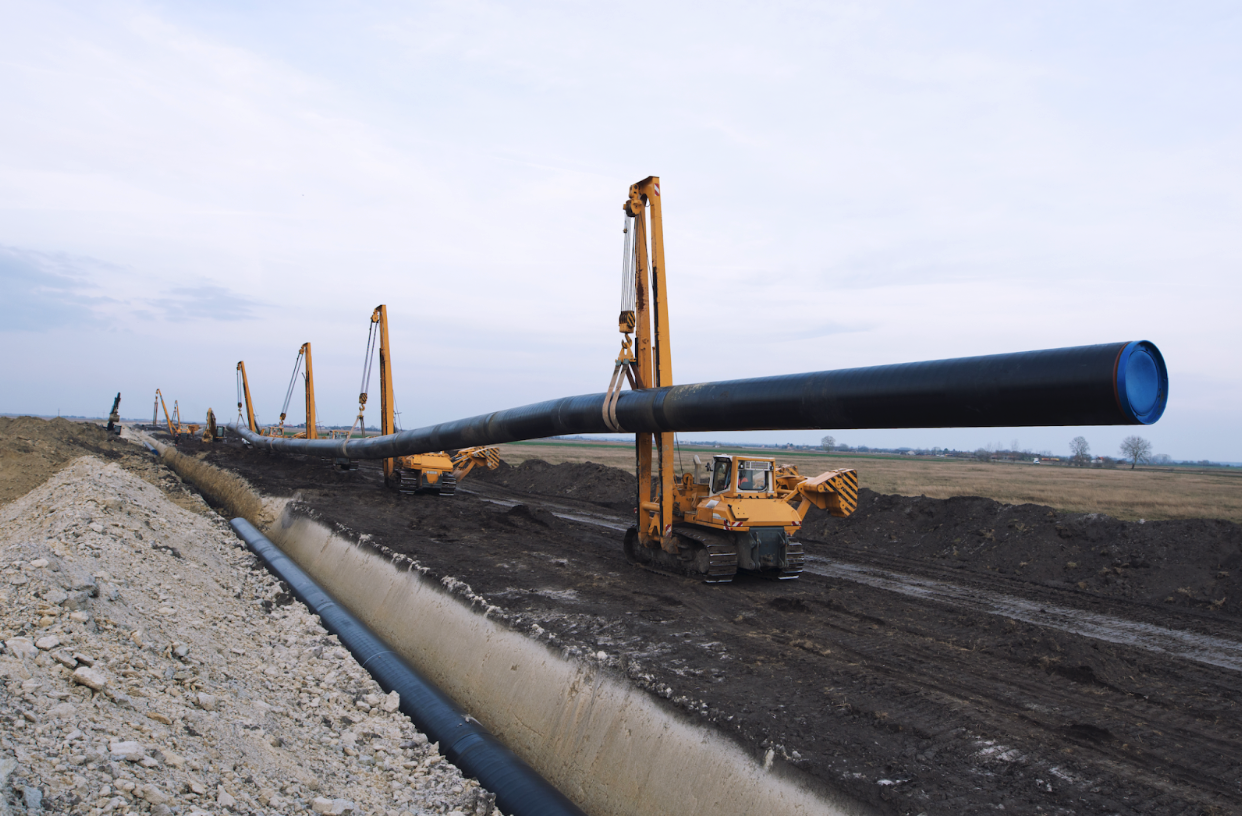
Oil and gas pipelines are the backbone of energy transportation, playing a critical role in delivering resources efficiently and safely across vast distances. Understanding the construction process of these pipelines provides insight into their significance and the technical precision required to build them. This article details the entire construction process, highlighting different types of pipelines and the importance of maintaining them using advanced products like those from Polyguard.
Types of Pipelines
Oil Pipelines
These pipelines transport crude oil from extraction sites to refineries and then to distribution centers. Oil pipelines are typically made from steel, which offers the strength needed to handle the high pressure and volume of transported oil. They are essential for the efficient movement of oil, reducing reliance on more hazardous and less efficient transportation methods like trucks and ships.
