The U.S. has over 2.6 million miles of natural gas and petroleum pipelines—more than any other country. Designing and constructing gas and oil pipelines with coatings will help minimize the risk of damage to the pipeline’s integrity and protect the safety and health of the environment, nearby communities, and pipeline workers.
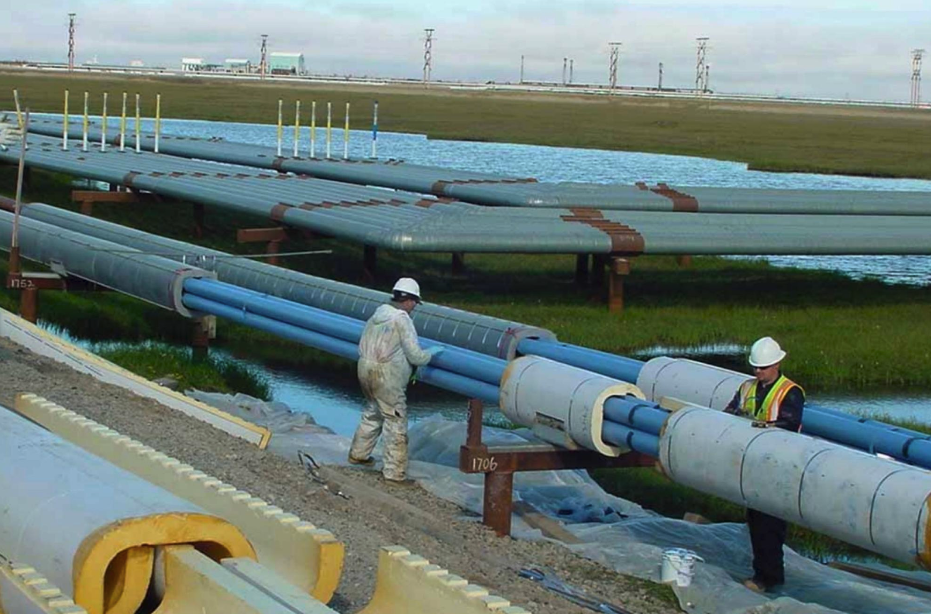
Oil and gas companies most often construct their pipelines with steel for its strength, durability, and ability to withstand the high pressure and temperature conditions in oil and gas pipelines. Properly engineered steel gas and oil pipelines are safe, efficient, and, because most are buried, largely unseen.
However, several factors can attack and degrade the pipeline’s integrity, including corrosion, which is a significant cause of pipeline damage (18.5 percent). Therefore, the design of buried steel pipes must include a quality gas pipeline coating to minimize damage due to external corrosion.
Choosing the best gas pipeline coating types depends on environmental conditions and the fluid flowing through the pipe. But there are other design considerations that protect the pipe against corrosion and equipment failure. Some of these considerations include:
- Thermal Expansion: Pipelines carrying hot fluids are prone to thermal expansion, which can cause pipe deformation and loss of its external protective coating.
- Damage: Mechanical damage to the buried pipes during soil excavation.
- Repair Challenges: The difficulty and cost of detecting and repairing buried pipes require an underground leak detection system.
- Maintenance Difficulties: There are challenges in cleaning and draining buried pipes compared to above-ground pipes.
- Code Compliant: The coating should follow federal regulations.
- Application: The design should allow for straightforward and quick application.
Fortunately, Polyguard Pipeline Coatings solves most gas and oil steel pipeline problems, such as:
- Pipeline corrosion
- Impact and chemical resistance
- Superior Adhesion
- High-abrasion resistance
- Temperature tolerance
- Federal compliance for non-shielding coatings
- Damage-resistant coating
- Slow and inefficient installation
Pipeline Coating Regulations
Requirements for corrosion protection vary based on the materials flowing through the pipeline (process oil, crude oil, dry gas, wet gas, or sour gas). Responsibility for selecting oil pipeline coating, natural gas pipeline coating, etc., that meet the necessary regulations falls on the pipeline owners and coatings contractors.
In Canada, pipelines are now regulated by provincial jurisdiction or the National Energy Board (NEB) if they cross provincial borders.
