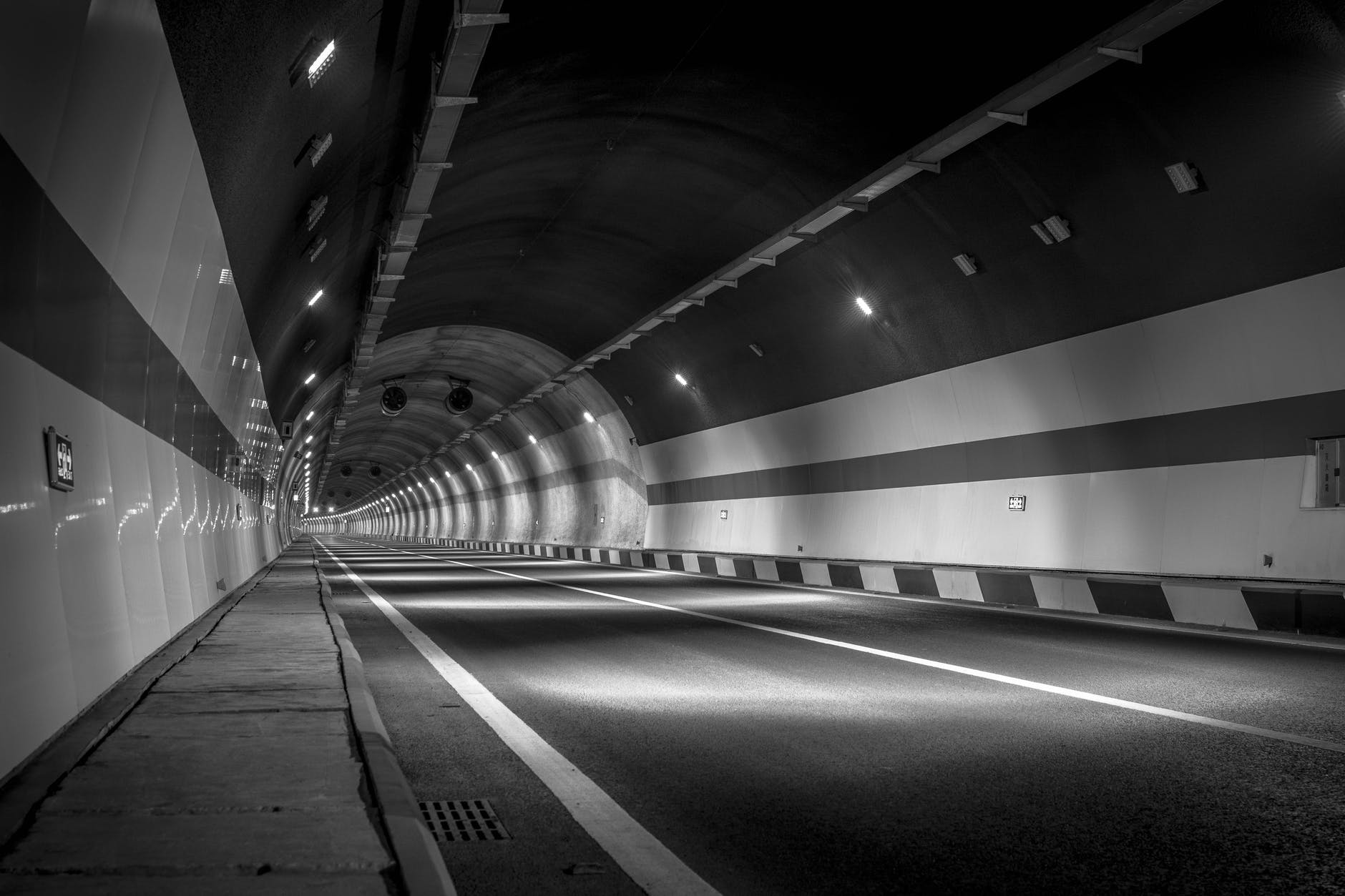
Applying a quality tunnel waterproofing membrane to a concrete project, whether a massive underground highway or just a shallow utility tunnel, will protect the tunnel’s integrity during its lifespan, limiting repairs and maintenance that can interrupt service and threaten users’ safety. Failed tunnel waterproofing methods will allow water, soils, and chemicals infiltration leading to corrosion of the steel reinforcement and long-term damage. Failed waterproofing can cause ice buildup, which is a severe safety hazard.
The choice of tunnel waterproofing membrane depends on the tunnel’s construction method, timetable, and job site conditions. However, the tunnel waterproofing method must also consider durability, sustainability, exposure, and stress conditions, along with ease of application and total cost.
The effectiveness of a tunnel’s waterproofing system depends on the proper installation and compatibility of all the components, from the substrate to the drainage system.
Read on for tips on how to successfully waterproof tunnels with Polyguard products, ensuring the integrity of the tunnel for its lifetime.
