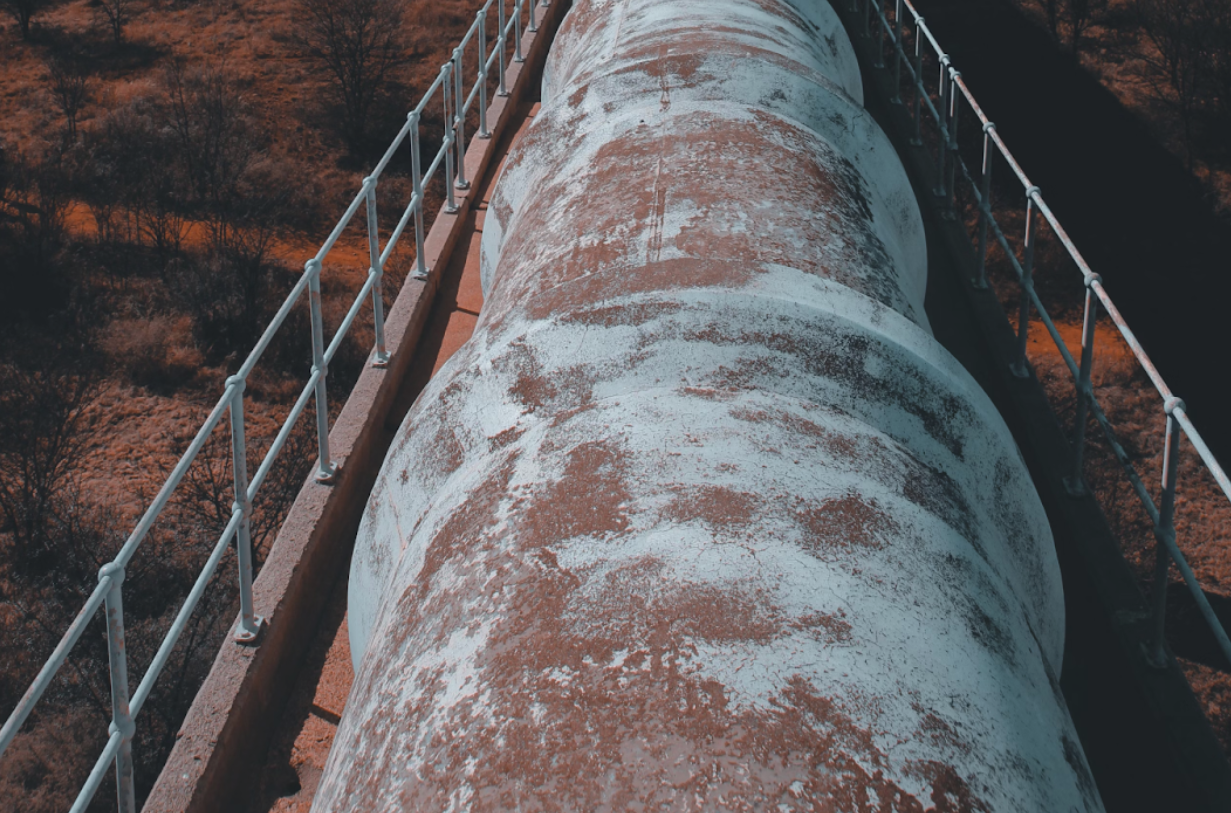
Underground pipelines are crucial for our industry and society by efficiently moving important resources across continents. However, the hidden problem of corrosion threatens these key pipelines that creates risks for safety, the economy, and the environment. Tackling underground pipeline corrosion is essential, not just a technical challenge, but a must for our modern lifestyle.
Understanding Underground Pipeline Corrosion
What is Underground Pipeline Corrosion?
Corrosion happens when metals break down in certain environments and causes underground pipelines to weaken. This mostly occurs due to chemical reactions between the pipe and its environment.
Types of Corrosion Affecting Underground Pipelines
Galvanic Corrosion
This form of corrosion worsens notably when an electrolyte, like water, which facilitates the electrical connection, is conducive. This accelerates the corrosion process considerably, especially in underground environments.
Microbiologically Influenced Corrosion (MIC)
The presence of certain bacteria can accelerate corrosion by creating environments that are more acidic or by directly consuming metal as part of their metabolic processes, which makes MIC particularly challenging to predict and manage.