In the U.S., The Department of Transportation Pipelines and Hazardous Materials Safety Administration (PHMSA) issues minimum pipeline standards. The standards mandate that new or existing steel pipelines meet the following coating requirements (along with other design specifications) before operating at the alternative maximum allowable operating pressure (MAOP) calculated under § 192.620. In addition, you must maintain records that demonstrate compliance with requirements for the useful life of the pipeline.
Oil and Gas Pipeline Coating Requirements According to PHMSA
1. You must protect the pipe against external corrosion with a non-shielding coating.
2. Pipes used for trenchless installation must be non-shielding and withstand abrasions and other damage during installation.
3. The coatings quality assurance inspection and testing program must include the following:
- The surface quality of the bare pipe
- Surface cleanliness and chlorides
- Blast cleaning
- Application temperature control
- Adhesion
- Cathodic disbondment
- Moisture permeation
- Bending
- Coating thickness
- Holiday detection
- Repair
Non-Shielding Coatings Protect Against Pipe Corrosion
An effective non-shielding coating provides two functions:
1. Non-shielding coatings provide primary corrosion protection to gas and oil piping by resisting degradation, disbondment, or loss of adhesion. However, non-shielding coatings require a backup if the coating fails, most likely due to improper surface preparation or application techniques, soil stress, impurities, etc. In addition, coatings contain tiny openings that may allow corrosion-causing compounds, like oxygen and water, to infiltrate.
2. Cathodic protection (CP) provides the backup if the coating fails. CP allows the cathodic protection current to reach the pipeline’s disbonded areas (its intended path), to raise the pH of the water between the pipe and the disbonded coating to 9 or higher - a value that does not support corrosion.
Polyguard Oil and Gas Pipeline Coatings
Polyguard Pipeline Coating products for gas and oil pipelines will protect the pipelines' integrity by minimizing corrosion and providing impact, chemical, temperature, and ultraviolet (UV) resistance, strong adhesion, and straightforward application.
Polyguard RD-6® Coating System
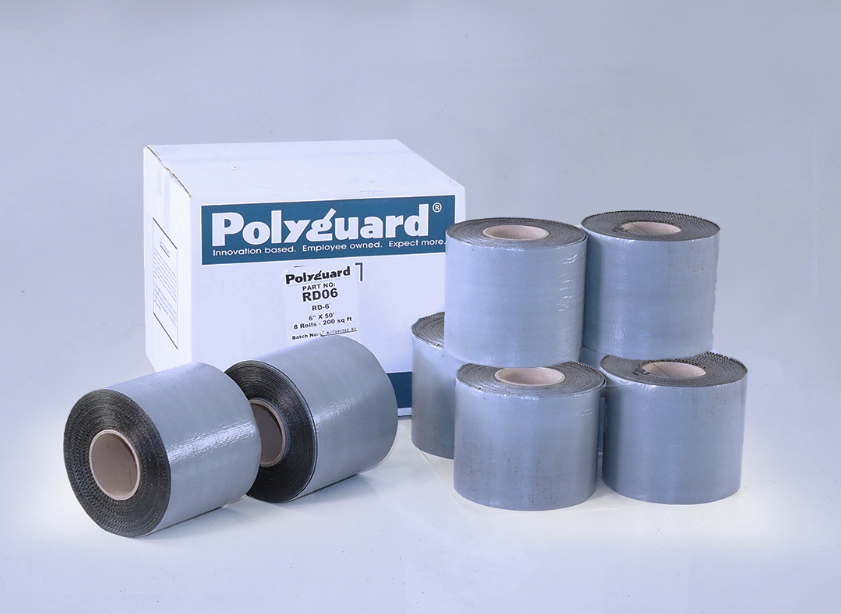
Non-shielding, anti-corrosion Polyguard RD-6® Coating System can be used on buried and submerged line pipe, rehabilitation, and new construction girth welds (operating at temperatures not exceeding 145°F (63°C)).
The Polyguard RD-6® coating system includes a tightly woven, strong polypropylene geotextile fabric that bonds to the coating on the pipe's outside surface to provide non-shielding properties, low elongation, and high breaking strength. The woven geotextile polypropylene backing also creates tension and compression during RD-6® application to ensure long-term performance.
In addition, we offer several coating and outer wrap products for above-ground, high temperatures, and larger pipe diameters.
- Above-ground pipes require an application of UV Overcoat to protect against harmful UV rays.
