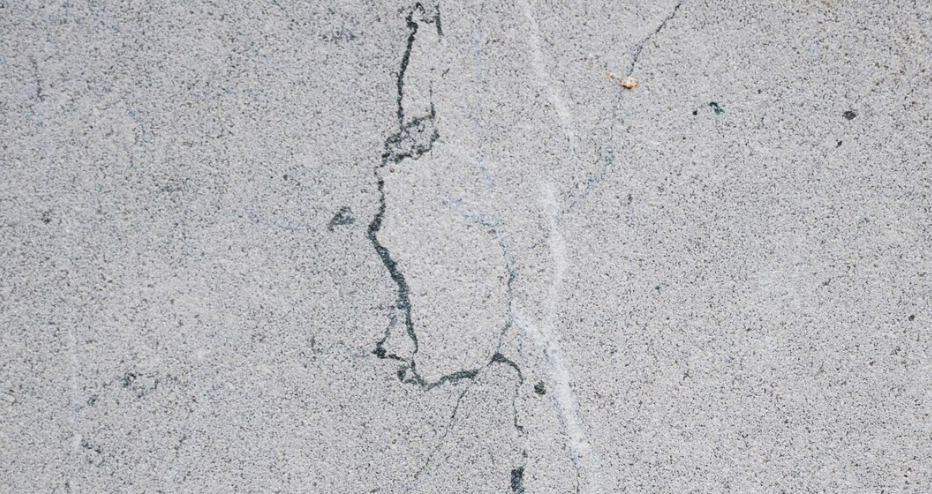
Patching concrete is crucial for the durability and safety of our infrastructure. Concrete surfaces endure a lot, from heavy traffic on highways to daily use in residential areas. Over time, cracks and weathering occur that require effective repair methods. Whether it's a busy freeway or a home driveway, choosing the right materials and techniques is important.
The Basics of Concrete Patching
Concrete patching does not just prolong the lifespan of concrete surfaces; it also preserves structural integrity. Whether for high-traffic highways or residential driveways, the choice of patching materials and techniques plays a pivotal role in the maintenance process.
Types of Concrete Damage
- Hairline Cracks: Small, thin cracks that may not threaten structural integrity but can lead to larger issues if water seeps in
- Deep Cracks: Larger cracks that penetrate the concrete and require more extensive repair to prevent further damage
- Surface Wear: General wear on concrete surfaces, including potholes and eroded areas that are especially prevalent in areas with heavy traffic
