Pipeline corrosion prevention aims to protect the world’s extensive network of buried pipelines. Without corrosion protection, pipes can lose their integrity, lowering mechanical strength through the development of exterior cracks and holes, which can lead to failures. A corrosion prevention coating system must resist degradation over time and conduct cathodic protection currents should the coating fail or disbond; both are features of long-lasting RD-6® COATING SYSTEMS.
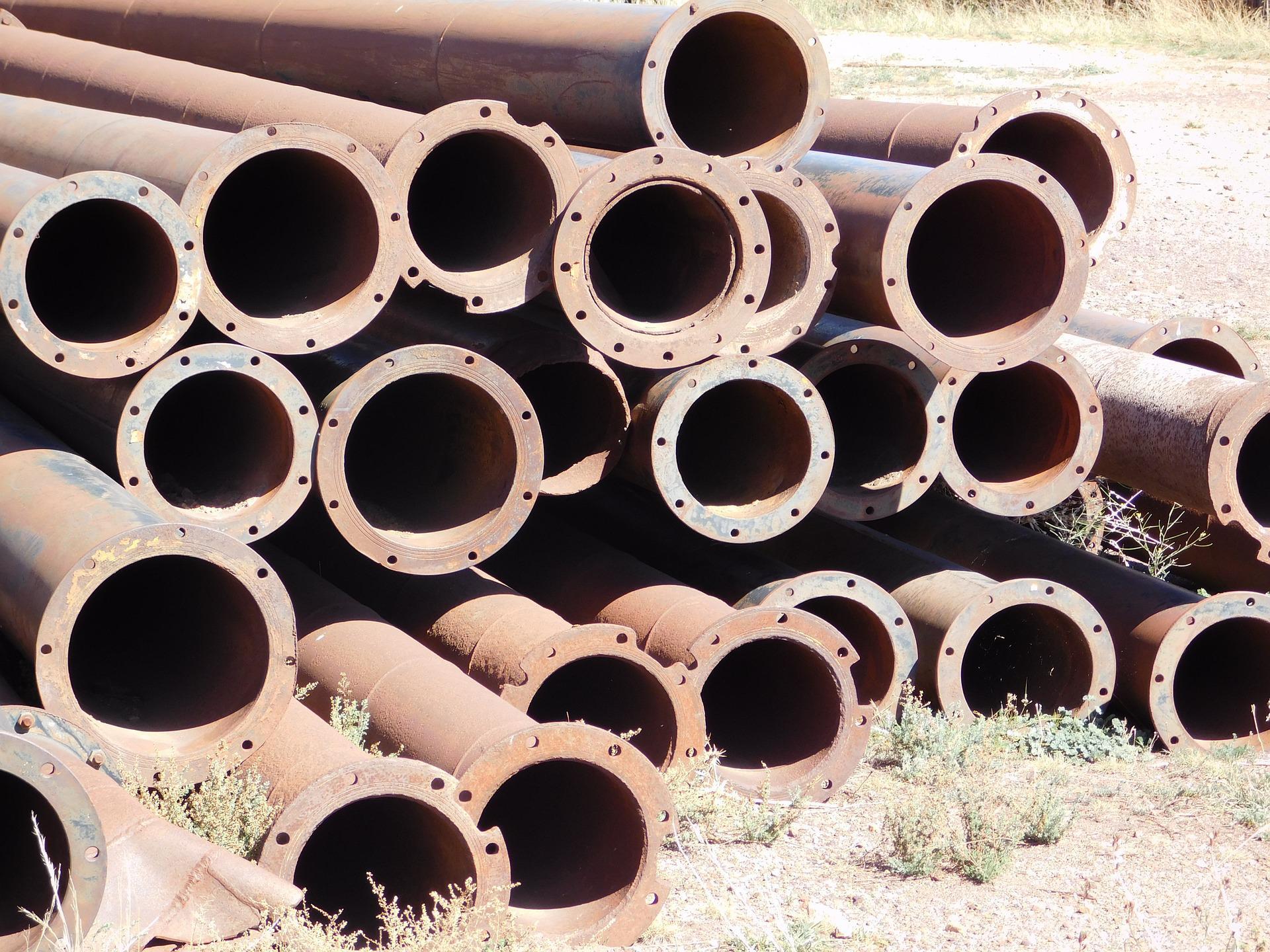
What is Pipeline Corrosion?