- For pipe diameters larger than 4 inches, we recommend applying Polyguard SP-6™ Unbonded Outerwrap over the RD-6® coating. The outer wrap produces an inexpensive, non-shielding layer to reduce damage from soil stress.
Benefits and Features of Polyguard RD-6® Coating System
Fast and Efficient No Cure Application
- Comes in rolls for easy application using Polyguard-approved machines like the Wrapster or power-operated machine
- Includes a silicone-coated release liner to prevent the layers from adhering to each other and assist in the application process
- Offers factory-controlled thickness
- Allows for immediate backfill
Durability
- Non-shielding design of the geotextile backing's open weave allows corrosion protection currents to pass to help prevent corrosion
- Resists disbondment from a pipe even if surface preparation is less than perfect
- Backing contains several features that resist soil stress from backfill pressure as it settles around the pipeline, which can lead to disbondment
- Heat-resistant backing with polypropylene provides 75 percent more resistance to weakening (relax or stretch) in high heat than polyethylene
- High tensile strength backing starts stronger than HDPE shrink sleeves and tapes
- Backing stretches 1/20th as shrink sleeves or tapes
NHT-5600™ Corrosion Barrier Epoxy Coating
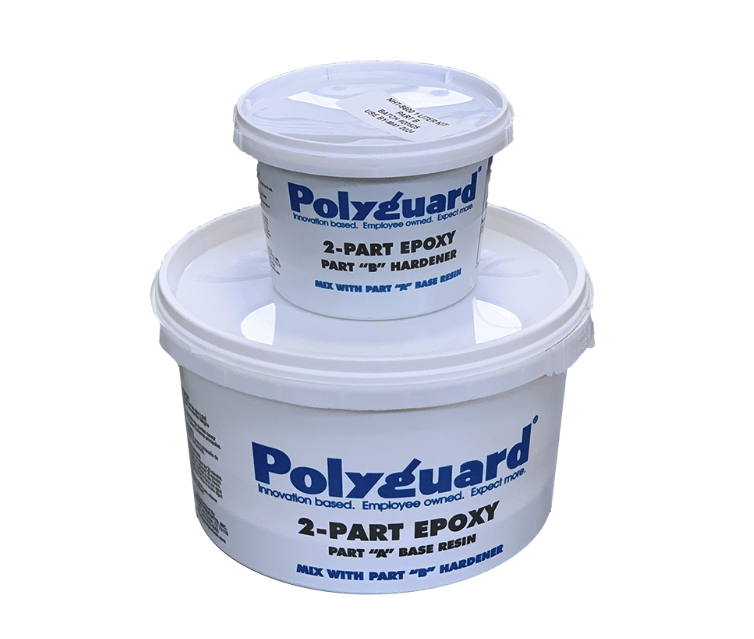
The design of VOC-free, 100-percent solid NHT-5600™ corrosion barrier epoxy coating works with fusion bond epoxy (FBE) coated steel pipe to create superior adhesion to steel. At the same time, the substrate maintains its cathodic protection. NHT-5600™ on bare or epoxy-coated steel pipes will extend the epoxy's useful life (30 - 50 percent over competitors) while maintaining a comparable cure time to other epoxies.
Applications of NHT-5600™ include:
- Repairing FBE-coated pipe
- Protecting the pipeline's field joint girth welds, fittings, and valves
- Coating for directional drill (ARO) and road bore pipe
- Existing pipeline coating rehabilitation.
