Properly managing and mitigating pipe corrosion will help minimize the risk of damage to the pipeline’s integrity and help maintain its reliability and longevity while transporting everything from natural gas, liquid petroleum, biofuels, water, sewage, etc.
Without corrosion protection, the pipes will lose mechanical strength and develop exterior holes and cracks that can lead to breaks, floods, and billions of dollars annually in maintenance and repairs. Preventing pipe corrosion will also protect the safety and health of the nearby communities, ecosystem, and pipeline workers.
Pipeline corrosion prevention must protect against degradation and conduct cathodic protection currents should the coating become damaged or disbond; both features of Polyguard’s long-lasting RD-6® COATING SYSTEMS.
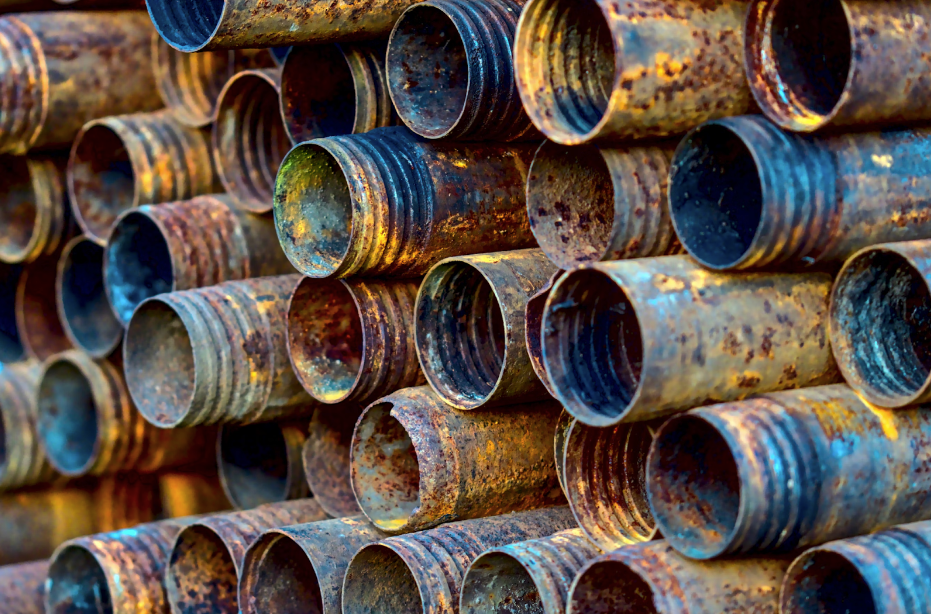
What Is Pipe Corrosion?
Pipe corrosion happens when the metal surface deteriorates due to an oxidation-reduction or redox reaction. Higher temperatures, salts, and acids will accelerate corrosion. The process of corrosion requires four elements:
- Anode - The site on the metal where oxidation occurs (loss of electrons) and metal deteriorates.
- Cathode - The site on the metal where reduction occurs (gain of electrons).
- Metallic Path - After the anode site loses its electrons, the electrons travel to the cathode area along the metallic path, where oxygen reduces and reacts with the oxidized metal (at the anode site) to form metal oxide (rust).
- Electrolyte (typically water) - Corrosion requires complete immersion of the anode and cathode sites in the electrolyte. The electrolyte (electrically conductive medium) facilitates the electron’s flow from the anode to the cathode.
Types of Pipeline Corrosion
All corrosion types deteriorate refined metal piping due to chemical interactions that naturally convert the metal to a more chemically stable form, like metal oxide (rust). However, each corrosion type needs particular protection methods to ensure the pipe's long-term integrity:
1. Galvanic Corrosion
Galvanic corrosion involves unlike metals of different corrosion resistance electrically connecting, which causes the anode area on the metal to deteriorate.
Preventing galvanic corrosion requires placing insulation between the two metals and using a combination of metals close in the galvanic series. Applying a non-shielding coating to the cathodic surface of the metal can also help stop galvanic corrosion.
