Underground pipeline leaks happen for many reasons, and every leak is different. Therefore, it’s important to know and use a series of underground pipeline leak detection methods when you’re trying to identify the cause and location of the leak.
If you’re trying to figure out where the leak is within your pipeline, that’s okay.
In this article, we’re going to discuss the different causes of pipeline leaks and highlight a few methods to help you detect where your underground pipeline leaks are coming from.
Are you ready?
Causes of Underground Pipeline Leaks
Underground pipelines are susceptible to leaks due to various factors, though it typically comes down to three main factors: corrosion, damage, and defects. For instance:
Corrosion on underground pipelines often results from chemical reactions between the pipeline material and its environment, and mechanical damage can occur during excavation, construction, or renovation activities. Material defects, such as flaws in the pipeline’s manufacturing process, can also lead to weaknesses over time and contribute to the development of leaks.
The Importance of Rapid Leak Detection and Repair
Timely detection and repair of underground pipeline leaks are critical to preventing extensive environmental damage, reducing economic losses and mitigating safety hazards.
However, if leaks are not detected early enough, they can often contaminate soil and pose fire and explosive risks—or simply lead to significant waste of resources.
6 Effective Underground Pipeline Leak Detection Methods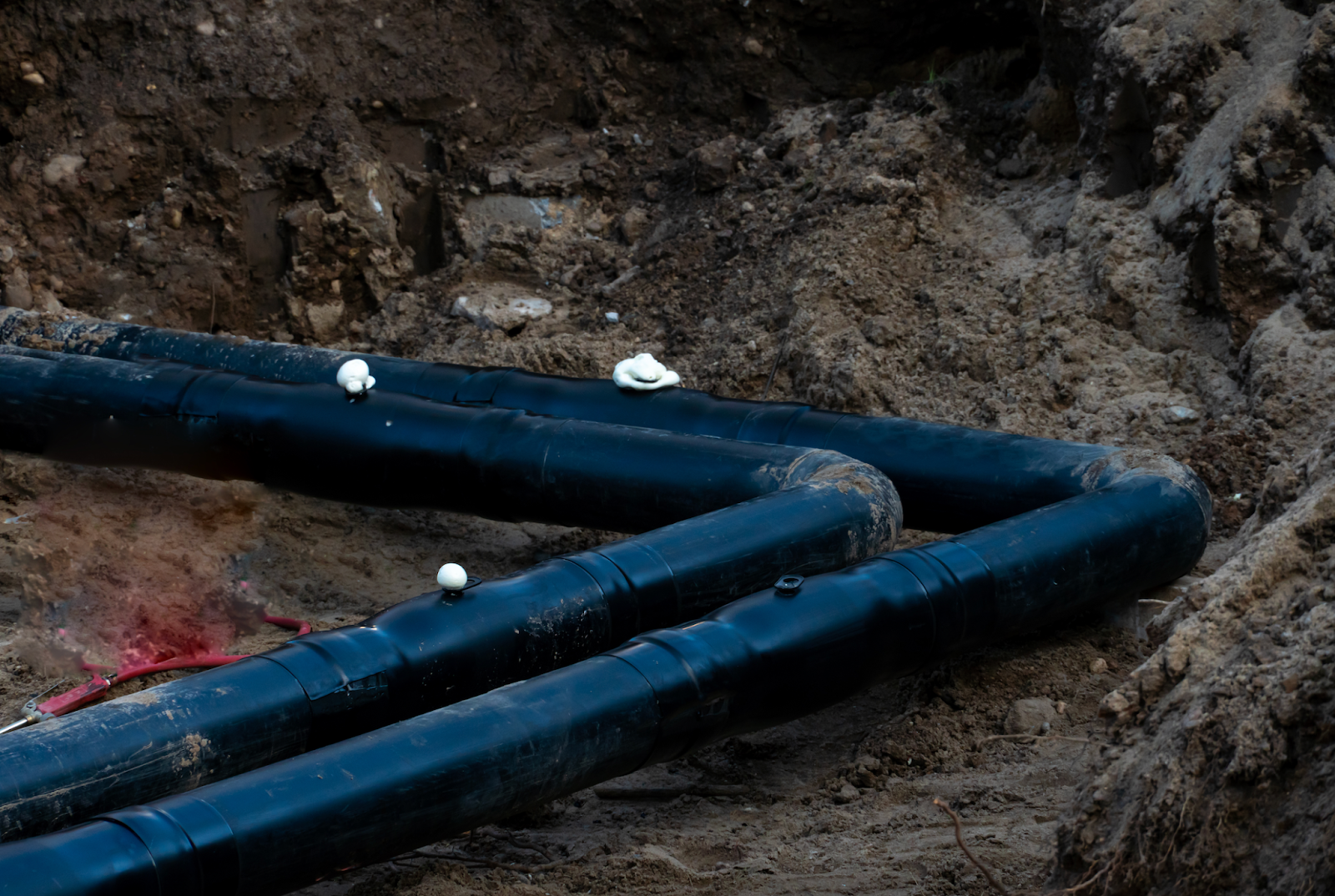
1. Acoustic Monitoring
Acoustic monitoring uses sound sensors to detect the noise generated by leaking fluids. This method is highly effective for pinpointing the exact location of leaks.
2. Fiber Optic Sensing
Fiber optic sensing involves running fiber optic cables along the pipeline to detect temperature changes and vibrations.
3. Electromagnetic Testing
Electromagnetic testing uses electromagnetic fields to identify changes in the pipeline structure that indicate a leak. It is often used for both metallic and non-metallic pipelines.