Stress Corrosion Cracking (SCC)
The danger of stress corrosion cracking (SCC) lies in its ability to remain undetected for long periods, as the initial micro-cracks are difficult to observe, which often leads to sudden and catastrophic pipeline failures when they finally propagate.
Causes of Underground Pipeline Corrosion
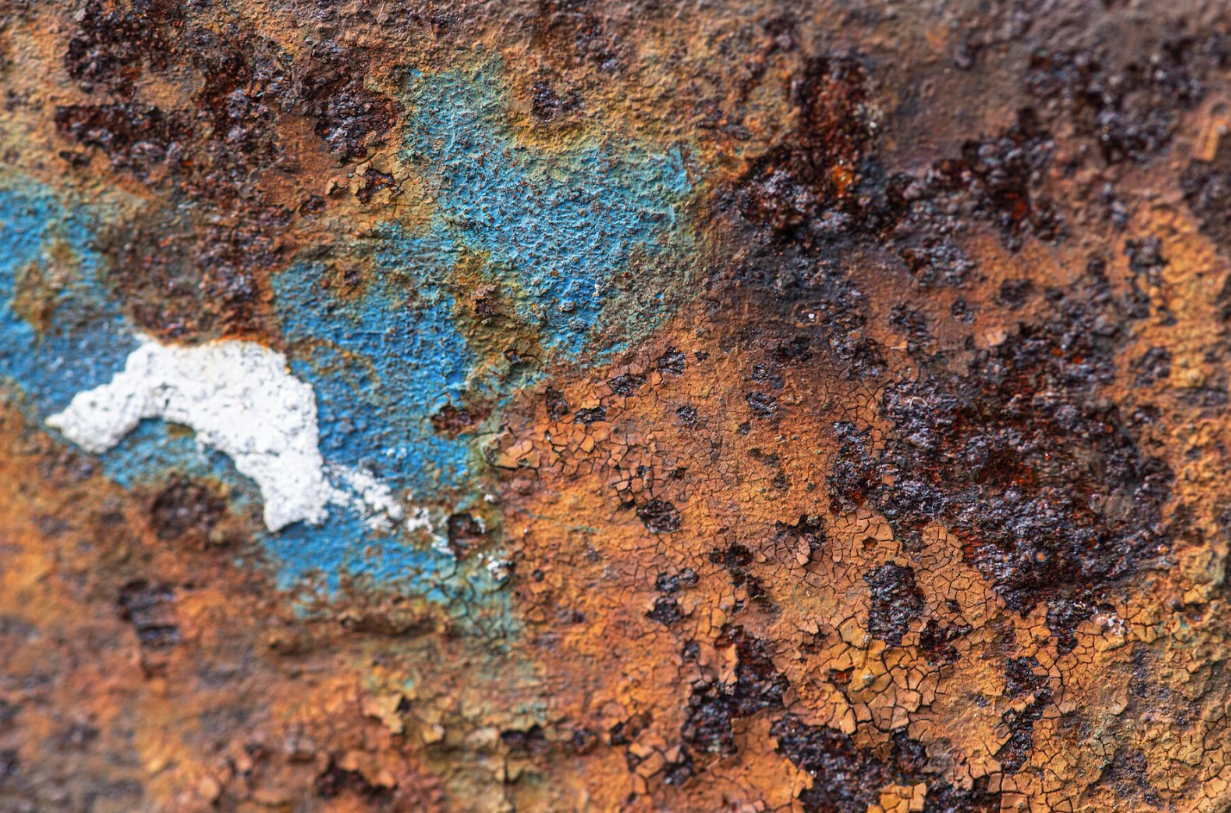
Understanding the multifaceted causes of underground pipeline corrosion is crucial for developing effective prevention strategies. Two primary factors stand out:
Soil Properties
pH and Electrical Conductivity
The chemical composition of soil, including its pH level and electrical conductivity, can significantly influence the rate of corrosion. Acidic soils or those with high conductivity can accelerate the corrosion process, which necessitates tailored protection strategies for pipelines in different geographical areas.
Operational Conditions
Pressure and Flow Rates
Variations in the operational conditions of pipelines, such as changes in pressure and flow rates, contribute to the mechanical wear and tear that can expedite corrosion. This dynamic nature of pipeline operation underscores the importance of adaptive management and maintenance plans.
These points highlight the need for thorough corrosion management plans that consider the complicated effects of environmental and operational factors on pipeline integrity.
