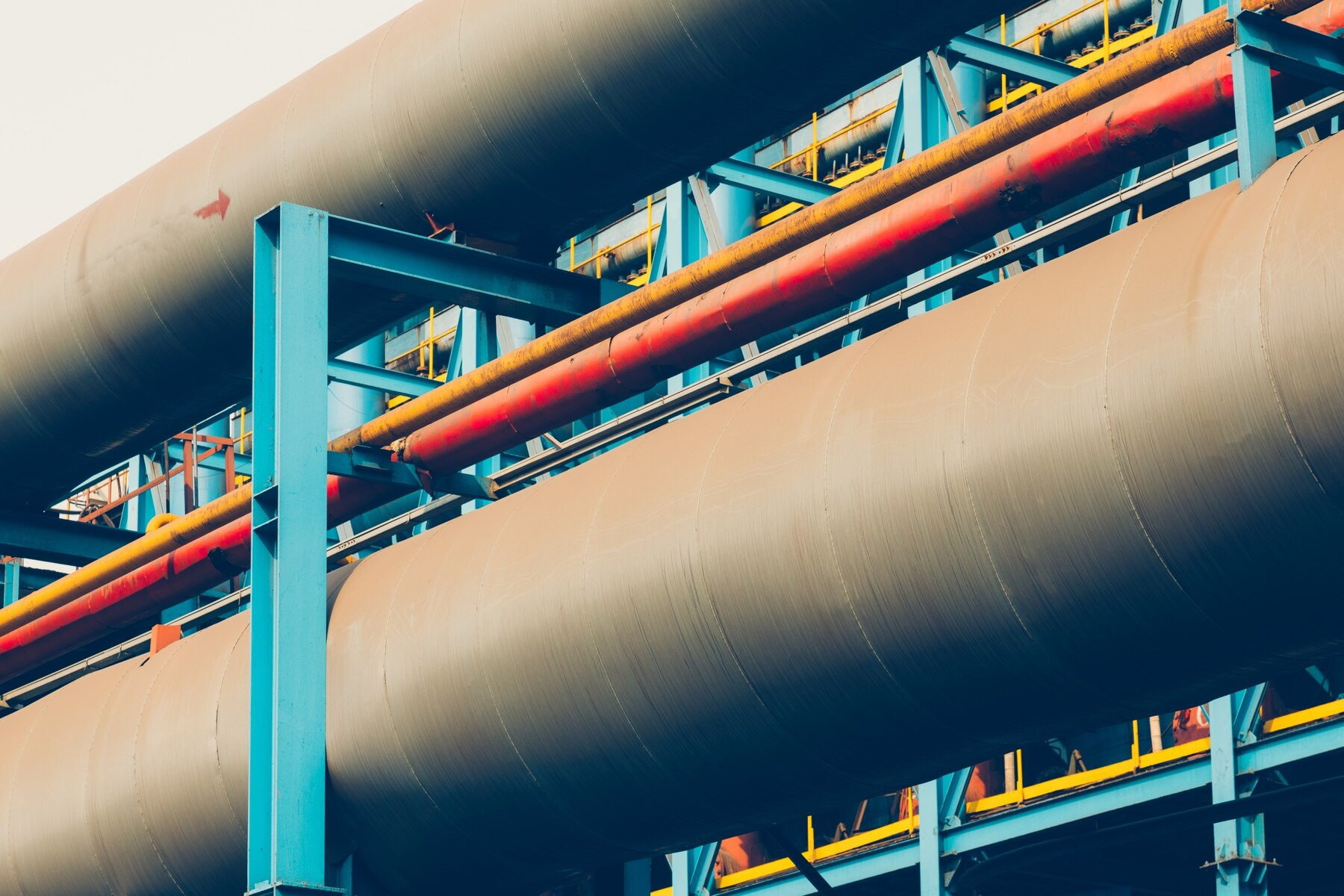
Pipeline coatings are key to protecting pipelines, which are essential for transporting energy and materials. This guide explains the different types of pipeline coating, how they're applied, and the standards they meet. It highlights how crucial these coatings are in preventing corrosion and keeping pipelines working smoothly.
