Properly installing vapor barriers (retarders) according to vapor barrier code requirements will minimize or stop water vapor infiltration and exfiltration into a building envelope, provide damp proofing, and enhance the building's comfort, energy efficiency, and long-term integrity. Vapor barriers can also limit condensation within the walls, floor, foundation, and roof, which can cause structurally damaging and unhealthy mold and threaten the insulation's effectiveness.
Note: Buildings susceptible to contact with water typically require a vapor-resistant barrier. Polyguard suggests you contact your local building inspection office for guidance on building code vapor barrier requirements.
Is a Vapor Barrier Required by Code?
The vapor barrier requirements by code depend on the climate zone and the building's construction.
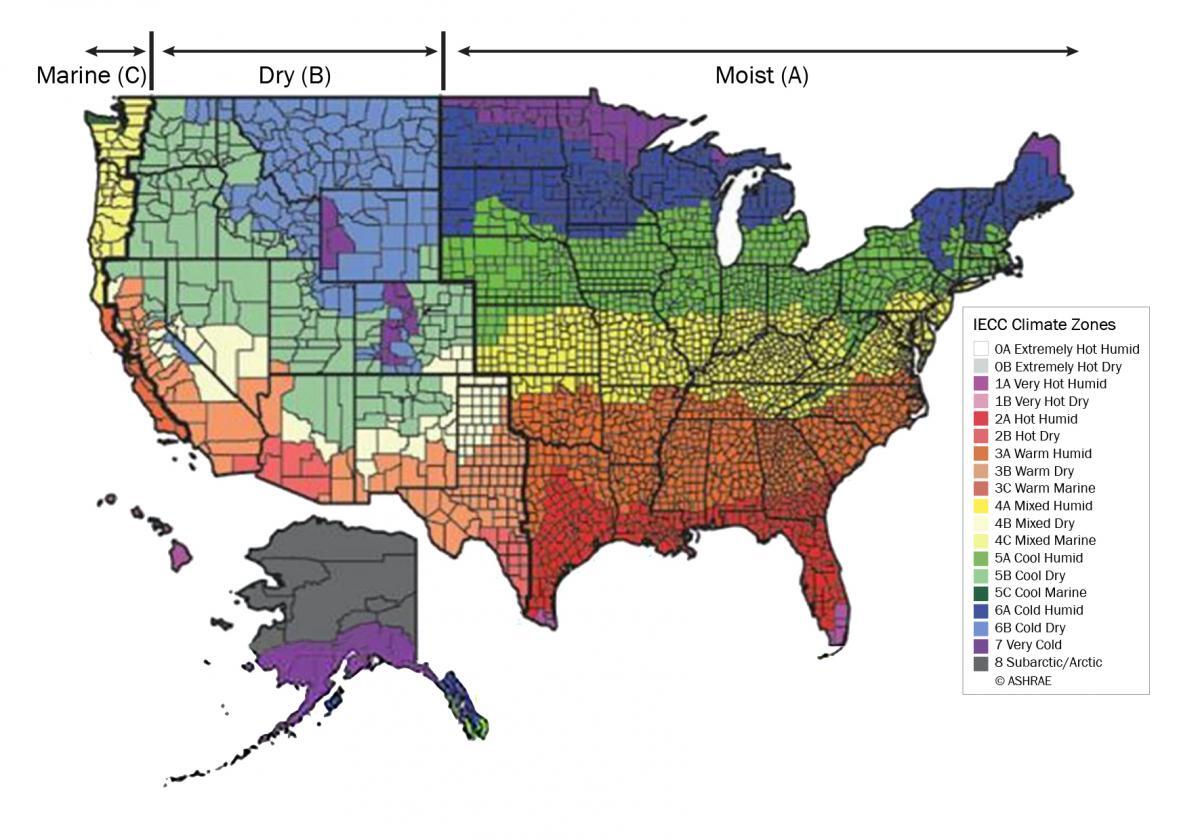
The 2021 International Residential Code R702.7 and the 2021 International Building Code 1404.3 mandate using Class I or II vapor retarders inside framed walls in climate zones 5, 6, 7, 8, and Marine 4. Southern, warmer climate zones (1, 2, and 3) do not need vapor barriers and retarders.