Gas Pipelines
Natural gas pipelines carry gas from production sites to processing facilities and eventually to consumers. These pipelines are crucial for delivering natural gas, a cleaner alternative to other fossil fuels, efficiently and safely. Gas pipelines use materials such as steel for high-pressure transmission lines and plastic for lower-pressure distribution networks.
The Pipeline Construction Process
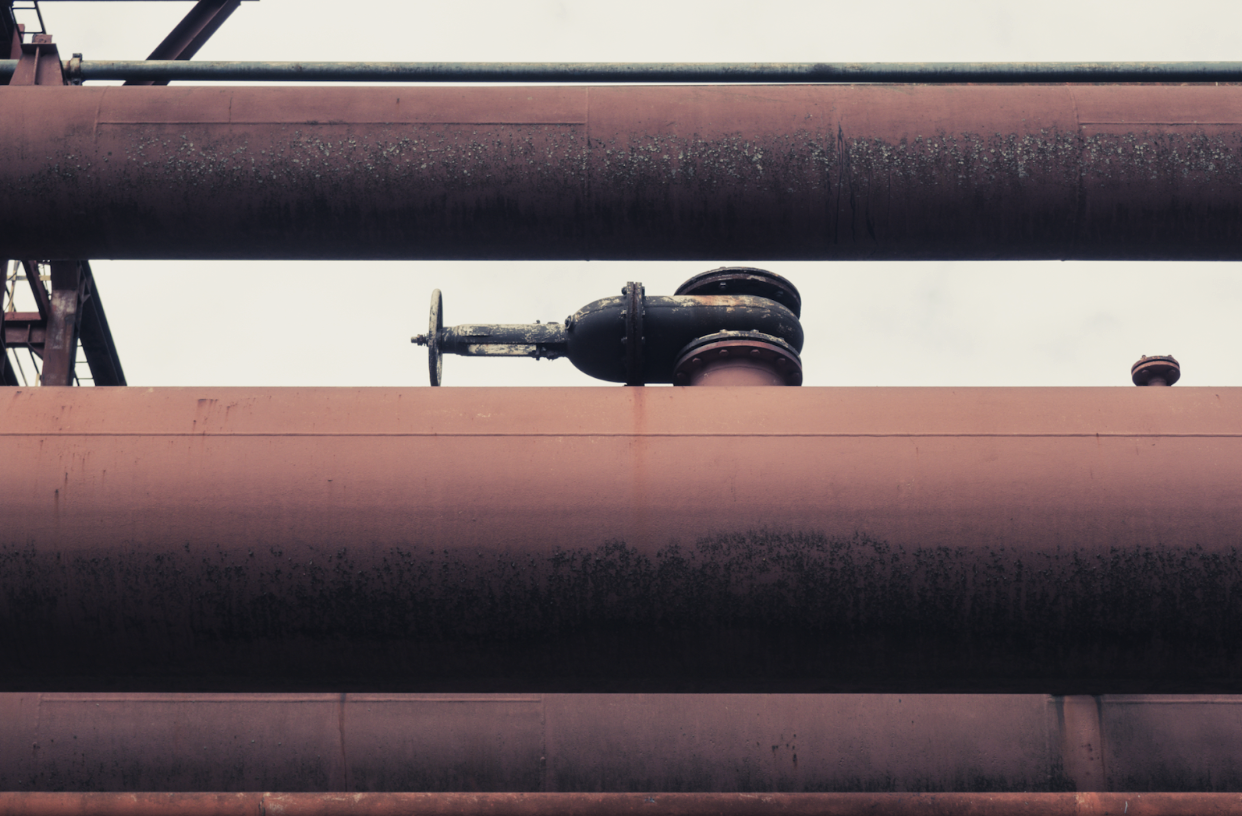
Planning and Design
Route Selection
Choosing the right route for a pipeline involves extensive environmental impact assessments, land use evaluations, and regulatory approvals. The goal is to minimize environmental disruption while ensuring the most direct and cost-effective path.
Design Specifications
The design phase considers various technical aspects, including the selection of materials, pipeline diameter, wall thickness, and pressure ratings. These specifications ensure the pipeline can withstand operational demands and environmental conditions.