Pipe corrosion occurs when water (a corrosive electrolyte) combines with oxygen on two metal pipe surfaces, which triggers an electrochemical process or electrical connection between the metal areas. Corrosion requires four elements, anode, cathode, metallic path, and electrolyte to occur. The first three elements are typically present and the addition of the electrolyte from the environment completes the corrosion cell. Higher temperatures, salts and acids are some common additions that will accelerate corrosion.
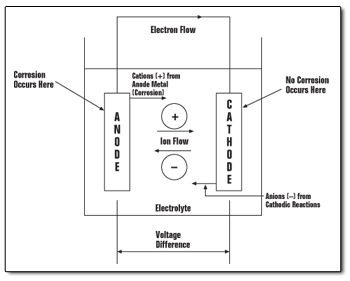
- During the electrochemical process, the metal surface more prone to corrosion (less noble) forms an anode. The anode loses electrons (forming a cation), causing the spot to oxidize (corrode), and produce rust (red iron oxide).
- The more corrosive or oxidation-resistant metal surface (nobler) forms a cathode. The cathode acquires electrons (forming an anion) that slows corrosion.
Corrosion can significantly affect the reliability and longevity of pipelines used to transport everything from natural gas, liquid petroleum, biofuels, water, sewage, etc. Corrosion costs an estimated $7 billion annually to monitor, replace, and maintain gas and liquid transmission pipelines – and the operation and maintenance represents 80 percent of the cost.
Types of Pipeline Corrosion
Pipeline corrosion can occur for many reasons, leading to various corrosion types, each requiring specific protection methods and considerations to ensure the pipeline’s integrity.
- Uniform pipe corrosion causes a consistent loss of material along the pipe’s surface, leading to a continuous thinning of the solid structure. You can prevent uniform pipe corrosion by selecting a suitable piping material and combining corrosion protection methods like surface coatings and cathodic protection.
- Selective leaching (graphitic corrosion) occurs when a noble metal and a more reactive element form an alloy, which results in the loss of the reactive component from the pipe’s surface, diminishing the pipe’s strength. Adding tin or aluminum can help protect against leaching.
- Galvanic corrosion occurs when dissimilar metals of different corrosion resistance electrically connect, causing the metalworking as an anode to deteriorate. To stop galvanic corrosion, place insulation between the two metals and use a combination of metals close in the galvanic series. In addition, coat the cathodic surface.
- Pitting corrosion produces severe, localized deterioration on a limited surface area, causing pits and punctures on a pipe’s surface. Surface and pipe material defects, mechanical damage to the protective coating, and penetration by aggressive chemical species, like chlorides, can lead to pitting corrosion. To prevent pitting corrosion, select the pipe material for the service environment, considering the chemical concentration of a reactant (pitting resistance) and temperature, and include cathodic and anodic protection with sufficient coating to withstand the environment..
- Crevice corrosion occurs when oxygen-starved surfaces of a pipe’s joints or crevices become the anode in an electrochemical reaction. Replacing riveted joints with welded joints can help overcome such problems. Areas with step downs or reductions in wall thickness can present areas of concern for crevice corrosion and require attention when applying the anticorrosion coating.
- The flow of stray currents both AC and DC through pipelines can cause stray current corrosion, which can lead to localized pitting and pinholes on metal surfaces at the exact points where stray currents exit the surface. Stray currents can come from electric railways, cathodic protection, electric welding machines, high overhead voltage, or buried lines. You can reduce stray current corrosion by controlling electricity leakages through bonds to other structures or bypassing stray current to an earthing station.
- Intergranular deterioration: Grains make up the microstructure of metals and alloys, separated by grain boundaries. Intergranular corrosion happens along the grain boundaries or immediately adjacent to grain boundaries. Typically, impurities (chemicals) that precipitate on the grain boundaries reduce the area’s corrosion resistance. Selecting extra-low carbon stainless steel materials can help prevent intergranular deterioration.
- Cavitation and Erosion Corrosion in a pipeline occurs when the fluid’s working pressure drops below its vapor pressure, which causes vapor pockets and vapor bubbles to form, collapsing the pipeline’s internal surface, and leading to erosion-corrosion. Areas of a pipeline particularly prone to erosion-corrosion include the discharge pipes, pump suctions, elbows, tees, expansions, or fitments at heat exchangers and valve seats.