4. Ground Penetrating Radar
Ground penetrating radar (GPR) sends radar pulses into the ground to detect changes in the subsurface environment. GPR is particularly effective for detecting leaks in non-metallic pipelines.
5. Infrared Thermography
Infrared thermography uses thermal cameras to detect temperature anomalies caused by leaking fluids, which can be used for many pipeline materials
6. Pressure Testing
Pressure testing involves monitoring pressure changes within the pipeline to detect leaks. This is arguably the simplest underground pipeline leaked detection method.
The Advantages and Disadvantages of Each Underground Pipeline Leak Detection Method
Because each leak is different and requires different underground leak detection methods, let’s take a look at the option above and explore the advantages and disadvantages of each.
Acoustic Monitoring
Advantages
- High Precision: Acoustic monitoring excels in pinpointing the exact location of leaks to provide highly accurate detection.
- Non-Intrusive: It does not require extensive modifications to the existing pipeline infrastructure.
Disadvantages
- Technical Expertise Required: Interpreting the acoustic data accurately necessitates skilled technicians.
- Potential Interference: External noises and vibrations can sometimes interfere with the detection accuracy.
Fiber Optic Sensing
Advantages
- Real-Time Monitoring: This method offers continuous, real-time data on pipeline conditions.
- Wide Area Coverage: Fiber optic cables can effectively monitor extensive pipeline sections.
Disadvantages
- High Installation Costs: The initial setup cost for fiber optic sensing is substantial.
- Vulnerability to Damage: The system is sensitive to external damage, which can affect its reliability.
Electromagnetic Testing
Advantages
- Versatile Application: It is effective for both metallic and non-metallic pipelines.
- Non-Invasive: The method does not require direct contact with the pipeline, to help preserve its integrity.
Disadvantages
- Depth Limitations: The accuracy can be compromised at greater depths.
- Environmental Sensitivity: External environmental conditions can influence the effectiveness of the method.
Ground Penetrating Radar (GPR)
Advantages
- Effective for Non-Metallic Pipelines: It is particularly useful for detecting leaks in pipelines made of materials like plastic.
- Detailed Subsurface Imaging: It provides comprehensive subsurface images to aid in precise leak detection.
Disadvantages
- High Initial Costs: The equipment and setup costs are relatively high.
- Requires Skilled Operators: Effective use of GPR demands trained professionals to interpret the data accurately.
Infrared Thermography
Advantages
- Visual Data: It offers clear visual representation of temperature anomalies to aid in leak detection.
- Adaptability: It can be used in various environmental conditions to enhance its utility.
Disadvantages
- Limited Depth Detection: The effectiveness is reduced for deeper pipelines.
- External Temperature Influence: Ambient temperature variations can affect the accuracy of the thermal readings.
Pressure Testing
Advantages
- Cost-Effective: Pressure testing is relatively simple and inexpensive to conduct.
- Straightforward Implementation: It is easy to perform without requiring extensive modifications to the pipeline system.
Disadvantages
- Limited Localization: While it can confirm the presence of a leak, it may not pinpoint the exact location without supplementary methods.
- Potential for False Positives: Pressure fluctuations can sometimes be caused by factors other than leaks that can lead to false positives.
Polyguard Solutions for Underground Pipeline Leak Prevention
Polyguard offers a comprehensive range of products designed to prevent leaks in pipelines to help ensure the longevity and reliability of the infrastructure.
Below are some key products specifically tailored for pipeline leak prevention:
RD-6® Coating System
The RD-6® Coating System is a top-notch external anti-corrosion solution for buried and submerged pipelines. It's perfect for new construction girth welds and long line rehabilitation. This system includes a liquid adhesive, a geotextile-backed protective coating, and a durable polypropylene geotextile fabric outerwrap. Together, these components offer high tensile strength, low elongation, and excellent resistance to soil stress, to help ensure pipeline integrity. For pipelines operating above 145°F, use the RD-6 HT variant.
606 Filler Compound
The 606 Filler Compound is designed for filling and sealing joints and seams in pipelines. This compound is flexible, durable, and resistant to a wide range of chemicals, to help ensure that pipelines remain sealed and protected against potential leaks. It is easy to apply and provides long-term protection against corrosion and leaks.
RG-2400® Corrosion Control Gel
RG-2400® is an anti-corrosion gel that uses Polyguard’s unique mineralization technology that effectively prevents the corrosion process by creating a mineral barrier on the metal surface. This gel is particularly useful for preventing corrosion under insulation in piping systems, valves, tanks, and vessels. RG-2400 is non-drying, non-sag, and easy to apply, which makes it a reliable solution for both new and existing pipelines.
IRO & IRO HD (Impact Resistant Outerwrap)
The Impact Resistant Outerwrap (IRO™) and the IRO Heavy Duty (IRO™ HD) products safeguard field joint and mainline coatings from damage caused by backfilling, drilling, and other conditions. These wraps are constructed from durable fiberglass material infused with a water-activated resin that solidifies within minutes to offer robust protection for the underlying surfaces. They are also compatible with cathodic protection systems to ensure comprehensive protection for pipelines.
These products are designed to provide comprehensive protection against environmental factors and mechanical damage, which makes them essential for maintaining pipeline infrastructure.
Enhance Underground Pipeline Safety with Polyguard’s Solutions
Looking to avoid using underground pipeline leak detection methods in the future?
Check out Polyguard’s advanced underground leak prevention solutions that range from protective coatings to filler compounds that are designed to address the unique challenges of underground pipelines.
If you have any questions, contact us today for more information.