2. Pitting Corrosion
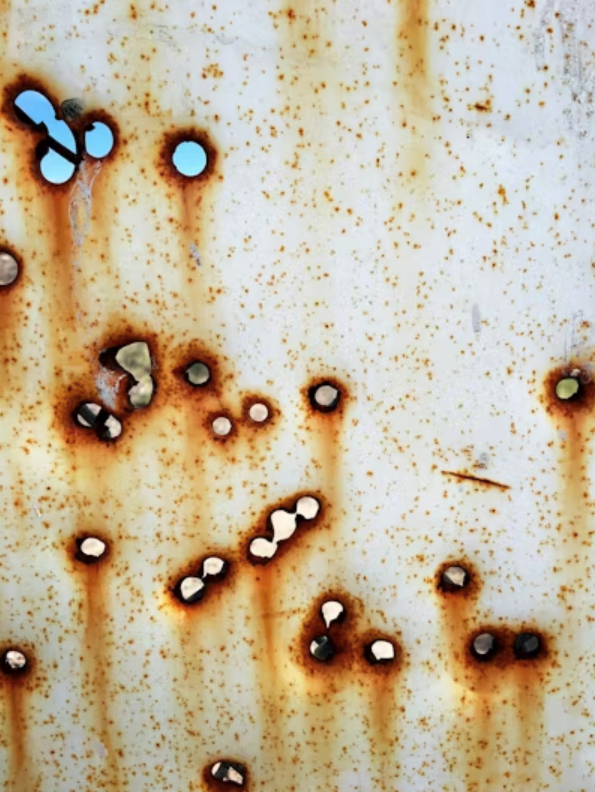
Several situations can lead to pitting corrosion: mechanical damage to the protective coating, pipe and surface material defects, and attack by aggressive chemical species, like chlorides. All can lead to dangerous, localized deterioration on a limited surface space that can create punctures and pits on a pipe's surface.
To stop pitting corrosion, choose a suitable pipe material for the service environment, considering the reactant’s chemical concentration (pitting resistance) and temperature. In addition, protect the cathodic and anodic with a sufficient coating to withstand the environment.
3. Uniform Pipe Corrosion
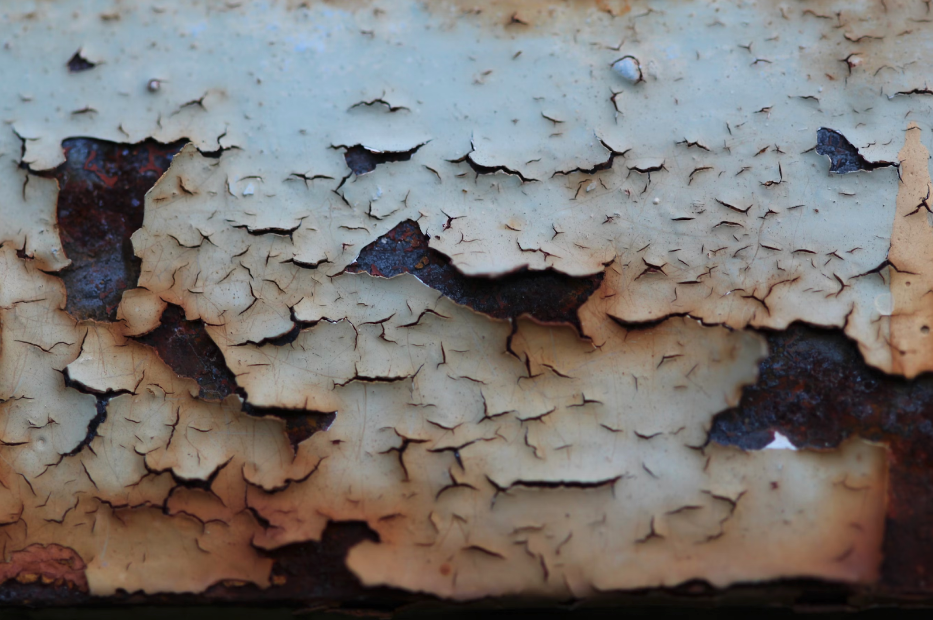
Uniform pipe corrosion causes consistent material loss along the pipe's surface, which could eventually lead to continuous thinning of the solid structure.