- Stress Corrosion Cracking results from pre-existing cracks’ growth, leading to the metal pipes’ failure that exceeds threshold stress levels under tensile stress, especially at higher temperatures. To prevent stress corrosion cracking, keep loads below the threshold stress levels.
Preventing Pipeline Corrosion
Corrosion prevention must consider both external and internal surface corrosion. External surface corrosion on a steel pipe occurs due to environmental conditions that lead to an electrochemical interaction between the pipeline’s exterior and the surrounding water, soil, and air. Internal pipeline corrosion happens when chemicals from the products transported in the pipes, including water, carbon dioxide, and hydrogen sulfide, attack a steel pipe’s interior surface.
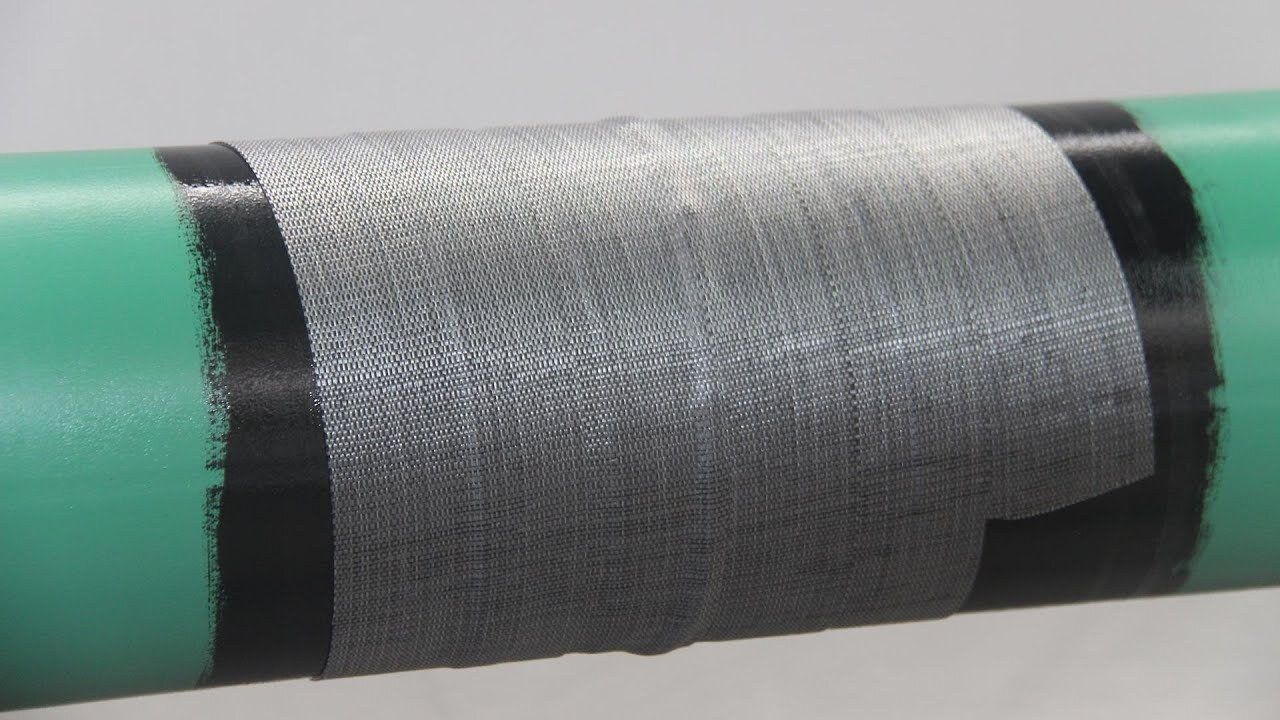
Stopping External Pipeline Corrosion
After you've determined the proper pipeline leak detection technique, the first line of defense in preventing external pipeline corrosion typically involves removing one of the four elements needed for corrosion – anode, cathodes, the metallic path, and electrolyte. A quality coating system can help protect the pipeline from the surrounding electrolyte (often water) by acting as a barrier thereby breaking the corrosion cycle. Some barrier coatings also use inhibitive or sacrificial pigments, causing passivation or a sacrificial anode to form defects in the coating.
In addition, applying cathodic protection will protect the pipeline if the coating becomes damaged, increasing corrosion at the defect. Cathodic protection currents mitigate corrosion by supplying electrical current (free electrons) from an alternate source that changes the anodic (active) sites on the metal surface to cathodic (passive) sites.