4 Tips for Waterproofing Tunnels
1. Proper Surface Preparation
The quality of the concrete surface significantly affects the waterproofing system’s performance. Only a smooth, clean concrete surface will allow the prime coat to form a mechanical bond to the surface, ensuring continuous support of the waterproofing material and good adhesion between the membrane and the substrate.
Good adhesion between the waterproofing membrane and concrete surface substrate will stop water migration and leakage in the presence of cracks or imperfections in the membrane or concrete surface. Water pressure acting on unsupported material may cause it to deform, extrude, and eventually rupture.
To ensure good bonding between the primer and substrate, you must properly prepare and clean substrate surfaces.
- Remove by mechanical or chemical processes, scales, dust, mold, oil, curing agents, or any material that can affect the bonding of the waterproofing membrane to the substrate.
- Grind surfaces down to a smooth surface, which ensures a tighter seal.
- Fill in all voids, gaps, or transition joints with Polyguard Detail Sealant PW™, an environmentally friendly, non-isocyanate adhesive/sealant. Tack-free in less than an hour, Detail Sealant PW cures in 24 hours at 75° F (24º C) and 50-percent relative humidity.
2. Prime the Substrate for Better Membrane Adhesion
Priming the concrete substrate with Polyguard® 650 LT Liquid Adhesive before applying the waterproofing member will improve the bonding between the substrate and membrane. Failure to prime will appreciably diminish the performance of the waterproofing system.
Priming structural concrete, masonry, or wood surfaces with 650 LT Liquid rubber-based adhesive will ensure superior adhesion with the Polyguard® waterproofing membranes. You can apply temperature-tolerant Polyguard® 650 LT Liquid Adhesive down to 25° F (-4° C).
3. Apply a High-Quality Waterproofing Membrane
Polyguard’s superior waterproofing membranes can stop water, contaminants, and mold from entering the structure, which helps maintain its integrity and lower maintenance and repair costs. Polyguard offers several high-performing waterproofing membranes to fit your project best: 650 Sheet Membrane, Polyguard 650L36 Sheet Membrane, and 650 PRM.
650 Sheet Membrane (48″ x 50′ rolls) and 650L36 SHEET MEMBRANE (36″ x 66.7′)
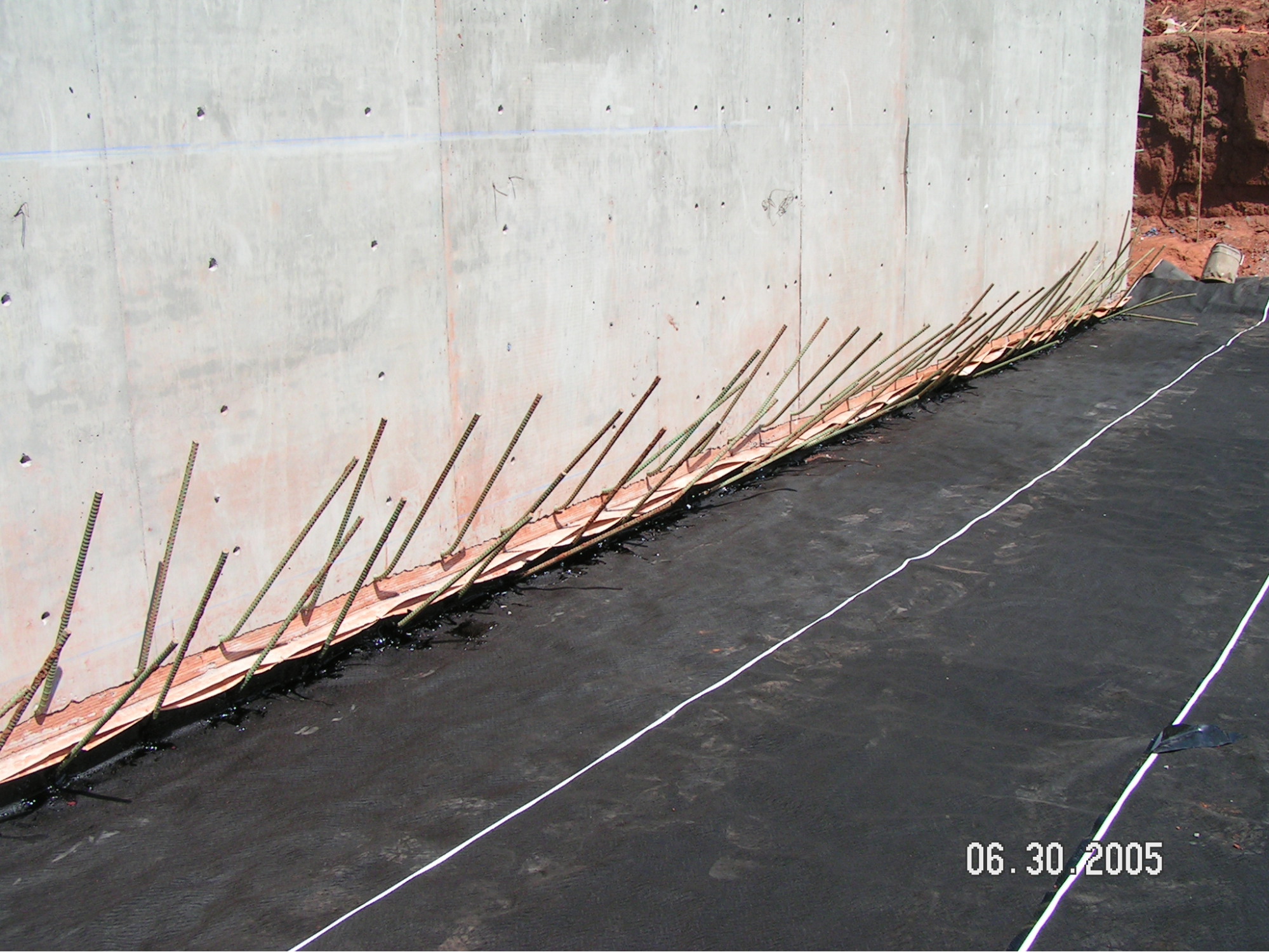
