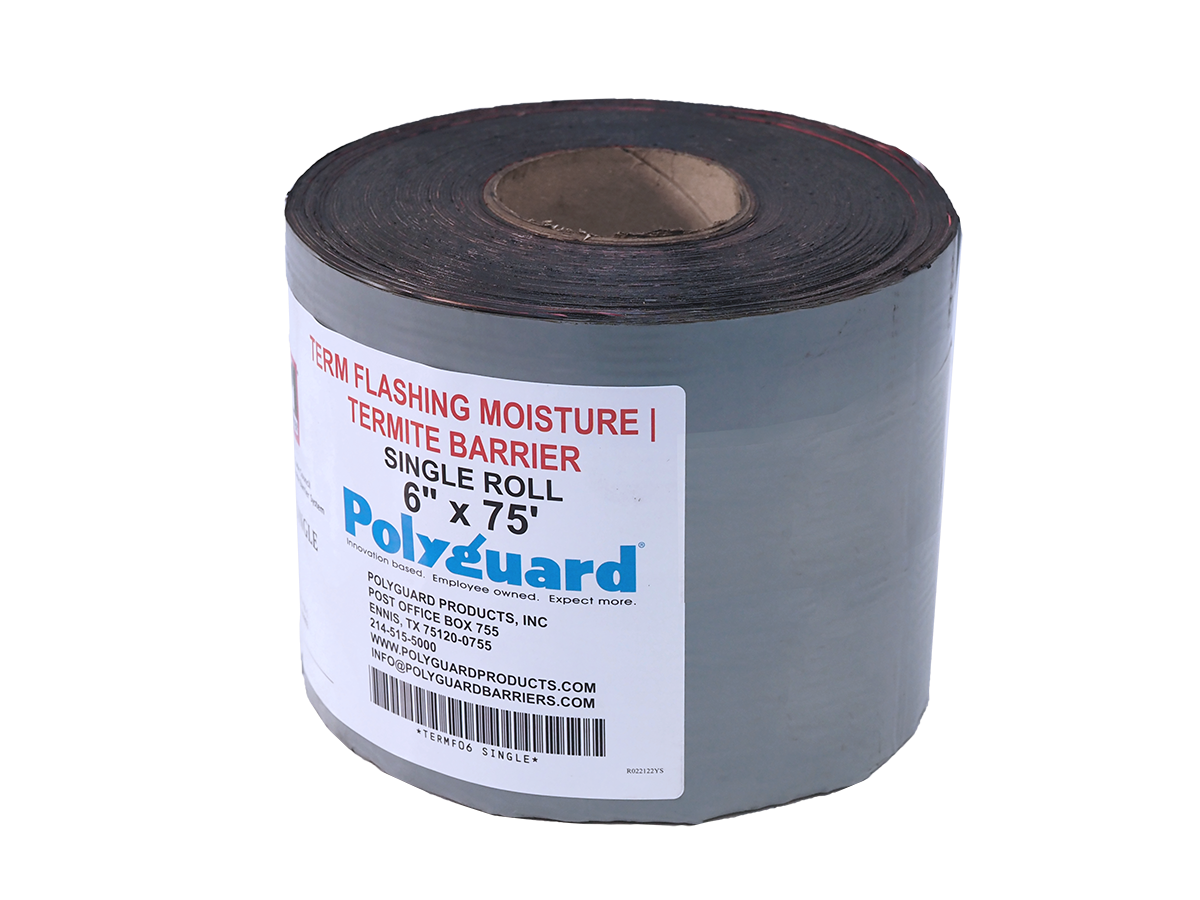
Polyguard TERM® Flashing Moisture|Termite Barrier, part of the Polyguard TERM® Barrier Systems Division non-chemical termite barrier system, provides waterproofing, energy sealing, and insect resistance. Builders can apply TERM® Flashing | Termite Barrier, where the horizontal concrete slab intersects with exterior sheathing, a common termite entry point.
TERM® Flashing | Termite Barrier provides the following features:
UV protection for one year
A flexible membrane that keeps air, moisture, and pests excluded when properly installed as part of the building envelope
A strong, pliable, self-adhesive sheet flashing with special silver foil facing
40-mils thick: 4-mil high-density polyethylene film bonded to 36 mils of sealant
Formulated for low-temperature application down to 30°F (-1°C)
For flashing applications, Polyguard has TERM® Flashing | Termite Barrier in 12-inch and 18-inch, 75-feet long rolls
NFPA 285 rated
The only physical termite barrier with 20+ years of testing and an evaluation report by the ICC (International Code Council) AC 380 ESR 3632
Applying the TERM® Flashing | Termite Barrier
Temperature Restrictions: Apply TERM® Flashing | Termite Barrier in temperatures above 30°F (-1°C) and rising. Cold and damp conditions marginalize the initial adhesion; however, 650 LT Liquid Adhesive will assist the initial adhesion.
Before applying TERM® Flashing | Termite Barrier, clean all dirt, dust, and foreign surfaces and eliminate sharp protrusions. The adhesive surface of the tape should not touch caulks or sealants (including most silicone or polyurethane) that contain plasticizers or solvents.
Prime the dry surfaces with 650 LT Liquid Adhesive at an average rate of 250-350 ft2./gallon by roller or brush. Apply liquid adhesive to all surfaces which will receive TERM® Flashing | Termite Barrier.
Cut pieces of flashing to length as needed and apply to the substrate 30 - 60 minutes after applying liquid adhesive.
Place the flashing with its horizontal portion extending no closer than ½-inch from the edge of the horizontal ledge.
Remove the first 6-12 inches of the release liner and adhere the exposed adhesive face to the substrate.
Overlap the adjacent flashing pieces by a minimum of 2 inches. Shingle the pieces vertically so the piece closest to the exterior (lower piece) overlaps the other piece.
Extend the flashing past the TERM® Sill Barrier edge to ensure tie-in.
Roll the flashing securely into place with a hand roller.
Use 650 Mastic to seal all top horizontal terminating edges on pipes, walls, and other protrusions.
Polyguard Makes the Best Concrete Foundation Flashings
Strong, flexible, self-adhesive sheet Polyguard concrete foundation flashings (105 Flashing Membrane and TERM® Flashing Moisture|Termite Barrier) efficiently direct water down and away from a building to a below-grade wall waterproofing system, which is vital to maintaining a building's integrity and health.
Contact the Polyguard professionals today for more on the significance of effective concrete foundation flashings!