Pipeline Corrosion Prevention with the
POLYGUARD RD-6® COATING SYSTEM
The RD-6® COATING SYSTEM is a superior, non-shielding, external, anti-corrosion system for buried and submerged pipelines, used on new construction girth welds and long line rehabilitation and for integrity assessment inspections, for pipelines operating at temperatures not exceeding 145°F (63°C). RD-6® HT is available for pipelines operating up to 190°F (88°C).
Our RD-6® coating system can also be used above ground. In these applications, to protect from harmful UV rays Polyguard recommends using our RD-6® UV Overcoat for extra sun protection.

The Polyguard RD-6® coating system includes a strong, tightly woven, polypropylene geotextile fabric that bonds to the coating’s outside surface, to provide non-shielding properties plus high breaking strength and low elongation. In addition, the woven geotextile polypropylene backing allows for compression and tension during RD-6® application to ensure proper long-term performance.
We also strongly recommend applying POLYGUARD SP-6™ OUTERWRAP over the RD-6 COATING for pipe diameters greater than 4-inches. The outer wrap provides an inexpensive, non-shielding layer, further reducing damage from soil stress.
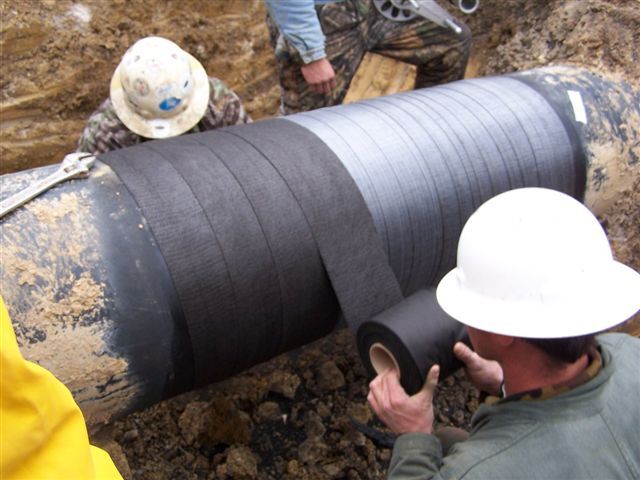
Benefits of Non-Shielding RD-6® COATING SYSTEM
RD-6® Allows for Corrosion Protection Currents
The non-shielding design of the RD-6® COATING SYSTEM allows for the passage of corrosion protection currents due to the geotextile backing’s open weave. If the coating is damaged or compromised the cathodic protection current will not be blocked from protecting the steel substrate. Evidence of adequate cathodic protection in these areas can be inferred if the pH of the electrolyte at the failure is at a level of 9 or higher.
Long-Lasting Durable RD-6®
Soil-stress-resistant RD-6® minimizes disbondment from the pipe, even with less than perfect surface preparation.
Easy to Apply POLYGUARD RD-6® COATING SYSTEM
Polyguard manufactures RD-6® coating in rolls for easy application using a Polyguard-approved machine such as the Wrapster or power-operated machine. The design of the Polyguard Wrapster includes two spindles: one provides tension during the application of the RD-6® coating to the pipe. The other spool releases the liner during the application. However, you can apply RD-6® manually without the Wrapster, as long as you adequately apply tension consistently during the application.
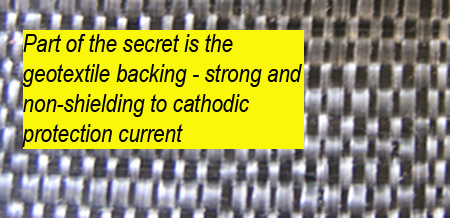
MINOLTA DIGITAL CAMERA
In addition, quick to apply RD-6® does not require curing. It includes a silicone-coated release liner to stop the layers from adhering to one another and help in the application process.
Pipeline Corrosion Prevention with the
POLYGUARD RD-6® COATING SYSTEM
The reliable and proven POLYGUARD RD-6® COATING SYSTEM has protected thousands of pipelines from external corrosion and stress corrosion cracking for over thirty years. Non-shielding RD-6® COATING SYSTEM is an excellent, long-lasting pipeline corrosion prevention that allows for cathodic protection currents in the event of disbondment.
Don’t hesitate to contact the Polyguard professionals today for more on pipeline corrosion prevention.