Polyguard designed the 60 mils thick 650 and 650L36 Sheet Membranes especially for use on tunnels, along with foundation walls, plaza decks, parking garages, insulated concrete forms (ICFs), and other similar applications. Applied post-concrete, poured (positive side), either vertically or horizontally, this self-adhesive waterproofing membrane/vapor retarder virtually eliminates vapor and water transmission through concrete slabs. You can utilize the 650 membranes for a Dual Core System, capitalizing on the benefits of a fluid-applied and sheet-applied membrane in a single system.
650 PRM
Polyguard’s strong, self-adhering, 65-mil 650 PRM is a post-concrete pour sheet waterproofing membrane/vapor retarder with significant strength, double-thick, cross-laminated polyethylene backing laminated to a thick layer of rubberized asphalt compound.
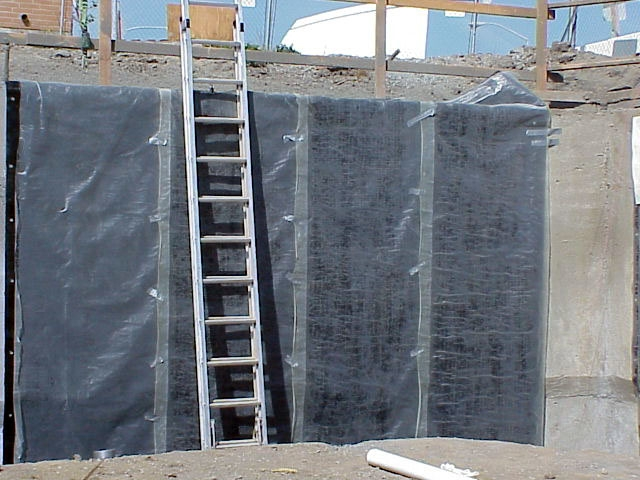
650 PRM adheres permanently and tightly to concrete, forming a continuous barrier against water and moisture infiltration. You can apply 650 PRM horizontally and vertically for a Dual Core System that capitalizes on the advantages of a fluid-applied and sheet-applied membrane in one system. It was also specially formulated for temperatures down to 25° F (-4° C).
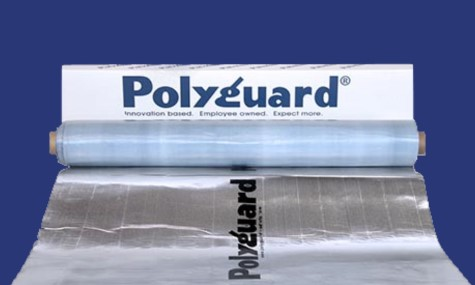
4. The Need for a Drainage System
A drainage component to a tunnel’s waterproofing system will collect and dispose of water before it damages the structure. The 15/15P Sheet Molded Drainage design establishes predetermined pathways for below-grade water management, allowing water to pass into the drain core while restricting the movement of soil particles that can clog the core. In addition, Polyflow 15/15P Sheet Molded Drainage provides a protective layer for Polyguard waterproofing membranes. However, you must limit their exposure to ultraviolet light.
Why Choose Polyguard Products for Tunnel Waterproofing?
Building a durable, long-lasting tunnel requires proper waterproofing system application, including substrate preparation, priming, waterproofing membrane, and drainage system. Fortunately, Polyguard has superior products to fit all these vital requirements.
In 2011, the Houston Country Club chose Polyguard waterproofing systems to protect the integrity of various tunnels they constructed to connect their new underground 400 vehicle parking garage (also waterproofed with Polyguard products) to their elevator room in the clubhouse. They choose our high-quality products to limit the tunnels and garages repairs and maintenance due to water inflation and protect their vehicles and members’ safety.
Contact Polyguard professionals today for more tips on waterproofing tunnels.