Pre-Construction Activities
Clearing and Grading
The initial step in pipeline construction is clearing the right-of-way (ROW). This involves removing vegetation, trees, and other obstacles to create a clear path for the pipeline. Grading ensures the terrain is level, providing a stable foundation for further construction activities.
Trenching
Once the ROW is cleared, trenches are excavated to lay the pipeline. Trenching requires precise equipment like diggers and bulldozers. In rocky areas, jackhammers may be used to break through hard surfaces. The trench must be deep enough to protect the pipeline from external damage.
Pipeline Assembly and Welding
Pipe Stringing and Bending
Pre-coated segments of pipe, usually 40 feet in length, are transported to the construction site and laid out along the trench. Special tools are used to bend the pipes to fit the terrain and planned route. Proper alignment is critical to ensure seamless connections.
Welding
Welding is a crucial part of pipeline construction, requiring meticulous attention to detail. The process involves several steps: root pass welding, hot pass, fill passes, and capping. Each weld is inspected using radiographic techniques to ensure it meets quality standards. The weld joints are then coated with epoxy to prevent corrosion.
Coating and Wrapping
Field Joint Coating
After welding, the joints need to be coated to prevent corrosion. Heat-shrinkable sleeves or epoxy coatings are commonly used. Proper surface preparation, such as sandblasting, is essential to ensure the coating adheres well and provides long-lasting protection.
Lowering and Backfilling
Lowering the Pipeline
The assembled pipeline sections are carefully lowered into the trench. This step requires precise handling to avoid damaging the pipe's coating. Sand padding and rock shields may be used in rocky areas to provide additional protection.
Backfilling
Once the pipeline is in place, the trench is backfilled with soil. The fill material should be free of rocks and debris that could damage the pipeline. In areas with steep gradients, slope breakers are installed to prevent soil erosion and trench washout.
Testing and Commissioning
Hydrostatic Testing
Before a pipeline is put into operational use, it must undergo rigorous hydrostatic testing. This crucial step involves pumping water through the pipeline at high pressure to check for leaks and to ensure the structural integrity of the system. This test is critical to verify that the pipeline can safely handle the operational pressures and stresses it will face.
Commissioning Process
After successful hydrostatic testing, the pipeline enters the commissioning phase, which ensures the system is fully ready for operational service. This phase includes several key steps:
- System Validation: This involves checking and validating all integrated systems associated with the pipeline, such as pumps, valves, and control systems, to ensure they function correctly and as expected.
- Safety Checks: Additional safety inspections are conducted to confirm all safety measures are in place and effective. This includes emergency response drills and reviews of safety protocols to ensure rapid and effective responses to any incidents.
- Operational Handover: The final step in the commissioning process is the operational handover from the construction team to the operations team. This includes comprehensive training for the operations staff on system management and response strategies, along with the transfer of all necessary documentation and operational manuals.
By meticulously following these steps, the pipeline is ensured not only to be physically robust but also functionally ready, with all safety and operational protocols firmly established. This thorough commissioning process helps in minimizing operational risks and ensures the long-term efficiency and safety of the pipeline system.
Maintenance of Pipelines with Polyguard
To maintain oil and gas pipelines effectively, Polyguard offers several products designed to protect against corrosion and environmental damage. Here are some key products from Polyguard that fit into the category of maintenance for pipelines:
Pipeline Coatings and Wraps
Polyguard provides a range of protective coatings and wraps designed to shield pipelines from corrosion. These include RD-6 Coating System, which prevents corrosion without requiring sandblasting, and the Polyguard Innerseal, which offers superior moisture protection.
RG-2400 Series
This series is designed to prevent corrosion under insulation (CUI). It includes products that provide a durable barrier to moisture and contaminants, ensuring the longevity of pipelines.
Weatherproof Jacketing
Polyguard’s weatherproof jacketing solutions protect pipelines from external environmental factors, such as UV exposure and mechanical damage, which can degrade the pipeline over time.
Vapor Barriers
These barriers prevent moisture ingress, which can lead to internal corrosion of the pipeline. Polyguard offers several types of vapor barriers suited for different environmental conditions.
