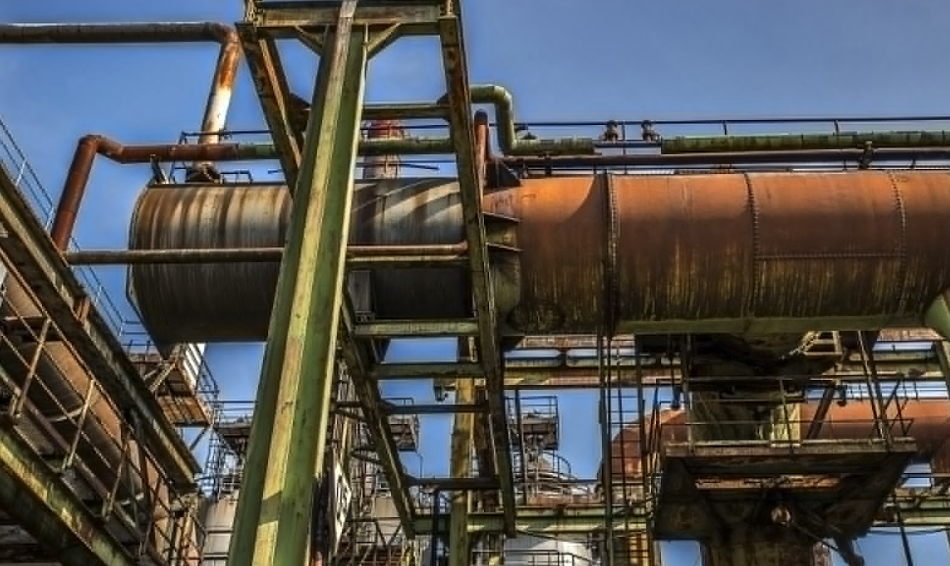
Ensuring the longevity and efficiency of oil and gas pipelines is vital for the success and environmental responsibility of the energy sector. Corrosion, a persistent threat to pipeline integrity, can result in significant operational hurdles, environmental hazards, and financial setbacks.
Polyguard's innovative solutions are pivotal in addressing these challenges, and they provide cutting-edge corrosion control and prevention technologies that lead the industry in best practices.
Understanding Corrosion in Oil and Gas Pipelines
Corrosion in pipelines for oil and gas is a chemical or electrochemical reaction between the pipeline material and its environment that leads to material degradation and loss.
This process can significantly impact oil, gas, and natural gas pipelines by threatening safety, reliability, and the continuity of operations.
The implications of unchecked corrosion are far-reaching, including the potential for leaks, ruptures, and catastrophic failures that compromise environmental safety and incur steep remediation costs.
Types of Corrosion Encountered
Two primary forms of corrosion affect pipelines: internal and external. Internal corrosion occurs from the inside due to the corrosive nature of the transported fluid, which can contain water, carbon dioxide, hydrogen sulfide, and other corrosive agents. External corrosion arises from environmental factors such as soil composition, moisture, and temperature fluctuations surrounding the pipeline.
In addition to internal and external corrosion, pipelines can suffer from microbiologically induced corrosion (MIC), where bacteria produce acids that accelerate corrosion, and galvanic corrosion that is caused by the contact between dissimilar metals in the presence of an electrolyte. Stress corrosion cracking (SCC) is another concern, where the combination of tensile stress and a corrosive environment leads to cracking.
Understanding these corrosion mechanisms is crucial for selecting the appropriate prevention and mitigation strategies by emphasizing the need for a comprehensive approach that addresses the various forms of corrosion pipelines may encounter.
Strategies for Corrosion Prevention
To mitigate these risks, several strategies are essential:
- Pipeline Coatings: A primary defense against external corrosion that provides a barrier between the pipe material and corrosive elements.
- Cathodic Protection: An electrochemical process that mitigates external corrosion by applying a direct current to the pipeline, effectively making it the cathode of an electrochemical cell. This technique helps in significantly reducing the corrosion rate.
- Corrosion Inhibitors: Chemical compounds that, when added to the transported fluid, decrease the rate of internal corrosion. These inhibitors form a protective film on the inner walls of the pipeline to prevent corrosive substances from directly attacking the pipe material.
- Regular Inspection and Maintenance: Consistent inspection and maintenance practices are crucial in identifying and addressing potential corrosion issues before they escalate. These procedures may include monitoring corrosion rates, performing visual inspections, conducting non-destructive testing, and implementing remedial actions when necessary.
Polyguard Solutions for Corrosion Control in Oil and Gas Pipelines
Polyguard's approach to combating pipeline corrosion is rooted in innovation and efficacy, which is demonstrated through their specialized product lineup that includes:
IRO™ (Impact Resistant Outerwrap)
The Polyguard IRO™ (Impact Resistant Outerwrap) is a fiberglass wrap made with water-activated resin to provide impact abrasion and mechanical protection for pipes. It's designed for quick hardening and is applied over various coatings like RD-6, Epoxy, and Polyethylene sleeves.
The application process involves wetting areas for wrap, applying IRO with specific overlaps, and using compression film with a unique wrapping technique for enhanced protection. Special considerations are given for cold and hot weather installations to ensure the IRO's adaptability to different environmental conditions.
NHT-5600™
NHT-5600™ 2-part epoxy is a cutting-edge, 100% solids, and VOC-free epoxy coating designed for comprehensive pipeline protection. It enhances the protection of FBE coated pipes by covering field joint girth welds, valves, and fittings, and is suitable for directional drills and road bore pipe applications. This epoxy excels in coating rehabilitation of existing pipelines for a robust barrier against corrosion.
Its application involves careful storage, surface preparation to achieve a near-white finish, and application specifications to ensure a uniform and durable coating, including specific conditions for curing and repairs.
CA-9™ Mastic
CA-9™ Mastic is a highly effective, cold-applied protective coating designed to safeguard against corrosion in oil and gas pipelines. It is a viscous, fiber-reinforced mastic that is uniquely formulated to coat flanges, fittings, and other irregular pipeline configurations in order to provide a durable barrier against corrosive environments.
Apply CA #9 Mastic using a brush, roller, or trowel. Typically, CA #9 is applied in two coats. Ensure that the first coat is dry to the touch before applying the second coat. Coverage: Approximately 60 square feet per gallon.
Explore Polyguard's Cutting-Edge Corrosion Control Solutions
Polyguard’s comprehensive suite of corrosion control solutions stands at the forefront of protecting the integrity of pipelines within the energy sector. Our technology is engineered to provide corrosion control in oil and gas pipelines and extend the lifespan of pipelines, mitigate environmental risks, and ensure uninterrupted flow of resources.
We invite industry professionals, engineers, and maintenance teams to explore the range of solutions from Polyguard..
Contact us today for more information!