The Essentials of Pipeline Coating Technology
Pipeline coatings serve a critical role by acting as a protective shield for both the internal and external surfaces of pipes. Pipeline coatings are pivotal in safeguarding the pipe from corrosion and environmental wear by ensuring they remain operational under various harsh conditions. Their application is key to preserving the pipe's structural integrity and ensuring its functional longevity.
Types of Pipeline Coatings
The selection of a pipeline coating depends on the environmental conditions, the material transported, and the service life required. Common types include:
- Fusion-Bonded Epoxy (FBE): A thermoset polymer coating that provides excellent adhesion and protection against chemical and physical degradation.
- Polyurethane Coatings: Known for their flexibility, abrasion resistance, and impact resistance, they are suitable for varying temperatures and terrains.
- Zinc Coatings: Zinc coatings react with the underlying steel to safeguard it from rust.
Detailed Overview of Key Pipeline Coatings
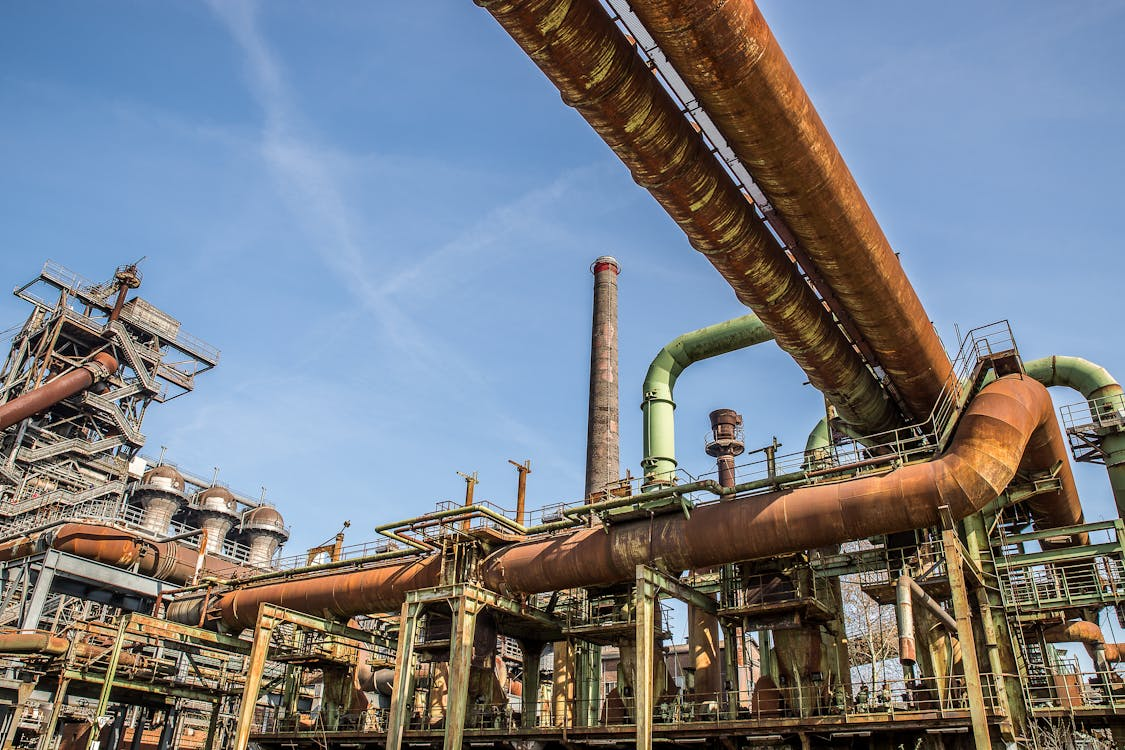
Fusion-Bonded Epoxy (FBE) Coating
FBE is a robust, thermoset polymer coating that is known for its strong adhesion and resistance to chemical and physical degradation. It's applied in a powder form and cures under heat to form a protective layer, which is ideal for environments that require high durability and corrosion resistance.