Insulation Systems
Effective insulation is crucial for maintaining pipeline efficiency and preventing thermal damage. Polyguard's insulation products, such as the Insulrap product line, offer robust thermal protection for pipelines.
By using these products, pipeline operators can ensure that their infrastructure remains in optimal condition, reducing the risk of leaks and prolonging the service life of the pipelines.
Enhance Your Pipeline Construction with Polyguard
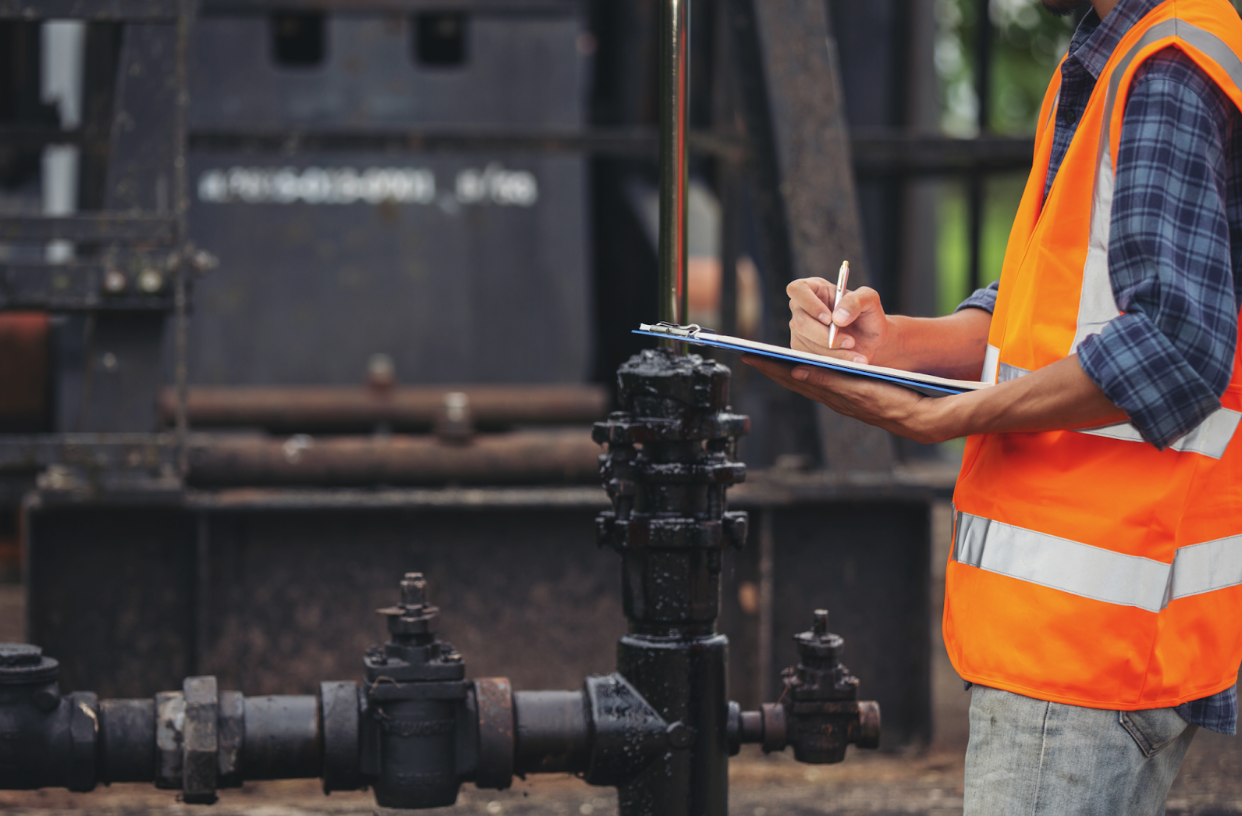
Polyguard specializes in high-quality waterproofing and pipeline protection solutions, ensuring the longevity and integrity of your construction projects. Our extensive range of products, including advanced coatings and membranes, offers robust protection against corrosion and environmental damage. Our expertise in pipeline construction and maintenance provides unparalleled support for your projects. Contact us today for more information.