Installing a vapor barrier in or around walls, ceilings, and floors prevents moisture from passing through, and is measured by its moisture vapor transmission rate (permeability).
A vapor diffusion retarder refers to permeable barriers.
Vapor Retarder Classes
The IRC describes three classes of vapor retarders according to their permeability:
Class I vapor retarders or barriers (0.1 perms or less): sheet metal, glass, polyethylene sheet, and rubber membranes.
Class II vapor retarders (more than 0.1 perms and equal to or less than 1.0 perms): extruded polystyrene or unfaced expanded, 30-pound asphalt-coated paper, bitumen-coated kraft paper, and plywood.
Class III vapor retarders (more than 1.0 perms and equal to or less than ten perms): concrete block, gypsum board, fiberglass insulation (unfaced), cellulose insulation, board lumber, brick, 15-pound asphalt coated paper, and house wrap.
The Best Vapor Barriers for Foundations, Walls, and Roofs
When properly applied, the best vapor barriers for foundations, walls, and roofs will provide long-term adhesion, durability, and performance. Fortunately, Polyguard offers several easy-to-install and durable peel-and-stick vapor barriers and companion products for foundations, walls, and roofs. Our products guarantee a high-performing, long-lasting vapor barrier for your building when properly installed.
Polyguard® Home Stretch Foundation Vapor Barrier Membrane
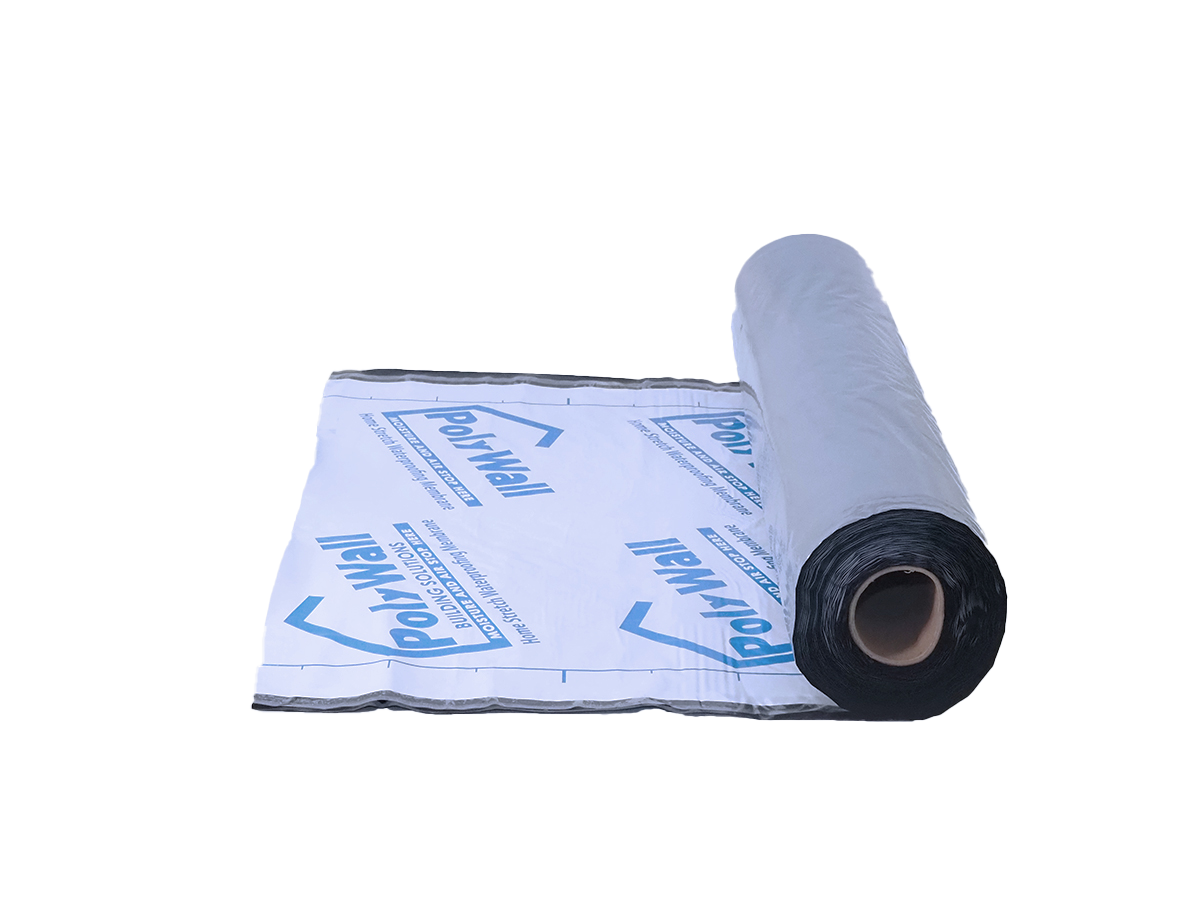
Polyguard® designed and engineered WM40 waterproofing membrane for expanded and extruded polystyrene insulated concrete forms (ICF), poured concrete foundation walls, concrete masonry units walls, and related waterproofing applications in the presence of hydrostatic pressure.
Robust, flexible, self-adhering WM40 is a 40 mil thick sheet waterproofing membrane consisting of high-density polyethylene (HDPE) facing bonded to a rubberized asphalt waterproofing compound. Home Stretch comes in 36-inch wide by 66.7-foot long rolls for easy handling and installation, with a disposable treat release liner.
Polyguard UV2-40 Wall Peel and Stick Vapor Barriers
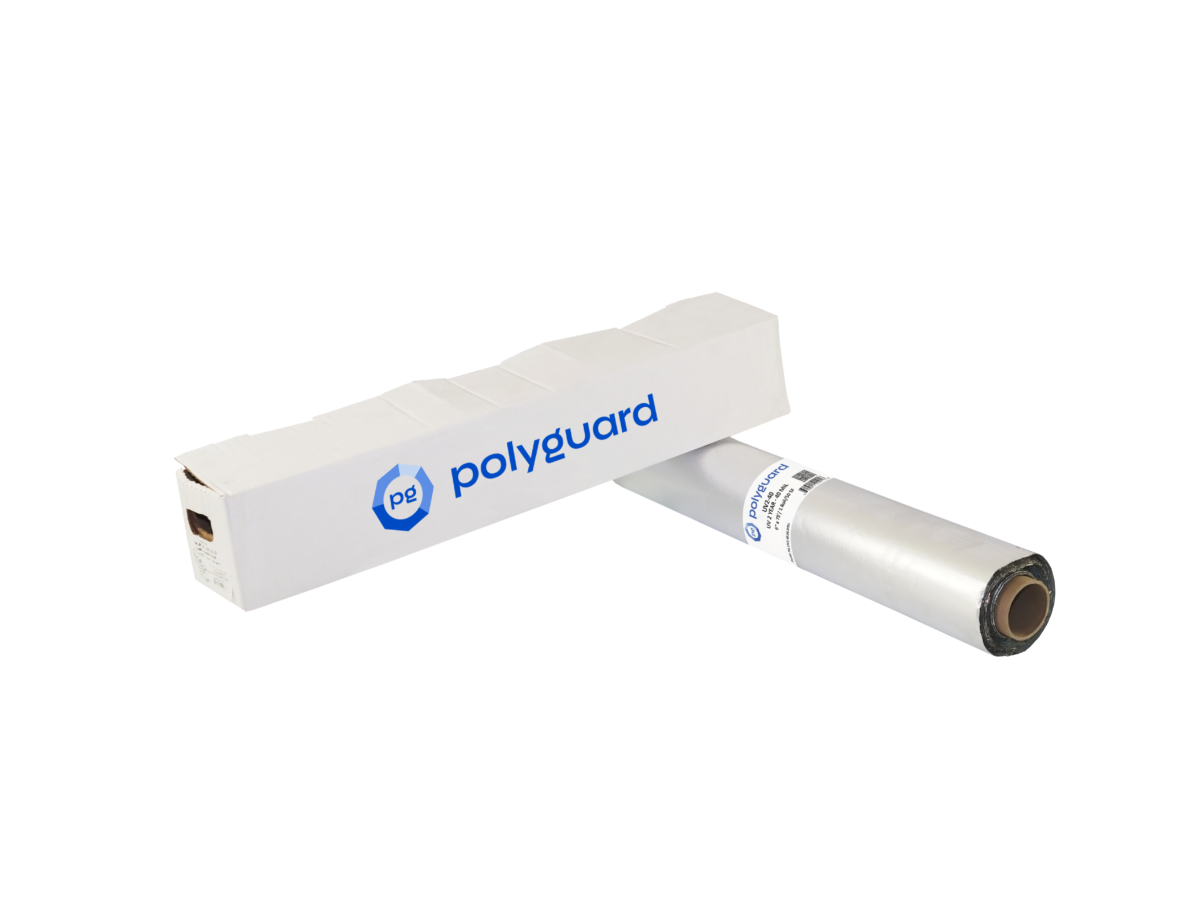
Builders can use Polyguard UV2-40 (formerly AlumaFlash Plus) in higher-exposure buildings for a more robust waterproofing strategy. The protective layer of aluminum provides an ultraviolet resistance exposure time of two years.
Fast and straightforward to apply, sunlight- and chemical-resistant Polyguard UV2-40 adheres when used according to the manufacturer's installation and performance requirements. Polyguard UV2-40 is a 40-mil rubberized asphalt waterproofing membrane, laminated to two layers of high-strength polyethylene film, with a top protective layer of aluminum — to ensure a robust waterproofing product. In addition, the aluminum surface of durable Polyguard UV2-40 works well with higher exposure buildings because it reflects heat, to lessen energy costs.
Is a Vapor Barrier Required by Code in Crawl Space?
Crawl space vapor barrier code requirements aim to protect the crawl space from ground moisture infiltration - which is particularly vital in high-humidity regions. The 2021 International Residential Code (R408.3) mandates covering exposed earth with a continuous Class 1 vapor barrier for unvented under-floor space. Additionally, the vapor barrier must overlap joints by 6 inches (152 mm) before sealing and taping. Extend the vapor barrier's edges at least 6 inches (152 mm) up the stem wall, then attach and seal to the insulation or wall.
The Best Vapor Barrier for a Crawl Space
The best way to prevent groundwater from entering a crawl space and ultimately damaging a home or building involves installing a puncture-resistant, low-permeance Class 1 vapor barrier, like Polyguard's Underslab TRM.
Fully-adhered Underslab TRM is the industry's thickest vapor barrier for crawl spaces. It creates a durable physical barrier against water and termites.