Preventing uniform pipe corrosion requires choosing an adequate piping material combined with corrosion protection methods like cathodic protection and surface coatings.
4. Selective Leaching (Graphitic Corrosion)
Selective leaching (graphitic corrosion) happens when a noble metal and a more reactive element create an alloy, which causes a loss of the reactive component from the pipe's surface, and reduces the pipe's strength.
Adding aluminum or tin can help protect against leaching.
5. Stress Corrosion Cracking
Stress corrosion cracking (fatigue corrosion) results from the growth of pre-existing cracks, causing the failure of metal pipes that surpass threshold stress levels under tensile stress, especially at high temperatures.
Keeping loads below the threshold stress levels can help stop stress corrosion cracking.
6. Crevice Corrosion
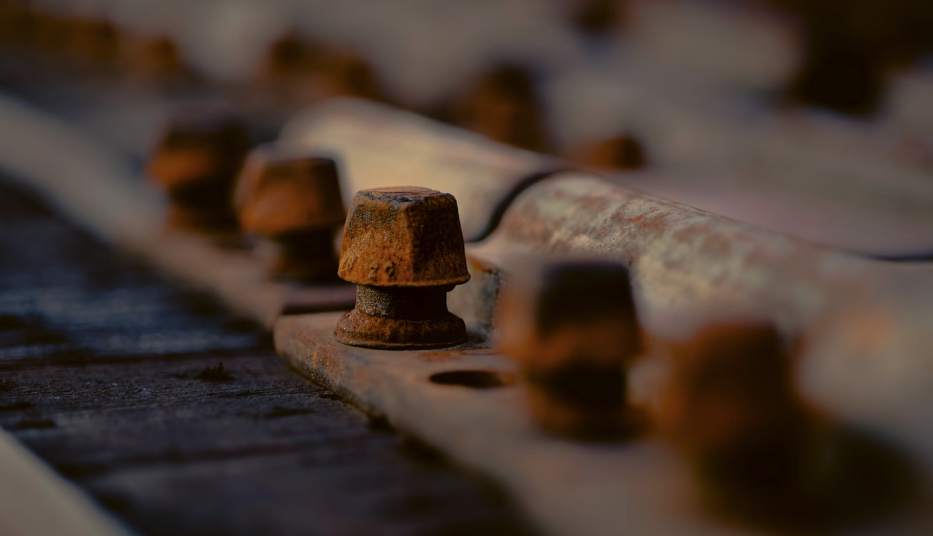
Crevice corrosion happens when oxygen-starved surfaces of a pipe's crevices or joints turn into the anode in an electrochemical reaction.
Using welded joints instead of riveted joints can help prevent crevice corrosion. Areas with step-downs or reductions in wall thickness can present spaces of concern for crevice corrosion and require attention when applying the anti-corrosion coating.
7. Stray Current Corrosion
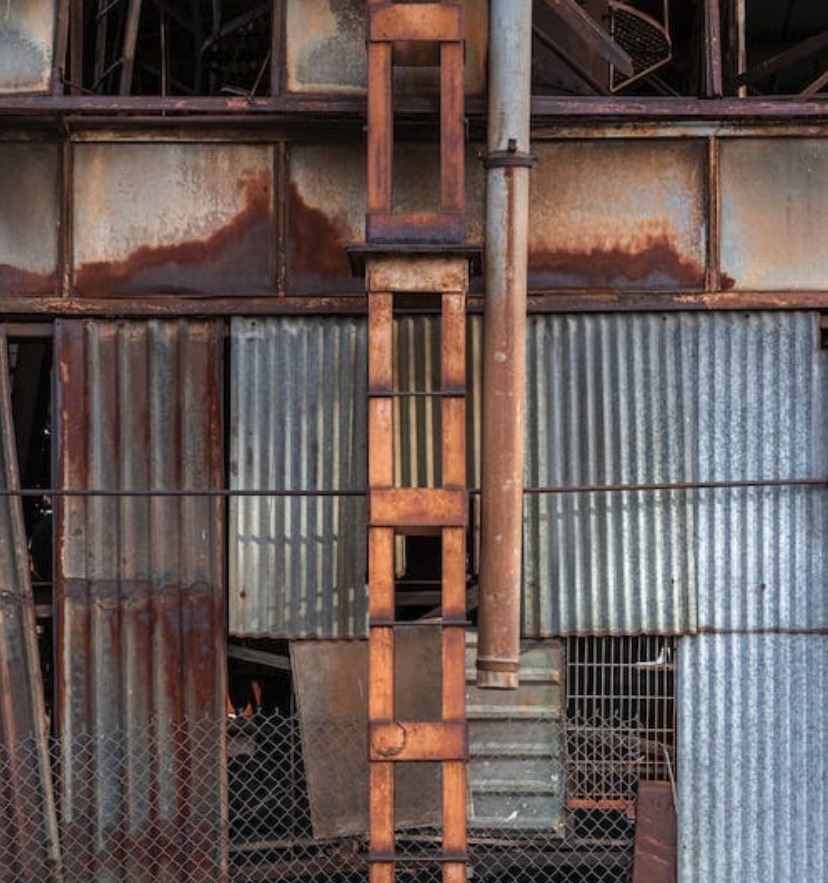
Stray currents (DC and AC) flowing through pipelines can cause stray current corrosion, which causes localized pinholes and pitting on metal surfaces at the exact points where stray currents exit the surface. Stray currents can come from cathodic protection, electric railways, welding machines, buried lines, or high overhead voltage.
You can lessen stray current corrosion by bypassing stray current to an earthing station or managing electricity leakages through bonds to other structures.