Three-Layer Polyethylene/Propylene (3LPE/3LPP) Coating
3LPE/3LPP coatings consist of three layers: a high-performance FBE base, a copolymer adhesive, and a top layer of polyethylene/propylene. These coatings are lauded for their excellent corrosion resistance, mechanical protection, and ability to withstand various environmental conditions.
Coal Tar Enamel (CTE) Coating
CTE is a thermoplastic coating that has been used for decades due to its low cost and effective protection against corrosion. It involves applying multiple layers, including a primer, the coal tar enamel, and glass fiber wraps, that provide a durable barrier against external elements.
Geotextile-Backed Non-Shielding Anti-Corrosion Coatings
Polyguard's innovative approach to pipeline coatings is embodied in their geotextile-backed non-shielding anti-corrosion coatings, such as the RD-6® and RD-6 HT® systems. These products represent a significant advancement in pipeline protection technology, and are designed to address the rigorous demands of buried and submerged pipeline environments.
Comparative Analysis of Coating Systems
In protecting pipelines, it's crucial to choose the best coating system for long-lasting durability, efficiency, and being eco-friendly. Comparing Fusion-Bonded Epoxy (FBE), Three-Layer Polyethylene/Propylene (3LPE/3LPP), Coal Tar Enamel (CTE), and Polyguard's Geotextile-Backed Non-Shielding Anti-Corrosion Coatings highlights a range of options. Each offers unique advantages and uses.
Fusion-Bonded Epoxy (FBE) Coating
FBE coatings stand out for their strong adhesion and excellent chemical resistance, which makes them suitable for harsh environments. They provide a solid, impermeable barrier that prevents corrosion and withstands high temperatures.
Three-Layer Polyethylene/Propylene (3LPE/3LPP) Coating
3LPE/3LPP systems offer superior mechanical protection and are renowned for their ability to resist environmental challenges. These coatings combine the toughness of FBE with the flexibility and impact resistance of polyethylene or polypropylene layers to provide comprehensive protection against corrosion.
Coal Tar Enamel (CTE) Coating
CTE is known for its cost-effectiveness and long history of providing reliable corrosion protection. This system uses multiple layers, including a primer and glass fiber wraps, to create a robust barrier against environmental and chemical aggressors.
Geotextile-Backed Non-Shielding Anti-Corrosion Coatings
Polyguard RD-6® and RD-6 HT® coatings are distinct in their approach that offers a geotextile-backed, non-shielding system that provides strong adhesion, high breaking strength, and low elongation. These coating systems are particularly effective in mitigating soil stress and accommodating the thermal dynamics of pipelines, which makes them suitable for high-temperature applications and ensuring long-term corrosion protection.
When choosing the best coating system, it's important to look at factors such as how well it can handle the temperature, impacts, penetration, soil stress, its environmental impact, and the specific needs of the pipeline project. Each type of coating has its own advantages, and the choice usually depends on the particular conditions of the pipeline's surroundings and how long and how well you want it protected.
Pipeline Coating Standards: Ensuring Excellence and Innovation
Pipeline coating standards, such as ISO 21809, API RP 5L2, and NACE specifications, set the benchmark for quality and durability in the industry. These guidelines dictate the materials, application processes, and testing methods to ensure coatings meet safety and performance criteria. In real-world applications, compliance with these standards is critical for maintaining pipeline integrity and operational efficiency.
They drive innovation, pushing manufacturers to develop advanced coating technologies that not only adhere to stringent requirements, but also offer enhanced protection against corrosion and environmental wear. This constant evolution in coating technology helps the industry tackle new challenges to help ensure that pipelines are safer and more reliable.