Polyguard Products: Enhancing Every Road
650 RC Liquid Adhesive
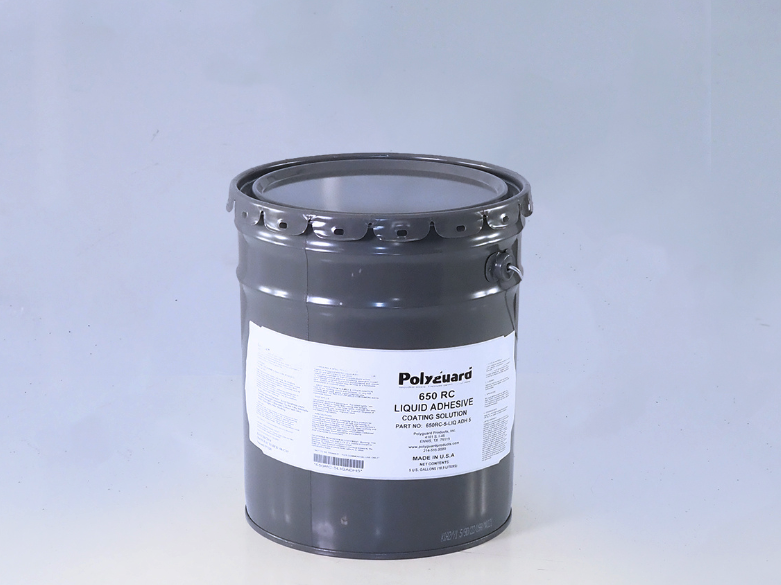
650 RC Liquid Adhesive is essential for priming surfaces to ensure optimal bonding for the sealing membrane.
665 Membrane
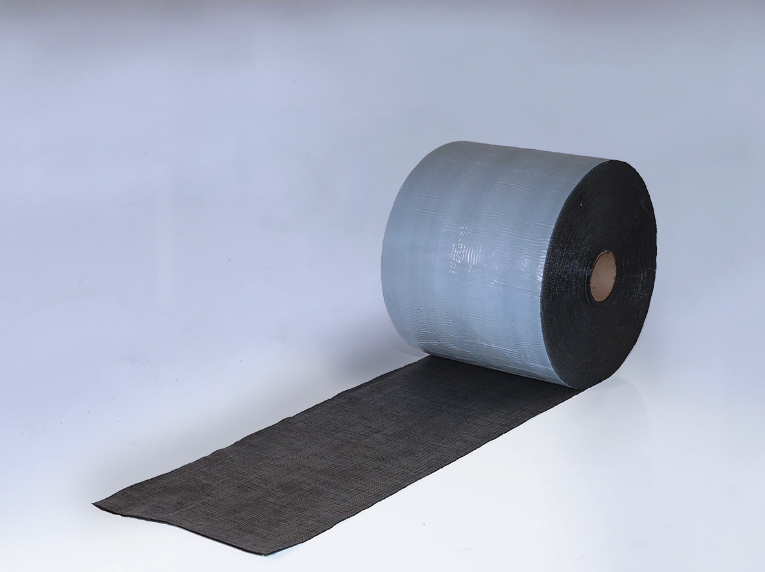
The 665 Membrane provides superior protection to keep patched areas safe from water intrusion and physical wear
For Highways
Material Selection
Highways and bridges require materials capable of enduring heavy traffic, severe weather, and environmental stressors. Polyguard’s 665 Membrane and 650 RC Liquid Adhesive are designed to meet these challenges head-on by offering unparalleled protection against moisture, chlorides, and corrosion.
Cost Considerations
High-quality patching materials like Polyguard will ensure durable repairs to significantly reduce the frequency of maintenance and to extend infrastructure lifespan, which makes it a cost-effective choice for roadway and bridge maintenance.
For Residential Driveways
Material Selection
While durability is crucial, aesthetic appeal is also a key consideration for residential driveways. Polyguard products strike a perfect balance that ensure both longevity and visual harmony for concrete patching projects.
Cost Considerations
Quality remains paramount in residential applications, with a focus on using materials that offer long-term value.
How to Patch Concrete: A Quick Guide for Patching Concrete
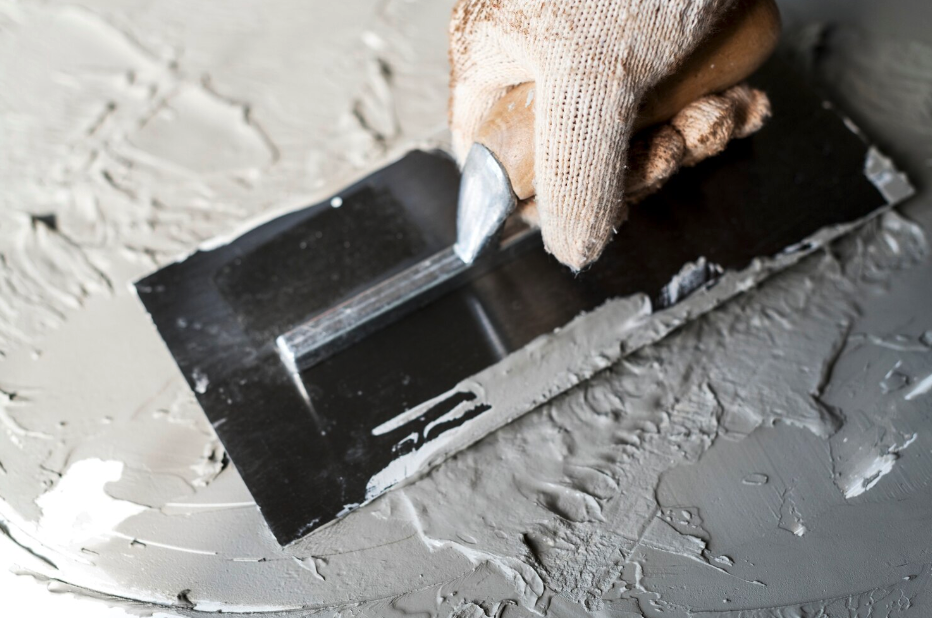
1. Debris Removal and Surface Preparation
Before patching concrete, It's crucial to start with a clean and dry surface, and preparation involves removing all voids, sharp projections, and debris. For new concrete, it must be cured for a minimum of 7 days and free from form release agents, curing agents, and other contaminants. This step will help to ensure the surface is optimal for adhesion.