Impact of Pipeline Corrosion
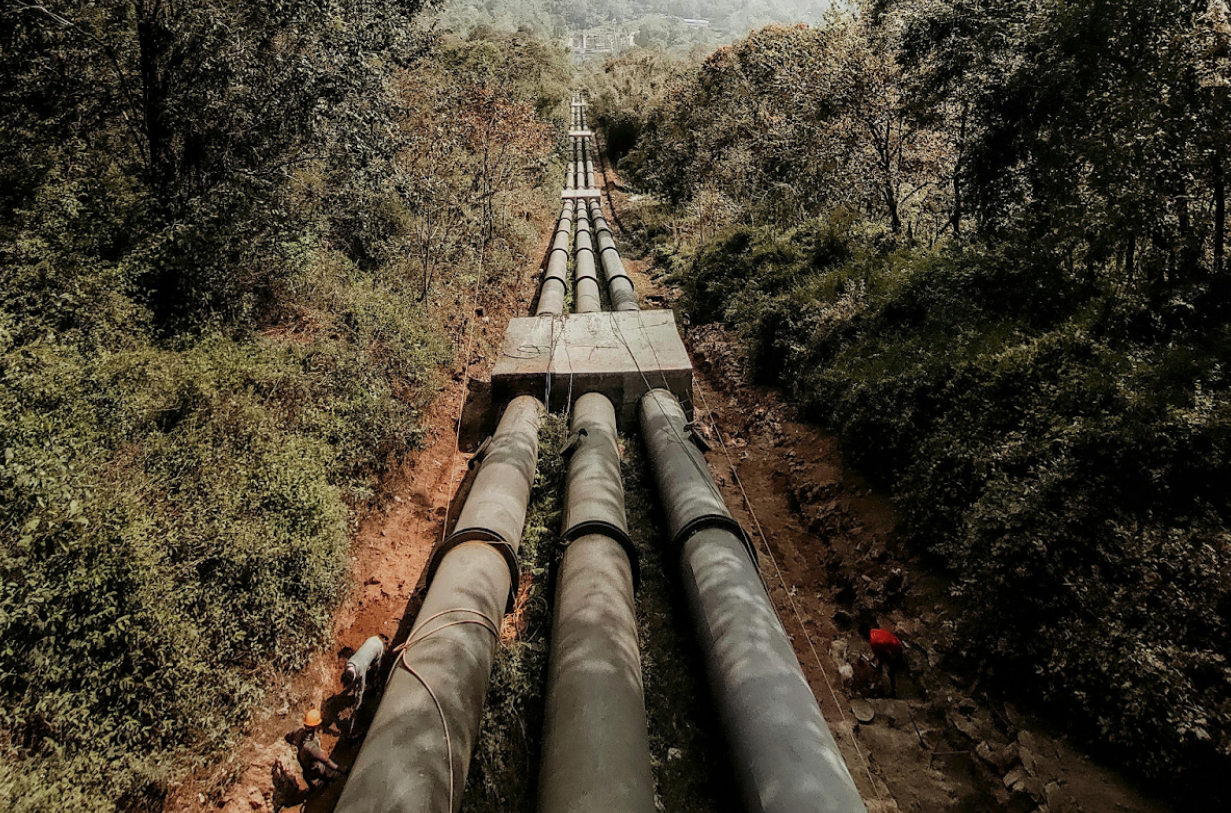
Safety Issues
The integrity of a compromised pipeline not only puts the immediate vicinity at risk, it also endangers the lives of individuals and wildlife that inhabit the surrounding areas. The repercussions of such failures underscore the critical need for rigorous monitoring and maintenance.
Economic Impacts
Besides the direct costs associated with repairing or replacing corroded pipelines, industries face downtime and efficiency losses during these operations, which can further amplify the financial strain. Polyguard's innovative solutions significantly mitigate the economic impacts of underground pipeline corrosion by offering durable protection that safeguards infrastructure and reduces the long-term costs associated with corrosion damage and maintenance. The ripple effect of these costs can be felt across the economy, which can impact the prices and availability of commodities.
Societal and Environmental Impacts
In addition to the immediate disruption caused by pipeline leaks or ruptures, the long-term consequences include diminished trust in infrastructure safety and potential health risks from contaminated resources. The environmental toll, including the loss of biodiversity and long-lasting pollution, emphasizes the importance of sustainable and effective corrosion management strategies.