Pipeline Coating Procedures
The procedure for applying pipeline coatings involves multiple steps:
1. Surface Preparation: Clean and profile the pipe surface to ensure coating adhesion.
2. Application: Techniques vary from spray application to electrostatic methods, depending on the coating type.
3. Curing: Make sure that the coating has properly adhered and set in order to form a durable protective layer.
Pipeline Construction and Coating Integration
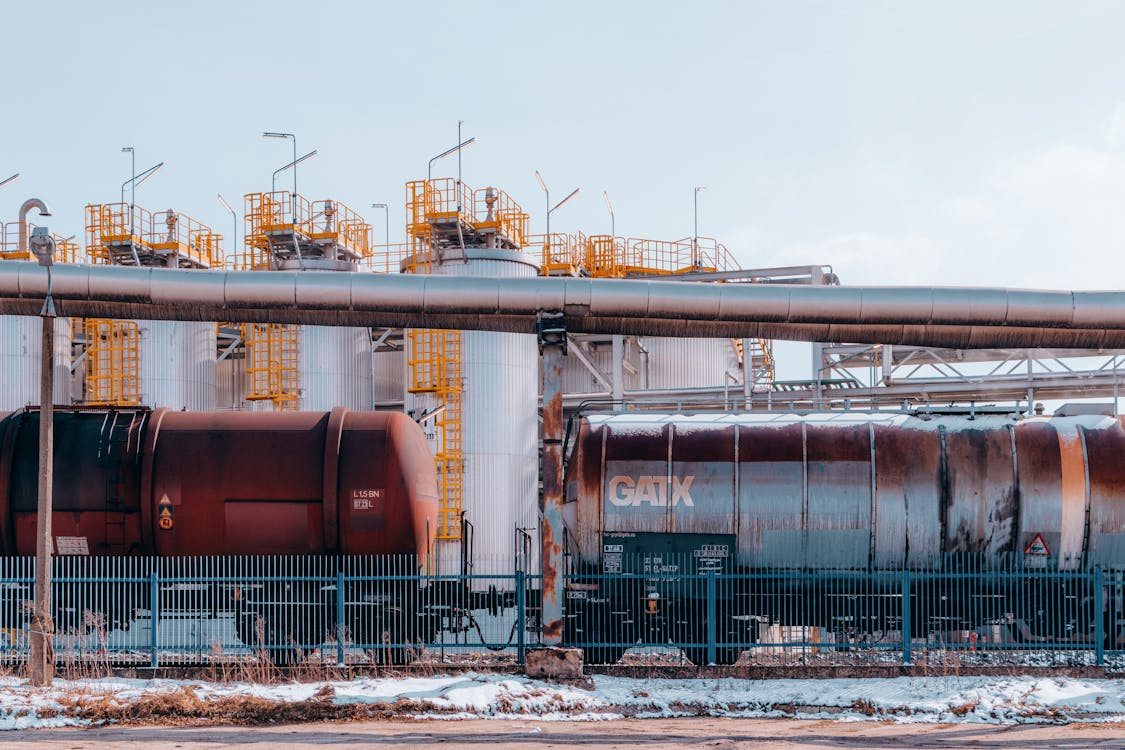
In pipeline construction, it's crucial to include coating processes to make sure pipelines last longer and are more durable. It isn't just about putting on a protective layer. It involves carefully planned steps during construction to make the coating work best and improve the pipeline's performance overall.
Timing and Application
Coating application should be timed to coincide with specific construction phases to avoid environmental or mechanical damage. For example, coatings should be applied after the pipeline has been welded and tested for defects, but before it is buried. This sequence minimizes the risk of coating damage during trenching and backfilling operations.
Environmental Considerations
The environmental conditions under which coatings are applied can significantly affect their adhesion and curing processes. Optimal conditions such as temperature, humidity, and cleanliness must be maintained to ensure the coating adheres properly to the pipeline surface and cures effectively. For instance, applying coatings during extreme temperatures or high humidity levels can compromise their protective properties.
Coating Selection and Compatibility
Choosing the right coating involves considering the pipeline's operational environment, the transported material, and the expected lifespan. The coating material must be compatible with the pipeline's substrate and the external conditions to prevent failures like coating delamination or corrosion under insulation (CUI).
Quality Control and Inspection
Quality control measures and regular inspections are critical during the coating application process. Techniques such as holiday detection are employed to identify and rectify any discontinuities or defects in the coating to help ensure a continuous protective barrier.