2. Primer Application (Liquid Adhesive)
Polyguard 650 RC Liquid Adhesive is essential for priming concrete bridge deck surfaces or milled pavement surfaces. The need for liquid adhesive varies based on surface condition and temperature. For instance, on new asphalt surfaces, it might not be required unless the temperature is too cool to obtain a good bond, typically between 40°F and 50°F.
On old asphalt or concrete pavement, liquid adhesive is recommended if the temperature is under 70ºF. The adhesive should be allowed to cure thoroughly before membrane application to ensure that it does not stick to fingertips upon touching lightly.
3. Membrane Installation for Crack Repair
Crack repairs are very common repairs, and understanding how to patch cracks in concrete is pretty simple. For cracks and joints, the adhesive should be applied 1" wider than the membrane, which should be centered over the joint or crack with a 2" tolerance. It’s important to seal transverse joints and cracks first by extending 4" to 6" beyond each pavement edge.
Overlapping of at least 3" is required for both transverse and longitudinal membranes to ensure that the membrane is installed straight and wrinkle-free for optimal adhesion.
4. Sealing with Membrane
After applying the adhesive, cover the area with Polyguard 665 Membrane. It seals the crack or damaged area to prevent water penetration and to protect against further physical wear.
5. Inspection and Traffic Management
After application, inspect the membrane for tears, punctures, and air blisters before asphalt overlay. If traffic needs to pass over the area before overlay, it's crucial to monitor the membrane’s condition, especially in wet conditions or when exposed to UV rays for extended periods.
Preventive Measures and Maintenance
Beyond patching concrete cracks, regular maintenance and preventive measures are key to extending the lifespan of concrete surfaces. This includes regular cleaning, sealing to prevent water penetration, and inspections to catch and address damage early.
FAQs and Troubleshooting Tips
Q: How often should concrete surfaces be inspected for damage?
A: At least annually, or seasonally in areas with harsh weather conditions.
Q: Can Polyguard products be used for DIY projects?
A: Yes, Polyguard's range is designed to be user-friendly and suitable for both professionals and DIY enthusiasts.
Transform Your Concrete Surfaces Today with Polyguard Advanced Protection
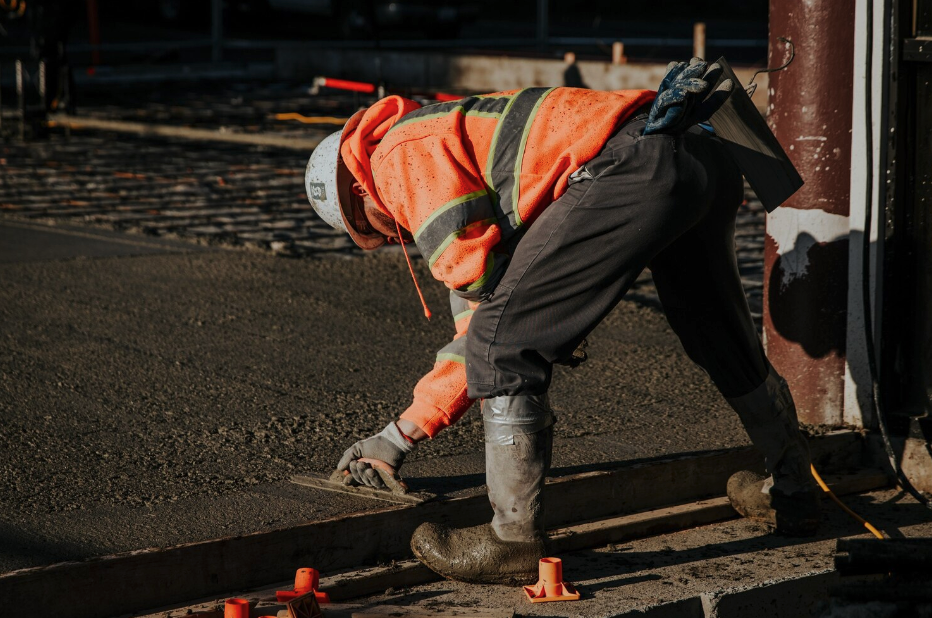
Bridging the gap between necessity and innovation, Polyguard stands as the premier choice for concrete patching. Don't let wear and tear compromise your concrete surfaces.
Contact us today for more information and take the first step towards enhanced durability and protection with Polyguard!