8. Intergranular Deterioration Corrosion
Grains comprise the microstructure of metals and alloys, and are separated by grain boundaries. Intergranular corrosion occurs along the grain boundaries or immediately adjacent to grain boundaries. Impurities (chemicals) precipitating on the grain boundaries often lower the area's corrosion resistance.
Using extra-low carbon stainless steel materials can help stop intergranular deterioration.
9. Cavitation and Erosion Corrosion
Cavitation and erosion-corrosion in a pipe occur when the fluid's working pressure is less than its vapor pressure. It causes vapor bubbles and pockets to form, which causes the pipe's internal surface to break and leads to erosion-corrosion.
Areas of a pipe particularly susceptible to erosion-corrosion include the discharge pipes, pump suctions, tees, elbows, expansions, fitments at heat exchangers, and valve seats.
There are several ways to prevent cavitation and erosion corrosion:
- Increase liquid pressures to minimize space for vapor bubbles to form
- Operate the system with the fluid at a consistent temperature below the boiling point to avoid vapor bubbles
- Use alloyed materials
- Reduce operational vibrations, which can lead to the formation of bubbles
10. High-Temperature Corrosion
High-temperature corrosion occurs under extreme temperatures (often above 400℃ (750℉)). Chemical attacks from gasses or molten metals that contain specific contaminants will produce high-temperature corrosion.
The oil and gas industries often favor using alloy pipes to prevent high-temperature corrosion. Alloy pipes comprise two or more metallic elements, like steel and chromium, which create greater strength and corrosion resistance.