By carefully managing these factors, using coating processes in pipeline construction improves the coatings' protective features, which greatly helps the pipeline's integrity and efficiency. This thoughtful approach is key to preventing corrosion and lengthening the pipeline's lifespan.
Reducing Corrosion with Pipeline Coatings
Pipeline coatings are the first line of defense against corrosion, a major cause of pipeline deterioration. By providing a barrier between the pipe material and corrosive elements, coatings can significantly extend the operational life of pipelines.
Polyguard’s Pipeline Products
Polyguard specializes in innovative pipeline coating solutions that are designed to meet industry needs. With a focus on research and development, Polyguard offers coatings that ensure durability, efficiency, and protection against harsh environmental factors.
RD-6® Coating System
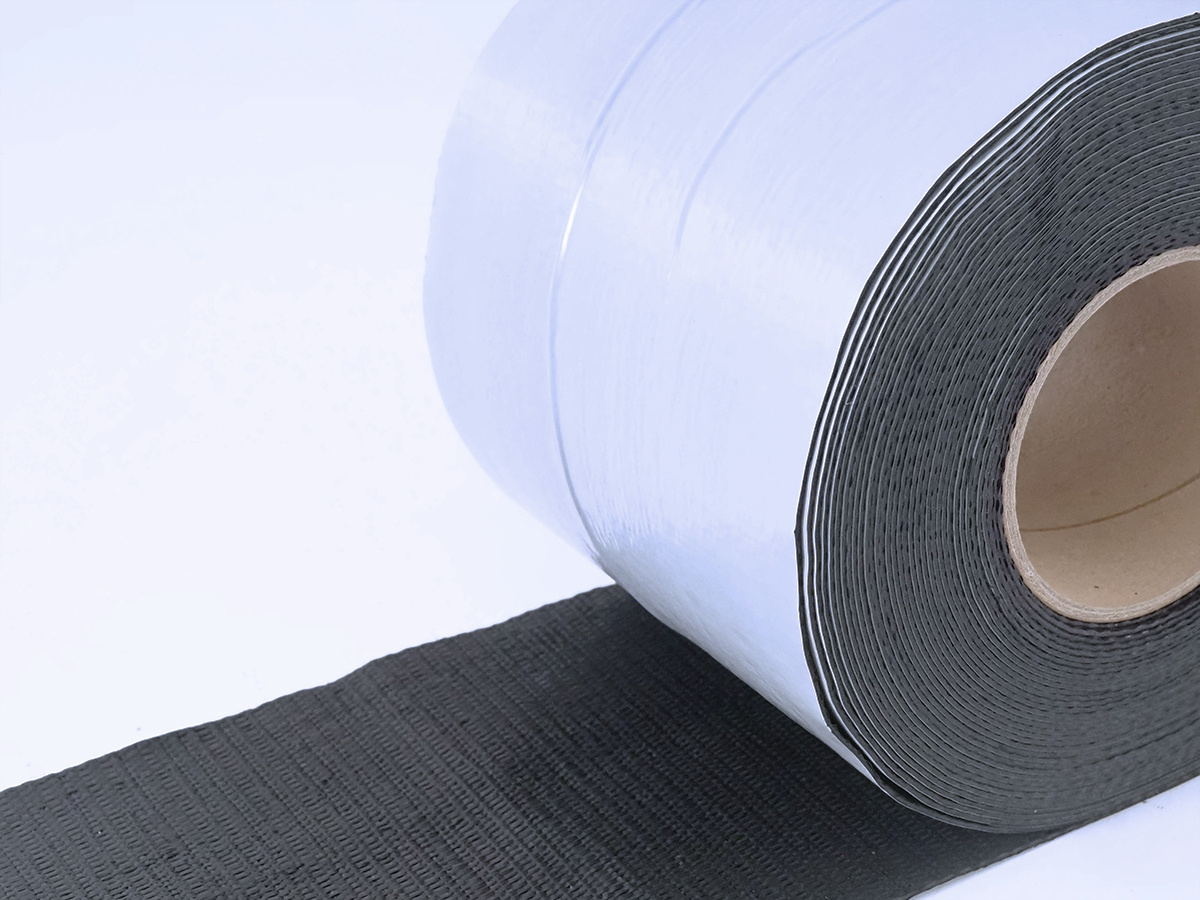
- Has non-shielding, anti-corrosion wrap for buried and submerged pipelines
- Accommodates thermal expansion and contraction
- Has an application with Polyguard approved equipment
- Is suitable for a wide range of environmental conditions