The Benefits and Features of Polyguard NHT-5600™
Application Benefits
- Quick touch, dry, and cure times
- Isocyanate free
- Applicable as an ARO coating
- High build (up to 50 mils in a single coat)
- Meets AWWA C210 Standards for Liquid Epoxy Coating Systems for Steel Water Pipelines
- Meets CSA Z245-30 Standards for Field-Applied External Coatings and Steel Pipeline Systems
Durability
- NHT-5600™ provides superior high-temperature cathodic disbondment resistance
- Superior adhesion features that complement FBE-coated pipe
- Impact resistant
- Excellent chemical resistance
- High abrasion and impact resistance appropriate for horizontal drilling applications
- Excellent high temperature (185ºF(85ºC)) cathodic disbondment resistance
Polyguard IRO™ and IRO™ HD
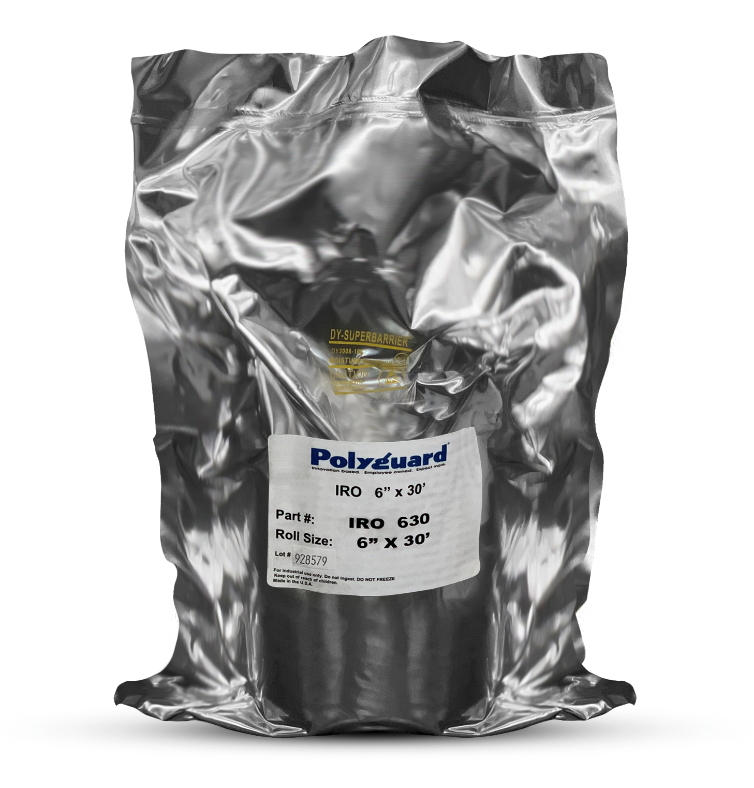
Abrasion-resistant Polyguard IRO™ (Impact Resistant Outerwrap, 0.013-inch thick layer) and IRO™ HD (Heavy Duty, 0.034-inch thick layer) create an outer layer. The layer protects pre-approved field joint and mainline coatings (RD-6®, liquid epoxies, Fusion Bond Epoxy (FBE, etc.) from abrasion damage for many applications, including:
- Air-to-soil transitions
- Aggressive soil conditions
- Mainline coating protection
- HDD (Horizontal Directional Drilling)
- Thrust boring and microtunneling
- Field-applied ARO (Abrasion Resistant Overlay)
Polyguard recommends using the IRO™ system as a protective layer for field joints installed by a trenchless method, which could impact a high-consequence area (HCA) like a road, populated space, building, or water.
Note: IRO™ application assumes correct application of the underlying coatings and, if required, completion of inspection before the IRO™ application
Benefits and Features of Polyguard IRO™ and IRO™ HD
- Non-shielding and non-hazardous
- 100-percent solids content
Straightforward Installation
- IRO™ and IRO™ HD-controlled set times, packaging, and conformability contribute to efficient installations with consistent applications.
- The system's easy application allows for speedy coating protection and backfill.
- IRO™ and IRO™ HD products help pipeline operators apply girth weld coatings at a perfect thickness to realize optimum performance with the corrosion barrier.
Note: Increasing the coating's thickness will reduce its flexibility and impact resistance.
Superior Flexibility and Gauge and Impact Resistance
- IRO™ and IRO™ HD products incorporate fibers to enhance the system's flexibility and gouge and abrasion resistance while also maintaining the resin's effectiveness.
- The IRO™ and IRO™ HD products eliminate the potential for re-pulling pipes or expensive spot repairs. They also offer exceptional mechanical protection of the underlying field-joint and mainline coatings.
- It minimizes repairs.
Help with Code Compliance
- Polyguard IRO™ and IRO™ HD work with cathodic protection systems to utilize DOT and PHMSA codes.
Polyguard Coatings for Gas and Oil Pipelines
Steel gas and oil pipeline design must provide quality materials and methods, like Polyguard Pipeline Coatings, to protect against problems that can damage the pipeline and coating's integrity.
For more on steel gas and oil pipeline design, don't hesitate to contact our professionals today at Polyguard's Pipeline Division at 214-515-5000 or email pipeline@polyguard.com.