Industry Standards for Underground Pipeline Corrosion Prevention
The American Petroleum Institute (API) and the National Association of Corrosion Engineers (NACE) set critical benchmarks for the industry that specify best practices for material selection, pipeline design, and operational protocols in order to minimize corrosion risks.
These standards are regularly updated to reflect the latest research and technological advancements in corrosion prevention and ensure that industry practices remain at the cutting edge of effectiveness and safety.
Their guidelines also emphasize the importance of regular inspection and maintenance schedules by advocating for proactive approaches to identify and mitigate potential corrosion issues before they escalate into more significant problems.
Polyguard Solutions for Pipeline Corrosion Protection
Polyguard has a range of products designed to protect underground pipelines from corrosion, including:
RD-6 Coating System
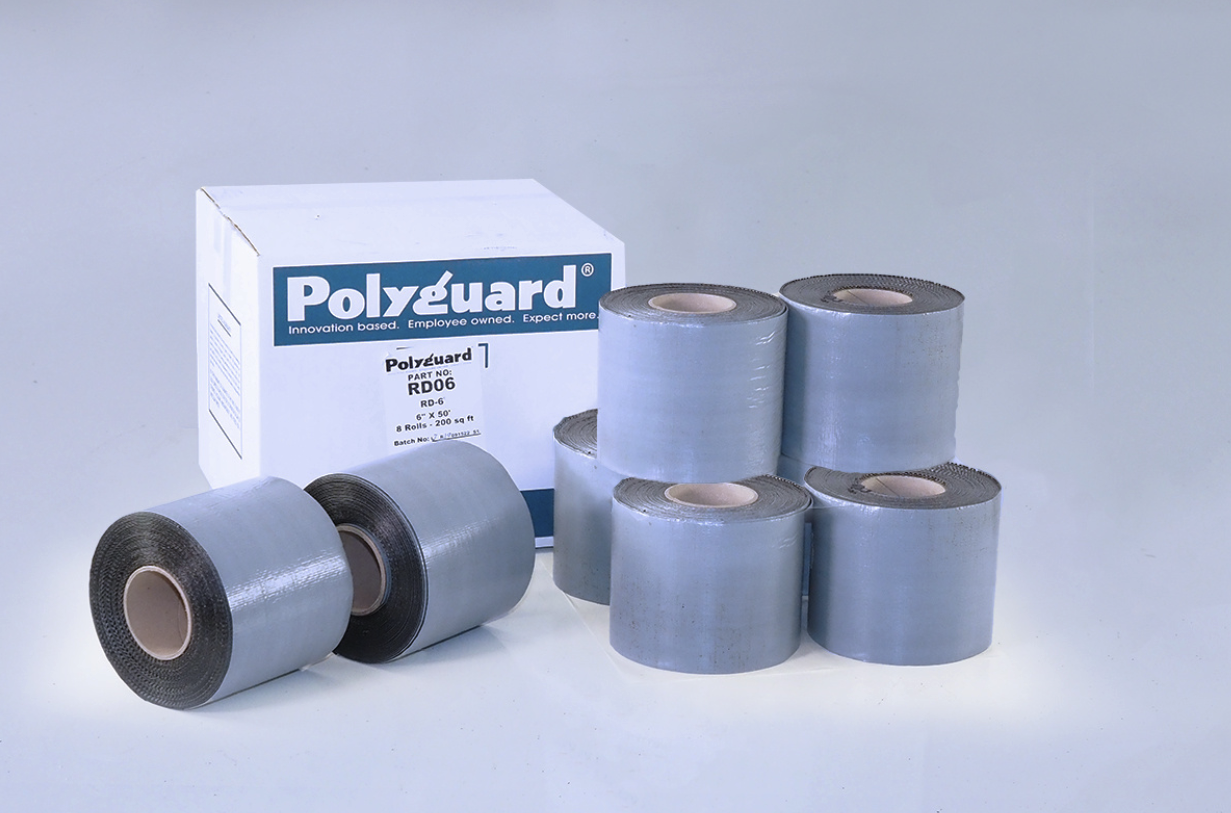
The system is distinguished by its unique, multi-layer composition that is both durable and flexible, and designed to conform to pipeline contours while providing robust protection against several forms of corrosion. Unlike traditional coatings, RD-6 doesn't shield the pipeline from cathodic protection currents so that any areas of minor damage can still receive protection. Its quick application process and compatibility with a variety of pipeline surfaces make it an ideal choice for safeguarding new pipelines as well as rehabilitating older ones.