Preventing Pipeline External Corrosion
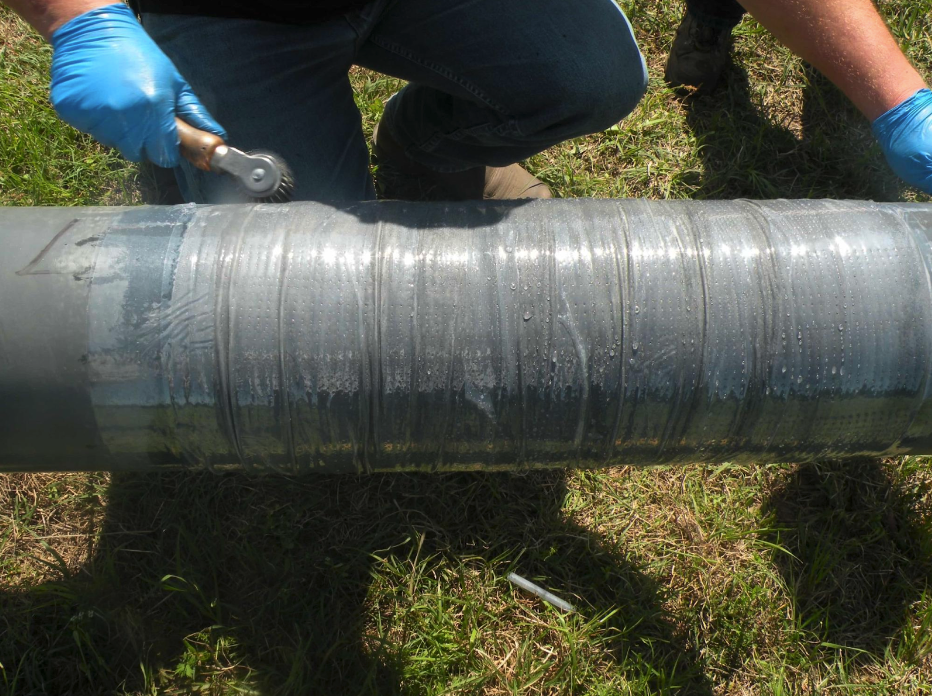
External surface corrosion on a steel pipe happens due to environmental conditions that cause an electrochemical interaction between the pipeline's exterior and the adjacent water, air, and soil.
The first line of defense in stopping external pipeline corrosion involves removing one of the four elements required for corrosion - cathodes, anode, metallic path, and electrolyte. A coating system can protect the pipeline from the electrolyte (often water) by acting as a barrier that breaks the corrosion cycle. In addition, some barrier coatings use sacrificial or inhibitive pigments that cause passivation or a sacrificial anode to form defects in the coating.
Cathodic protection (CP) currents offer a second line of defense that protect the pipe if the coating becomes damaged, which creates a corrosion-prone space. CP allows the cathodic current to reach the pipeline’s disbonded areas to raise the water’s pH between the pipe and disbonded coating to 9 or above - a value that does not support corrosion.
Preventing Pipe Corrosion with the POLYGUARD RD-6® COATING SYSTEM
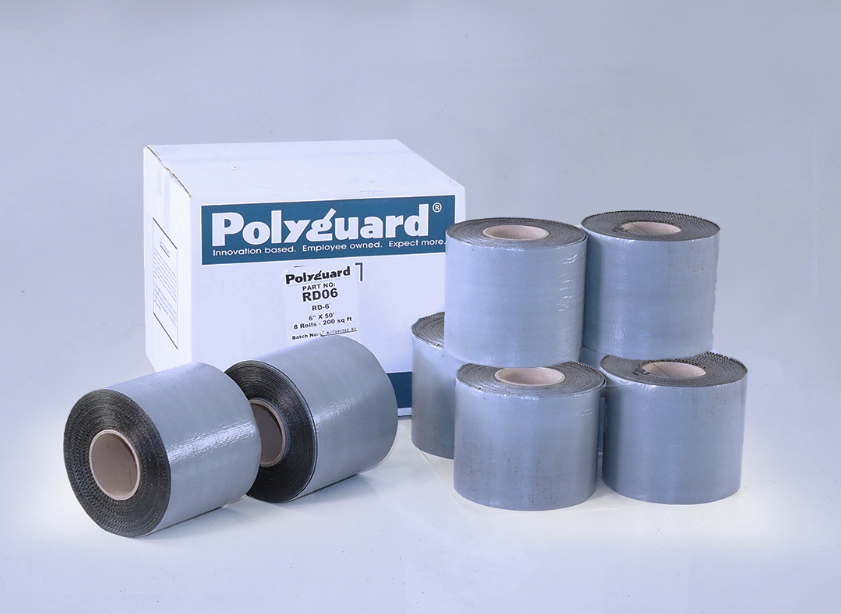
Polyguard Pipeline Coating products protect the pipelines' integrity by minimizing corrosion and providing impact, chemical, temperature, and ultraviolet (UV) resistance, strong adhesion, and straightforward application.
Polyguard RD-6® Coating System
The non-shielding, anti-corrosion Polyguard RD-6 Coating System can be used on submerged and buried line pipe, rehabilitation, and new construction girth welds (operating at no more than 145°F (63°C)).