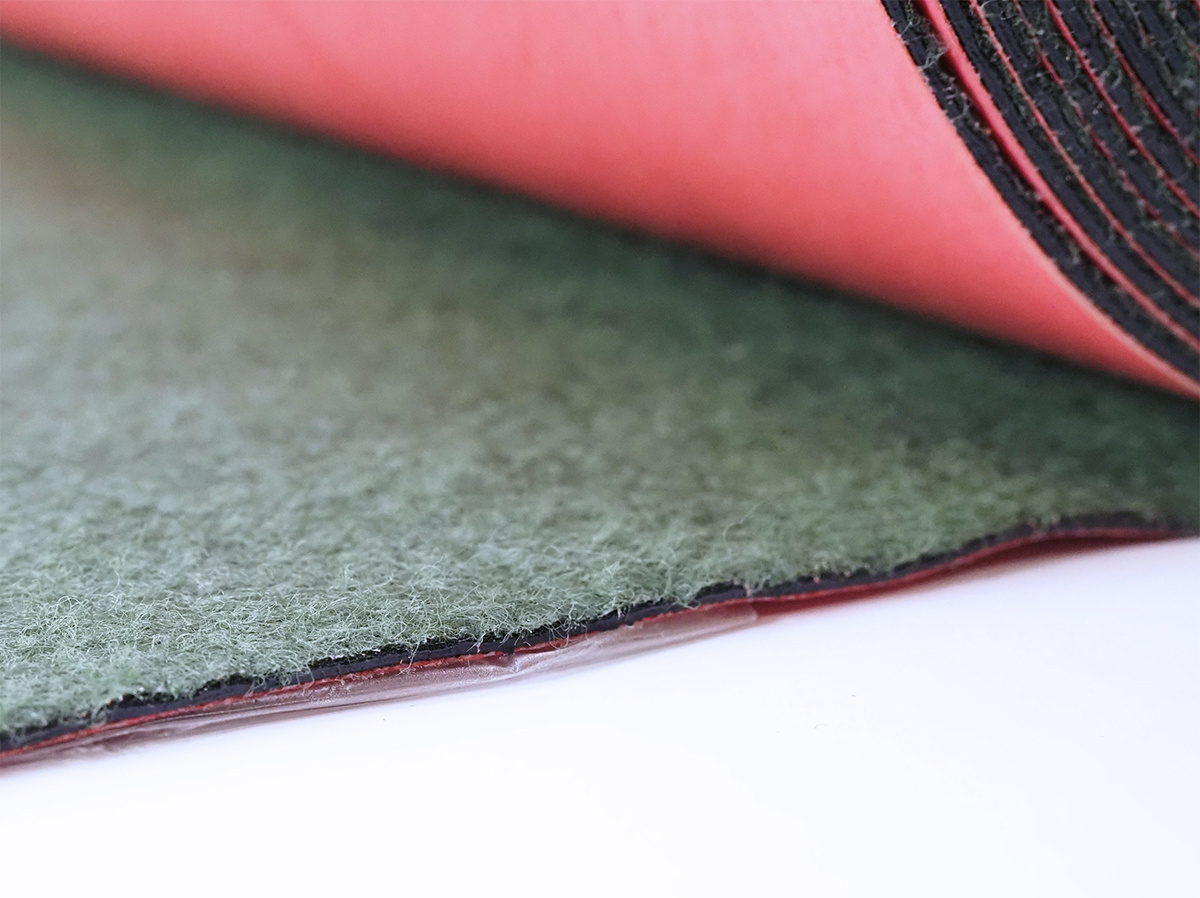
The high-strength Underslab TRM stands up to abusive job sites. It consists of an 8.5 mils polyethylene backing laminated to a 69-mil thick TRM Sealant integrated into a high strength non-woven geotextile fabric top layer for a factory-controlled thickness of 95 mils.
Is a Vapor Barrier Required by Code?
Installing vapor barriers can help to minimize or stop water vapor infiltration and exfiltration into a building envelope, provide damp proofing, and enhance the building's durability, comfort, and energy efficiency. However, the code requirements for applying a vapor barrier depend on the climate zone and the building's construction. Generally, colder climates require vapor barriers, while warmer climates may not. In addition, crawl spaces typically require a vapor barrier. Always consult your local building inspection office for guidance on building code vapor barrier requirements.
Contact Polyguard vapor barrier professionals today for more about the need and benefits of applying a vapor barrier.