600 Liquid Adhesive
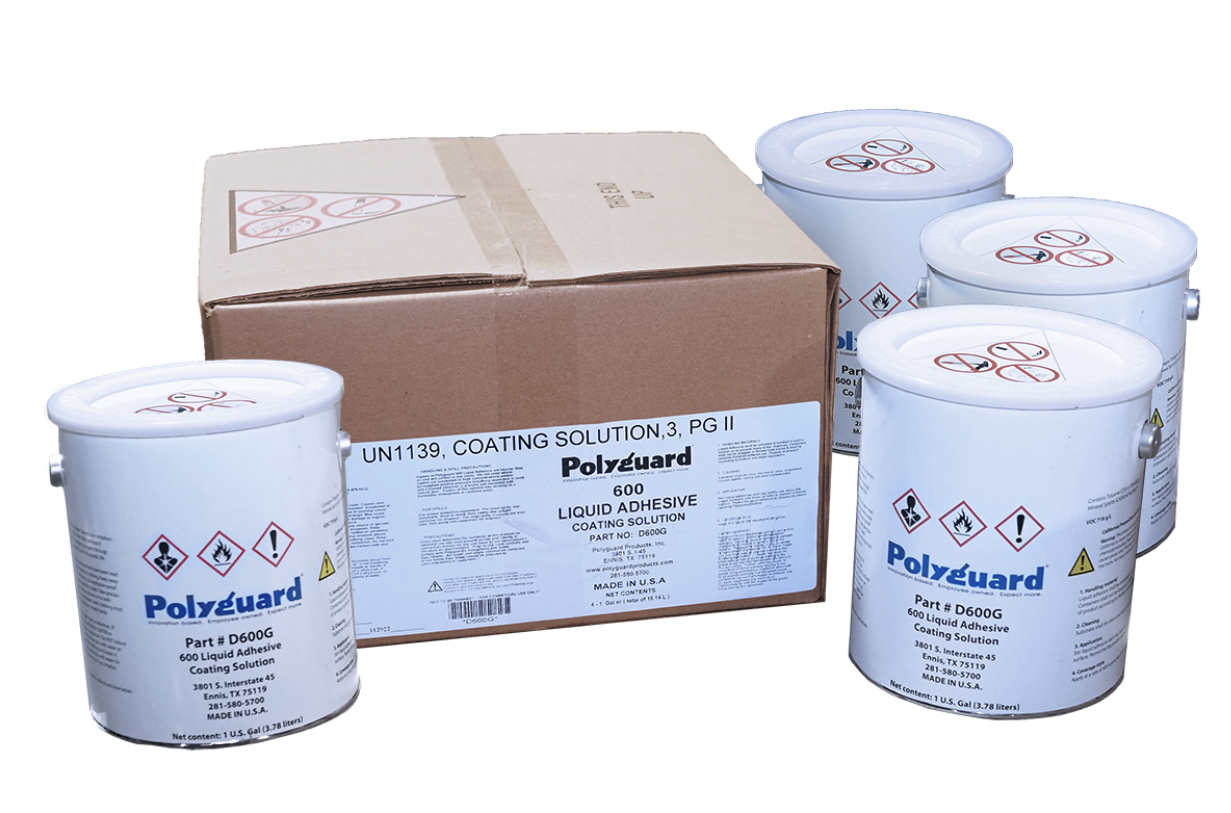
The 600 Liquid Adhesive is specially formulated to enhance the bonding between pipeline surfaces and protective coatings. Its superior adhesive properties ensure a secure and lasting seal to significantly reduce the risk of coating disbondment even under stressful environmental conditions. It is easy to apply and is compatible with a wide range of coatings, which makes it a versatile solution in the arsenal against pipeline corrosion. Its application is a critical step in the process of pipeline protection which helps to ensure that the integrity of the corrosion prevention system is maintained over time.