The Polyguard RD-6® coating system comprises a tightly woven, robust polypropylene geotextile fabric that bonds to the coating on the pipe's exterior surface to furnish non-shielding properties, low elongation, and high breaking strength. The woven geotextile polypropylene backing produces tension and compression during RD-6® application, which ensures its lasting performance.
We also offer coatings and outer wrap products for high temperatures, above-ground, and larger pipe diameters:
- Above-ground pipes need an application of RD-6® UV Overcoat to protect against harmful UV rays.
- For pipe diameters greater than 4 inches, we recommend using Polyguard SP-6™ Unbonded Outerwrap over the RD-6® coating. The outer wrap produces a non-shielding layer to lessen further damage from soil stress.
Benefits of the Non-Shielding RD-6® COATING SYSTEM
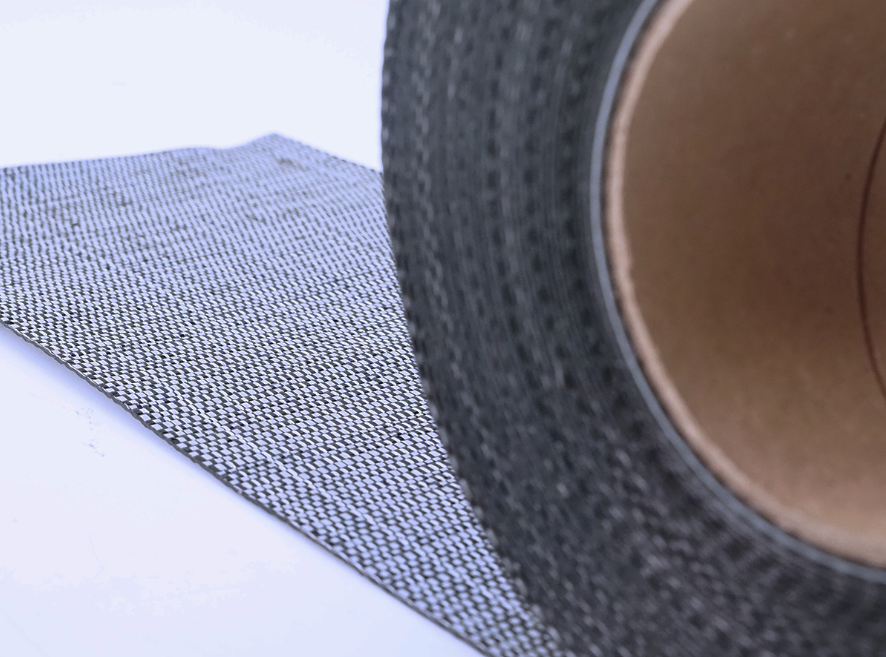
Provides Corrosion Protection Currents
RD-6® COATING SYSTEM’s non-shielding design, with its geotextile backing’s open weave, allows for the passage of corrosion protection currents to damaged or compromised areas of the coating, to elevate the pH of the electrolyte in the space to above 9, which will not support corrosion.
Durable and Long-Lasting
Soil-stress-resistant RD-6® limits disbondment from the pipe, even with less-than-perfect surface preparation.
Simple to Apply
Polyguard manufactures RD-6® coating in rolls for straightforward application using a Polyguard-approved machine like the Wrapster or power-operated machine.
The Polyguard Wrapster has two spindles: one offers tension when applying the RD-6® coating to the pipe. The other spool releases the liner when applying. You can also apply RD-6® manually without the Wrapster if you apply tension consistently during the application.
In addition, RD-6® does not require curing. It includes a silicone-coated release liner to prevent the layers from adhering to one another and help in the application process.
Pipe Corrosion Prevention with the POLYGUARD RD-6® COATING SYSTEM
The dependable and verified POLYGUARD RD-6® Coating System has protected pipes for over thirty years from external corrosion and stress corrosion cracking. The non-shielding RD-6® Coating System offers superior, long-lasting pipe corrosion prevention and provides cathodic protection currents during disbondment.
Contact our Polyguard professionals today for more on types of corrosion and how to prevent them!