RD-6® UVO Overcoat
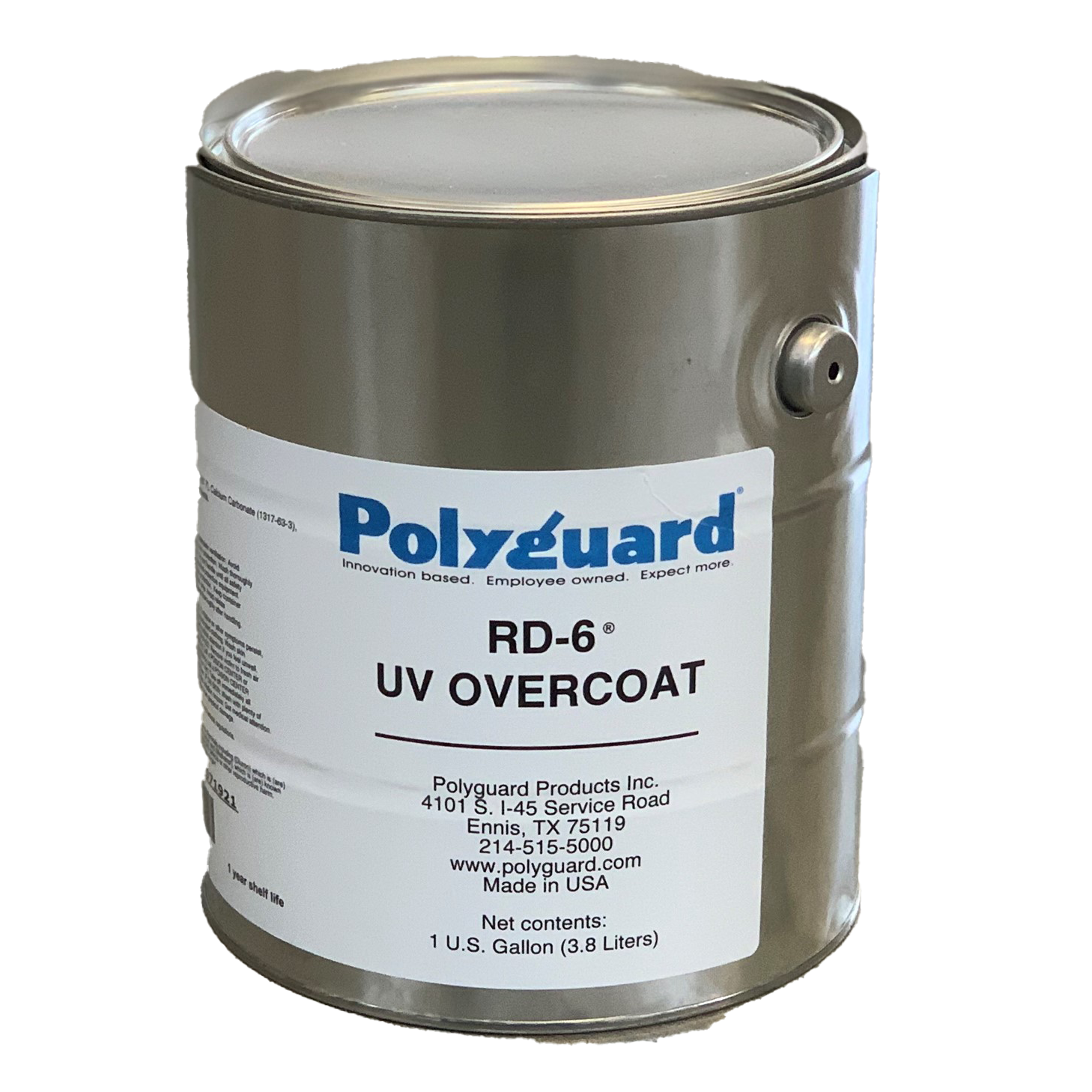
- Provides UV protection for above-ground pipeline sections
- Enhances the longevity of the underlying RD-6® coating
- Is quick and easy to apply, and complements the primary coating system
CA-9™ Mastic
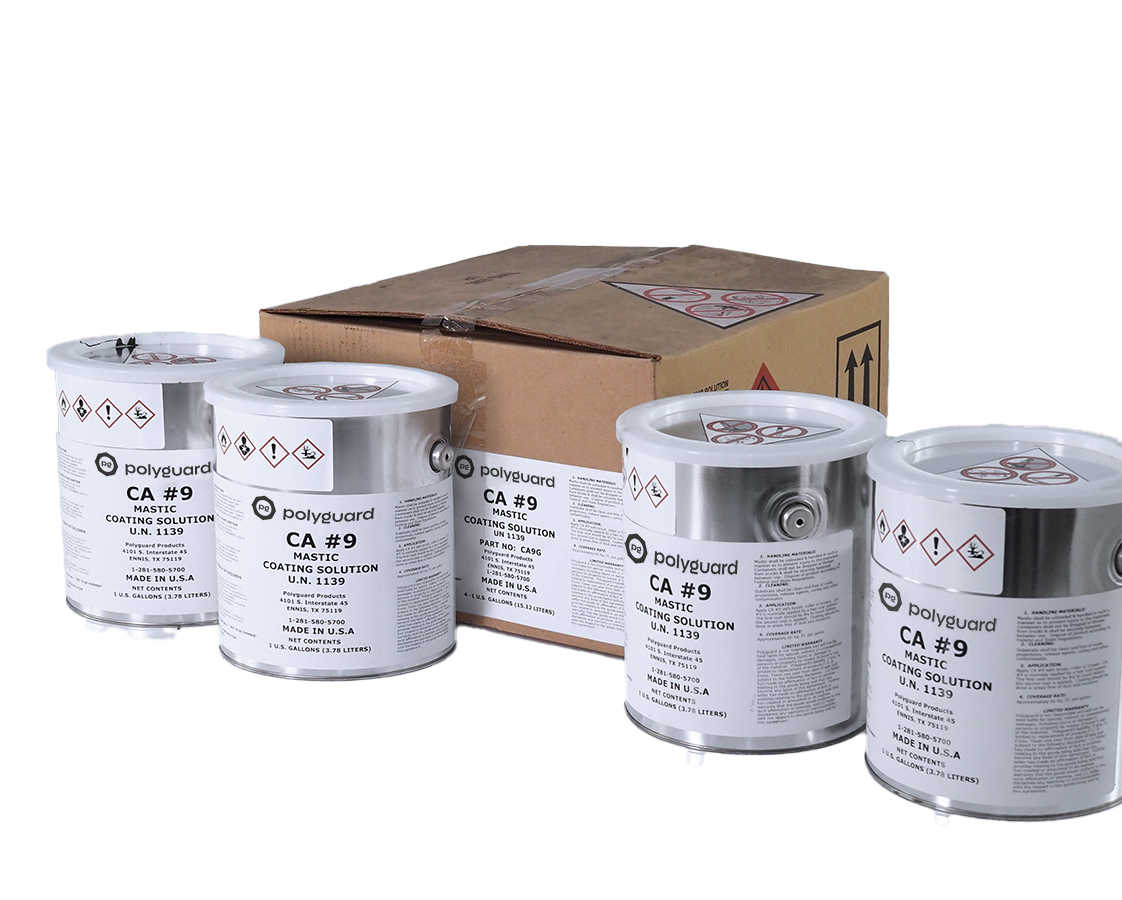
- Water-resistant for effective moisture exclusion
- Ideal for sealing joints and cracks against corrosion
- Durable across various environmental conditions
606 Filler Compound
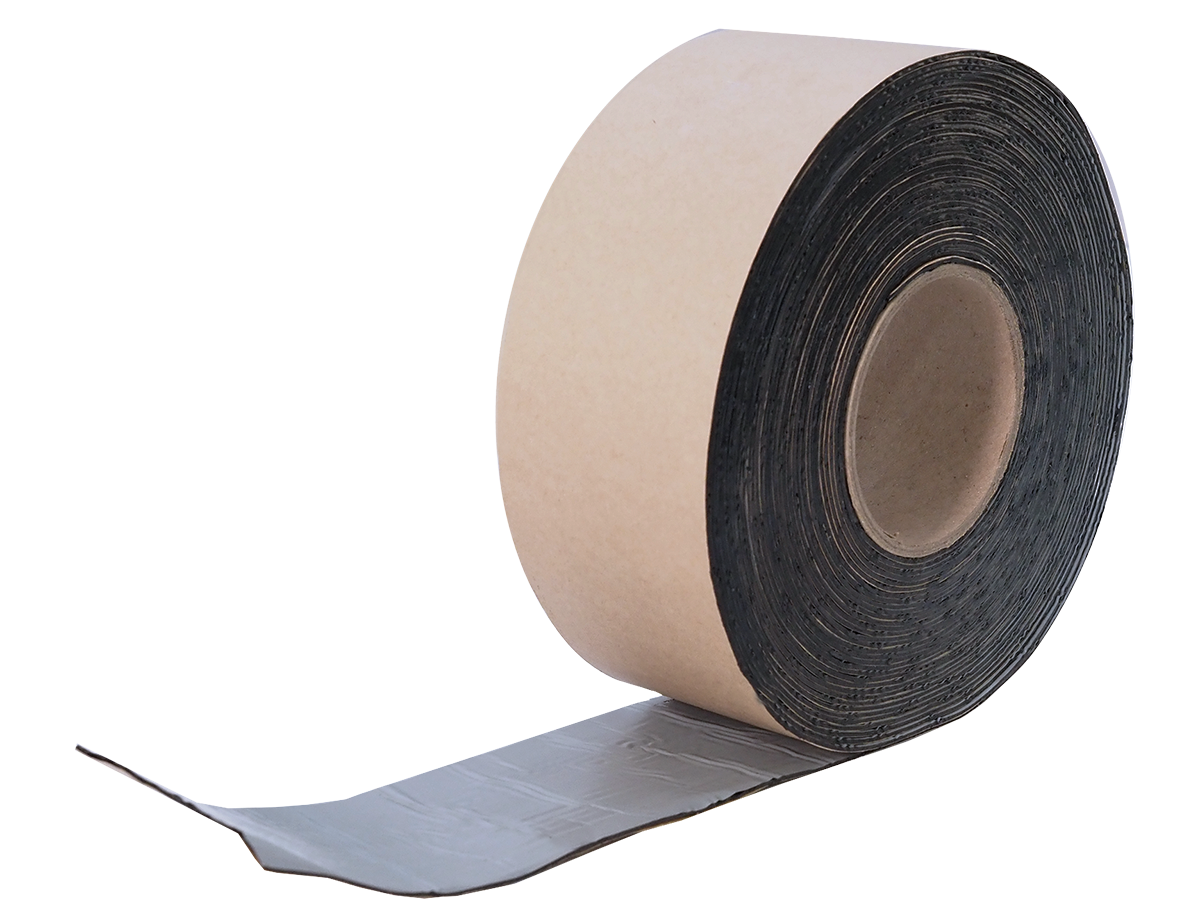
- Ensures smooth surface preparation for coating application
- Is compatible with other Polyguard coating products
- Fills voids and irregularities effectively
Maximize Pipeline Integrity with Polyguard's Innovative Coating Systems
Polyguard's advanced pipeline coating systems, developed through years of research and technological innovation, meet the modern pipeline industry's needs. Our systems do more than just prevent corrosion; they provide a complete protective solution that maintains the structural integrity, efficiency, and durability of pipelines.
Contact us today and find out why we're the top choice for pipeline coating systems!