IRO Outerwrap
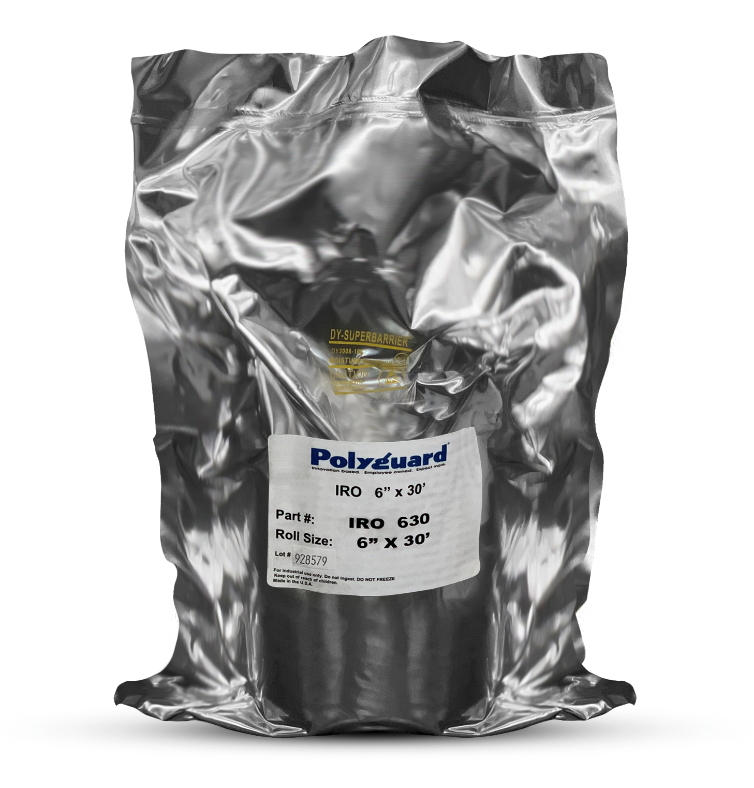
In addition to its range of reactive and proactive solutions, Polyguard IRO Outerwrap stands out as a mechanical protector designed to enhance the durability of pipeline coatings under harsh environmental conditions. Its tough, resilient material acts as a shield against physical impacts and abrasions that could compromise the integrity of underlying corrosion protection layers.
This added layer of security is crucial in extending the lifespan of pipeline installations to ensure that they remain safe and functional for years to come. The ease of application makes it an essential component in the comprehensive strategy to combat underground pipeline corrosion.
CA-9 Mastic
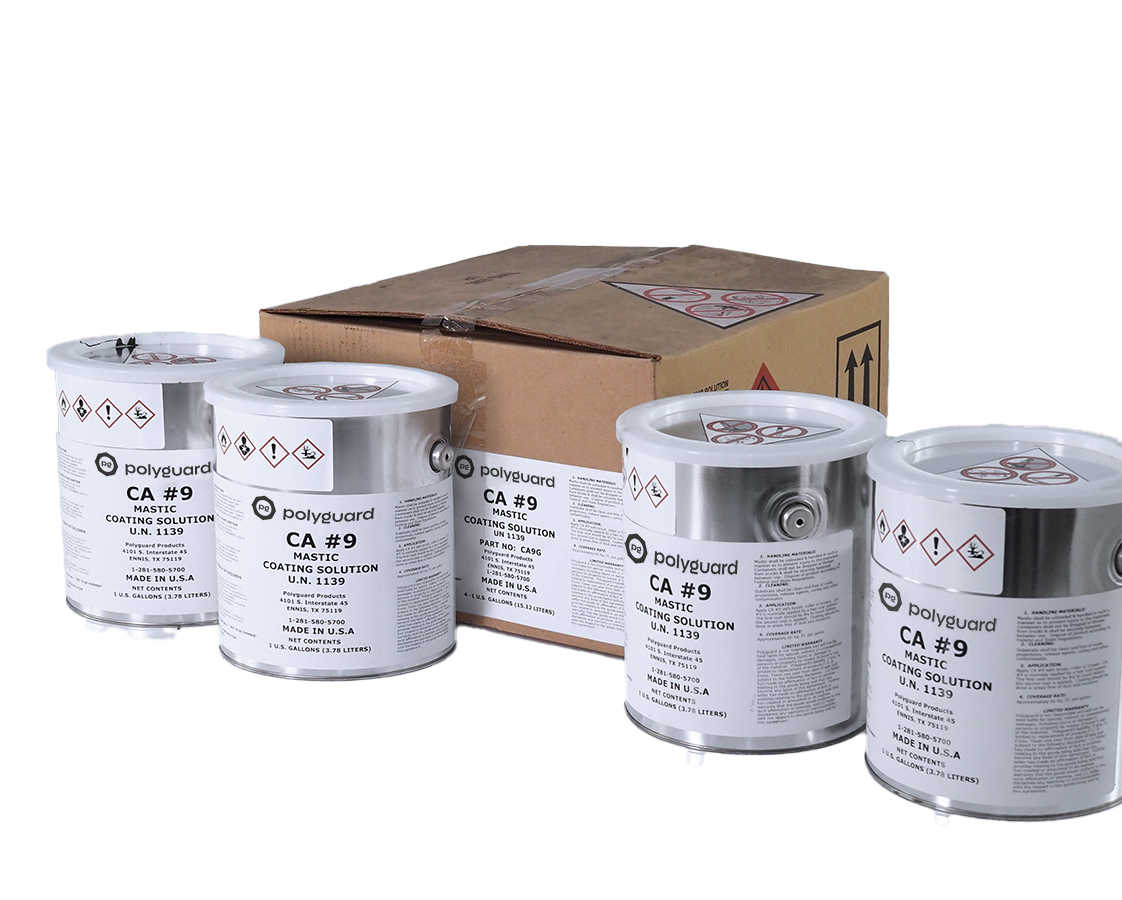
For pipelines that require robust, yet flexible protection against corrosive elements, Polyguard CA-9 Mastic presents a premier solution. CA-9 Mastic is designed to fill voids, seams, and welds in order to create a seamless barrier that defends against moisture ingress and chemical attacks. Its ease of application and superior sealing capabilities make it indispensable for comprehensive corrosion mitigation strategies. The versatility of CA-9 Mastic allows for its use in a wide range of environments for reliable protection under even the most challenging conditions.
NHT-5600
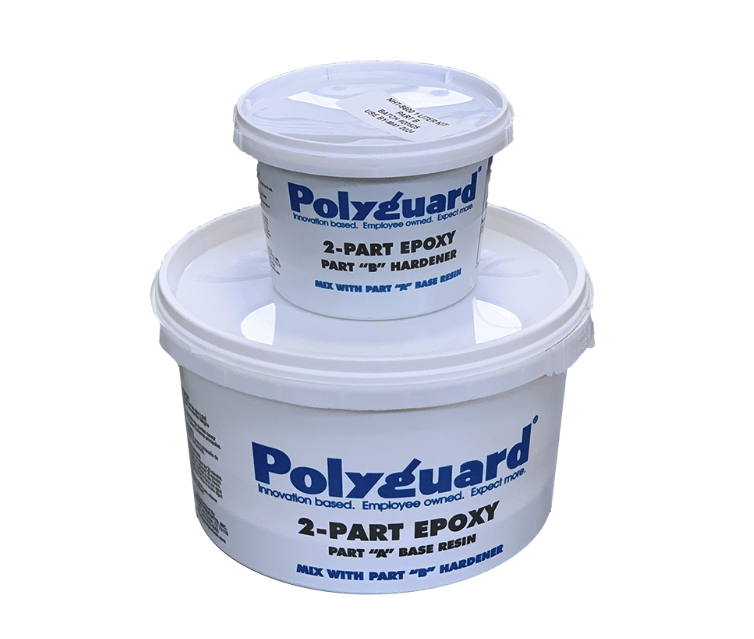
NHT-5600 is Polyguard's innovative answer to the toughest corrosion challenges faced by underground pipelines. NHT-5600 is an advanced coating solution that has been engineered for high-performance corrosion resistance for a robust defense against environmental aggressors and mechanical stressors alike. Its formulation is designed for ease of application to ensure a durable bond and long-lasting protection for critical infrastructure.
By integrating these products into pipeline protection strategies, operators can significantly enhance the longevity and reliability of their infrastructure.
Innovative Approaches to Corrosion Protection
The continuous evolution of corrosion protection technologies reflects the industry's commitment to safeguarding infrastructure. Advanced materials, smarter monitoring systems, and improved coating technologies are at the forefront of the battle against corrosion with new layers of defense and peace of mind for pipeline operators.
Polyguard: The First Line of Defense Against Pipeline Corrosion
We must use the latest and most reliable methods to protect our underground pipelines from corrosion. Polyguard's advanced solutions provide top-notch protection to help keep your pipeline infrastructure safe, efficient, and sustainable.
Contact us today and speak with one of our experts!